"Zet de muziek aan en nodig mensen uit om te dansen"
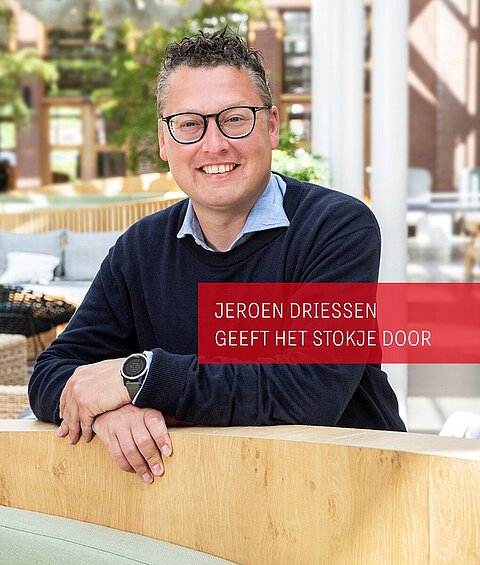
In de Brainportregio bruist het van talent. De campagne ‘Je hebt meer talent in huis dan je denkt’ van Brainport Eindhoven x PSV inspireert mensen om hun talent te ontdekken en bedrijven om anders naar talent te kijken – voor een toekomst waarin iedereen meedoet.
Lees meer over deze campagneBrainport Eindhoven is een toonaangevende technologische regio waar innovatie bijdraagt aan maatschappelijke uitdagingen zoals energie, mobiliteit en gezondheid. Met 21 gemeenten en 800.000 inwoners is het klein in omvang, maar met een grote, wereldwijde impact.
Lees meer over Brainport EindhovenHet Brainport Partnerfonds versterkt de regio met investeringen van bedrijven. Samen werken ze aan bereikbaarheid, betaalbare woningen, technisch talent, een sterke arbeidsmarkt en sociale cohesie. Dit zorgt voor duurzame groei en een goede balans tussen welvaart en welzijn.
Lees meer over het Brainport PartnerfondsDoor onze unieke hightech competenties en de krachtige samenwerking tussen bedrijfsleven, onderwijs- en kennisinstellingen en overheden is Brainport Eindhoven uitgegroeid tot een economische kernregio. Samen realiseren we innovaties voor de maatschappelijke vraagstukken van vandaag en morgen.
Lees meer over Brainport voor InnovatieInnovatiehuis de Peel, Kempisch Ondernemers Platform, WTC Eindhoven Brainport en Brainport Development slaan de handen ineen om mkb-ondernemers verder te helpen. Samen vormen zij Brainport voor MKB: hét loket voor vragen rondom groei, personeel, verduurzaming en digitalisering.
Lees meer over Brainport voor MKBDe Brainportregio zet volop in op onderwijsinnovatie om leerlingen en studenten klaar te stomen voor een toekomst vol technologie en internationalisering. Ontdek inspirerende activiteiten, tools en samenwerkingen op het platform waar onderwijs en bedrijfsleven de krachten bundelen.
Lees meer over Brainport voor OnderwijsGelijke kansen voor iedereen. Dát is het doel van Brainport voor Elkaar. Onze vereniging van sociaal werkgevers verbindt bedrijven, maatschappelijke organisaties, gemeenten en onderwijs. We bundelen onze krachten en werken samen aan sociaalmaatschappelijke vraagstukken in de regio.
Lees meer over Brainport voor ElkaarAan de hand van een gezamenlijke agenda werken bedrijven, onderwijs- en kennisinstellingen en overheden in Brainport intensief samen aan het versterken van de regio. Het behouden van een goede balans tussen technologie, talent en woon- en leefklimaat is hierbij het uitgangspunt.
Lees meer over Strategie & OrganisatieDe Brainportregio biedt volop kansen en mogelijkheden, voor iedereen. En als je iets doet waar je plezier in hebt, dan maak je automatisch gebruik van jouw talenten.
Lees meer over deze publiekscampagneSamen werken we hier aan allerlei onderwerpen. Sluit je aan, schrijf je in en blijf op de hoogte van ontwikkelingen en relevante evenementen.
Meld je aanStrijp-T, gebouw TQ5, ingang 6, 3e verdieping
Achtseweg Zuid 159H
5651 GW Eindhoven