Govers Accountants / Adviseurs are locally involved in Brainport growth
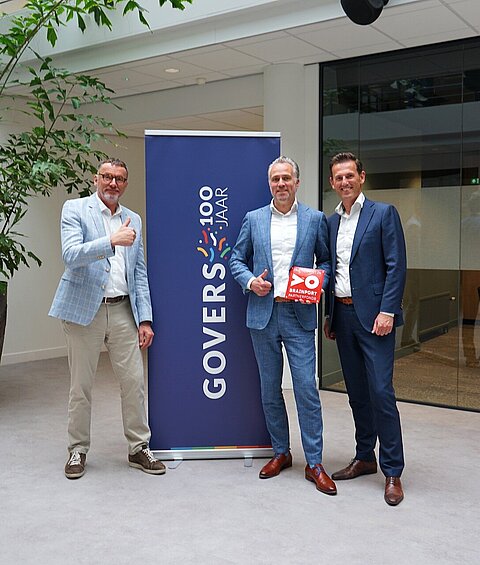
For new markets (drones, unmanned vehicles, aerospace), additive manufacturing has already become the first choice. In more traditional sectors, a bit more time was needed to reach that point.
KMWE was one of the initiators and the first tenant for Brainport Industries Campus (BIC) in Eindhoven, the Netherlands. Yet some crucial parts of the high-tech manufacturing company remained for years in the Strijp-T district, where KMWE concentrated its aerospace activities. That will soon end: a move to BIC will begin in early 2023. At the same time, a new space will be set up in the field of 3D printing, a technique that KMWE has developed with partners over the past nine years. By the end of next year, the move should be fully completed.
In addition to the logic of concentrating activities in one place, CEO Edward Voncken has another important reason for the decision to move to BIC: “We see that additive manufacturing, the technology that makes 3D printing possible, has now moved beyond the stage of hype. This paves the way for us to make serious investments in this sector. What is extra nice about this is that we can rent a space within Brainport Industries Campus that is right next to our other one and that BIC has now developed into the place where many other companies are working on developments in 3D printing.”
For decades, KMWE has developed itself as the party that uses machining to make the most complicated parts and products for various parties within the high-tech manufacturing industry. “In doing so, we naturally kept our eyes open for additional manufacturing methods, and certainly, in recent years, we have seen that 3D printing has made serious inroads. Initially, this seemed to apply only to prototypes or very small series, but it is now clear that larger series can also be manufactured via additive manufacturing.”
The big difference between classic machining technology and 3D printing is that with machining, the manufacturer starts with a large chunk of metal and cuts away so much from it that, eventually, the desired product remains. 3D printing works the other way around: you start with nothing and build the desired product step by step. The most significant advantages are freedom of form (specific shapes that could not be manufactured before can now) and lower environmental impact (machining creates a lot of waste in the form of the “curls” that are cut from the source material). 3D printing can also be done with a wide range of materials: from simple plastics, which we are also familiar with from home 3D printers, to ingenious metal alloys, which go into the machine in powder form.
For new markets (drones, unmanned vehicles, aerospace), additive manufacturing has already become the first choice, simply because there is no need to compare the result with previous production processes. In more traditional sectors, it is often waiting until a new model is needed. It takes a little more time to convince this group of users that the new technology can deliver the same performance as the old one. “When the need is higher, for example, due to time constraints or the requirements of an important customer, they often change their position,” Voncken knows.
This change is only a matter of time, says Rob van Loon, responsible for the technological development of additive manufacturing at KMWE. “We have seen the obstacles for a long time already, and were able to find the solutions and further development in recent years. Our customers are now reaping the benefits of this. In itself, of course, it is not surprising that there is some hesitation among users. Casting and milling have been around for a hundred years, the users know the quality through and through. With new technology, you have to wait and see, of course. But now everyone sees that the advantages are enormous: our data show that we can deliver at least the same quality, but lighter, in exactly the shape they need, and also much faster.”
According to Voncken, the latter has only become all the more visible with the increasing scarcity in the supply chain. “We all know the stories. As a result of Corona and the war in Ukraine, there are considerable issues in the supply chain: critical materials are in short supply, and energy prices are skyrocketing. As a result, lead times can sometimes be as long as 30 to, in extreme cases, 60 weeks. With 3D printing, thanks to powder technology, that’s two weeks at most. That’s quite a difference.”
Because the technology behind the process has been digitized even further, it also benefits KMWE’s human resources department. “No or much less manual capacity is needed for many steps in this process because all the knowledge is already in the software we use to power that machine. A production run, on average, takes about two and a half days continuously, and is fully automatic. Taken together, this means a huge improvement in lead time.”
The new production facility at BIC will include several SLM machines, with which KMWE has succeeded in turning a significant client into a partner as well. To keep the purity of the end products optimal, there will be separate production lines for each machine. Van Loon: “The composition of the powder that serves as raw material needs close attention; you don’t want to have any mixing with other powders. By always keeping the same composition on a single machine, you can be sure that the material remains pure.” In addition to the manufacturing of new products, there is also room for the repair of damaged products and thermal spraying, something that is especially important in aerospace.
BIC has developed in recent years as an essential hub for 3D printing. Some 25 AM companies are already actively collaborating fully on design and development. Voncken is already sure that KMWE will be part of this. “Of course, no doubt that much of our R&D will take place there, but also in our own labs. And conversely, we will also be able to be of value to the other 3D companies here on campus. Having all this knowledge and experience so close together here is an advantage for everyone.”
For the foreseeable future, additive manufacturing will only become more important in the high-tech manufacturing industry, Voncken expects. “What plays an important role is that we can use our processes for existing and new markets. And because circularity is more attainable with additive manufacturing, we will have even more opportunities.”
The expertise KMWE has accumulated in both old and new technologies could even be an added advantage. Voncken, laughing: “If we could melt down all those curls left over from the machining process into raw material for the 3D printing machines, that would, of course, be fantastic. Then you’re talking about tons of curls a week.” But, he immediately adds, that is no more than a prospect at this point. “First, let’s finish the whole move and expansion of our operations in BIC properly.”