What could possibly go wrong?
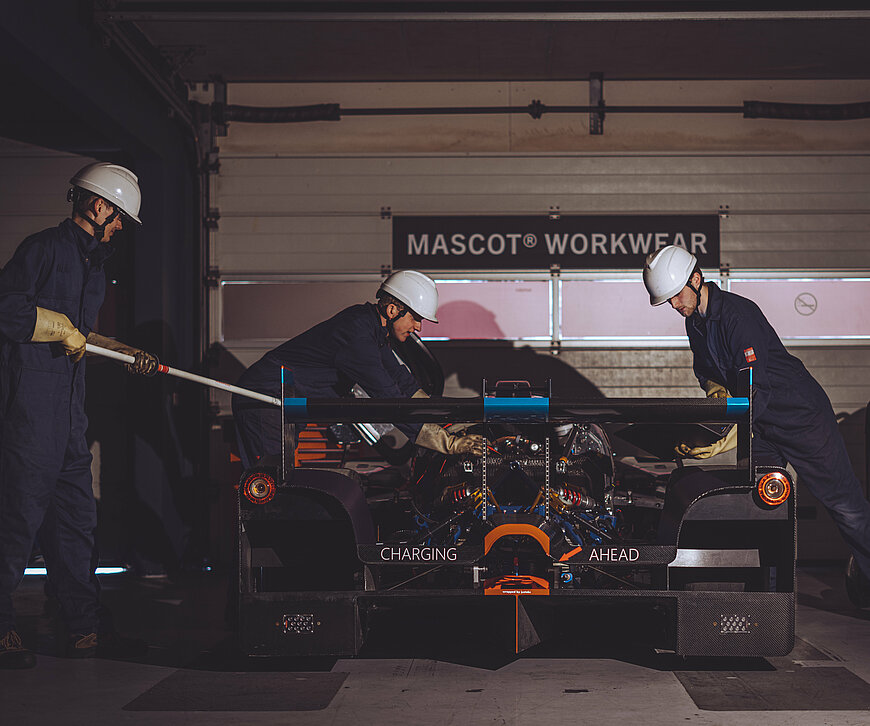
What could possibly go wrong?
Over the past year, InMotion has made remarkable progress in the development of their Next Generation Battery Pack (NGBP). One of the key milestones for the team was designing their own battery modules, a key innovation that allowed them to achieve an unprecedented charging time of 4 minutes.
As a team, InMotion is extremely proud of these achievements, but more importantly, it marks a significant step forward within the automotive industry to revolutionize battery charging speeds. In July 2023, students completed the first round of performance tests on these modules, validating their capabilities in a controlled environment. These tests confirmed that the design met the strict requirements that had been set.
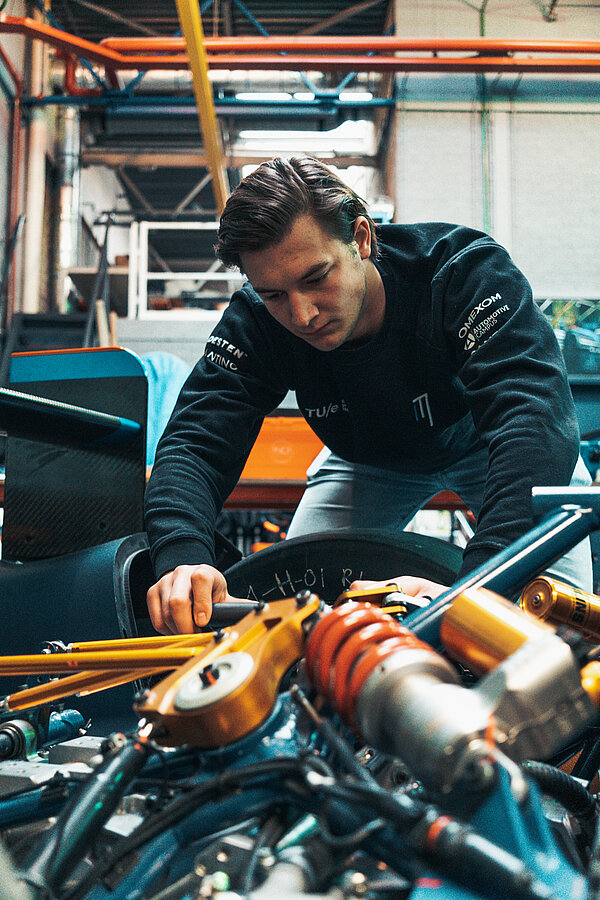
The next team was installed in the new academic year. This shifted the focus to scaling up the modules and integrating them into a complete battery pack, suitable for the demanding conditions of racing. However, this process did not go as the new team expected. The transition from a controlled test environment to the harsh reality of a racing scenario exposed quite a few critical issues that needed to be addressed first. Ensuring sufficient electrical insulation at higher voltages proved particularly challenging; when scaling up from a single module to a complete package at 800 Volt, the requirements for electrical insulation increased considerably. Materials that were non-conductive at lower voltages suddenly became conductive at higher voltages, necessitating a complete overhaul of our insulation strategies.
In addition, the sustainability of the cooling system turned out to be a crucial point of attention. Although the system performed well in a controlled environment, it had to be robust enough to withstand the harsh conditions of a race, where leaks and system failures could have disastrous consequences. Designing a cooling system that could function under the extreme conditions of a race – where vibration, heat and physical stress are constantly present – was a significant challenge. Extensive testing and refinement was required to ensure that the cooling system could maintain safe temperatures within the battery pack, both while charging and while racing, without sacrificing performance or safety.
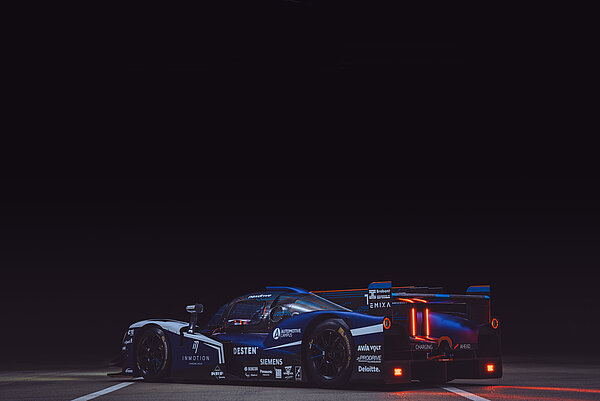
Despite all these setbacks with the battery pack, the team has managed not to give up. In addition to the battery pack, InMotion also made significant upgrades this year to the powertrain, which is responsible for converting the battery's energy into speed on the track. This upgrade included an extensive revision of the car's rear subframe, to which the drivetrain is attached. To ensure that the new frame could withstand the forces of racing, extensive material research was carried out and numerous simulations were carried out.
Another milestone for InMotion this year was the successful implementation of their innovative cooling system – which has been in development within the team for several years – which was finally tested and integrated into the Revolution. The so-called Refrigerant Loop is actually the car's large refrigerator, which keeps the battery pack at the right temperature during both charging and racing.
In short, InMotion's past year was all about trial and error. Although the student team was often confronted with problems and unforeseen situations, this of course also led to new insights. In any case, the student team has gained a lot of practical knowledge about the complexity of battery packs and the course of technical design processes.