Govers Accountants/Adviseurs zijn lokaal betrokken bij Brainportgroei
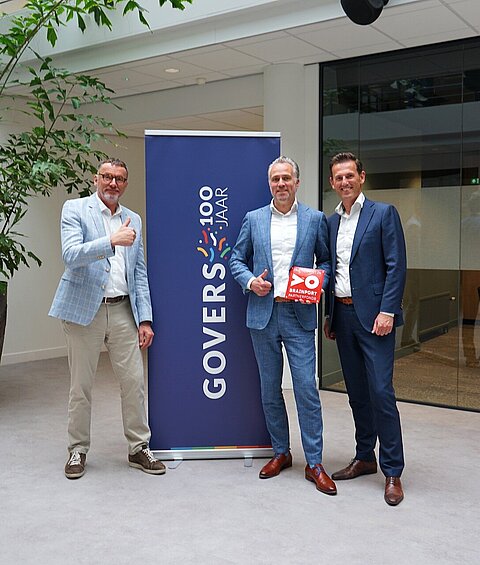
Voor nieuwe markten (drones, unmanned vehicles, aerospace) is additive manufacturing al een eerste keus geworden. Voor traditionele maakbedrijven is dat een kwestie van tijd.
KMWE was een van de initiatiefnemers en de eerste huurder voor Brainport Industries Campus (BIC). Toch bleven enkele belangrijke onderdelen van het high-tech maakbedrijf nog jarenlang op Strijp-T, waar KMWE de aerospace activiteiten heeft geconcentreerd. Daar komt binnenkort een einde aan: begin 2023 start een verhuizing naar BIC. Tegelijkertijd wordt er een nieuwe ruimte op gebied van 3D printen ingericht, een techniek die KMWE tot nog toe samen met partners over de afgelopen 9 jaren heeft ontwikkeld. Eind volgend jaar moet de verhuizing helemaal zijn afgerond.
CEO Edward Voncken heeft, naast de logica om de activiteiten te concentreren op één plek, nog een belangrijke reden voor de verplaatsing: “We zien dat additive manufacturing, de technologie die 3D printing mogelijk maakt, het stadium van hype inmiddels is ontstegen. Dat maakt voor ons de weg vrij voor serieuze investeringen in deze sector. Extra mooi is het daarbij dat we een ruimte binnen Brainport Industries Campus kunnen huren die direct naast onze andere ligt én dat BIC zich inmiddels heeft ontwikkeld tot de plek waar heel veel 3D printing development zich heeft geconcentreerd.”
KMWE heeft zich decennialang ontwikkeld als de partij die met verspaning de meest ingewikkelde onderdelen en producten kon maken, voor diverse partijen binnen de high-tech maakindustrie. “Daarbij hebben we vanzelfsprekend onze ogen open gehouden voor aanvullende vervaardigingsmethoden en zeker de laatste jaren hebben we kunnen zien dat 3D printing een serieuze opmars heeft gemaakt. Aanvankelijk leek dat alleen voor prototypes of heel kleine series op te gaan, maar inmiddels is wel duidelijk dat ook grotere series via additive manufacturing kunnen worden vervaardigd.”
Het grote verschil tussen klassieke verspaningstechnologie en 3D printing is dat de producent bij verspaning begint met een groot brok metaal en van daaruit zoveel wegsnijdt dat uiteindelijk het gewenste product overblijft. 3D printing werkt net andersom: je begint met niks en bouwt stap voor stap het gewenste product op. De grote voordelen daarbij zijn de vormvrijheid (bepaalde vormen die voorheen niet vervaardigd konden worden, kunnen dat nu wel) en de lagere milieubelasting (bij verspaning ontstaat, in de vorm van de ‘krullen’ die weggesneden worden uit het bronmateriaal, veel afval). 3D printen kan bovendien met een breed scala aan materialen gebeuren: van eenvoudige plastics, die we ook wel kennen van de 3D printers in de huiskamer, tot ingenieuze metaallegeringen, die in poedervorm de machine in gaan.
Voor nieuwe markten (drones, unmanned vehicles, aerospace) is additive manufacturing al een eerste keus geworden, eenvoudigweg omdat daar geen vergelijking hoeft te worden gemaakt met voorgaande productieprocessen. In traditionelere sectoren is het vaak wachten tot er een nieuw model nodig is. Het kost iets meer tijd om deze groep gebruikers ervan te overtuigen dat de nieuwe technologie dezelfde prestaties kan leveren als de oude. “Als de nood hoger is, bijvoorbeeld door tijdsdruk of de eisen van een belangrijke klant, gaan ze overstag”, weet Voncken.
Dát ze overstag gaan is slechts een kwestie van tijd, zegt ook Rob van Loon, die bij KMWE technisch verantwoordelijk is voor additive manufacturing. “Wij hebben afgelopen jaren de obstakels al lang en breed gezien, de oplossingen en de doorontwikkeling gerealiseerd. Daar plukken onze klanten nu de vruchten van. Op zich is het natuurlijk niet zo gek dat er enige reserve zit bij de gebruikers. Gieten en frezen bestaat al honderd jaar, ze kennen de kwaliteit daarvan door en door. Van een nieuwe technologie moet je dat nog maar afwachten natuurlijk. Maar inmiddels ziet iedereen dat de voordelen enorm zijn: onze data tonen aan dat we minimaal dezelfde kwaliteit kunnen leveren, maar dan lichter, in exact de vorm die ze nodig hebben en ook nog eens veel sneller.”
Volgens Voncken is dat laatste alleen maar zichtbaarder geworden door de toenemende schaarste in de toeleveringsketen. “We kennen de verhalen allemaal. Als gevolg van Corona en de oorlog in Oekraïne zijn er behoorlijke issues in de supply chain: er is schaarste aan kritische materialen en de energieprijzen gieren de pan uit. Het gevolg is dat de doorlooptijd soms wel 30 tot, in extreme gevallen, 60 weken kan oplopen. Bij 3D printing is dat, dankzij de poedertechniek, hoogstens twee weken. Dat is nogal een verschil.”
Omdat de technologie achter het proces nog verder is gedigitaliseerd, levert ook voordelen op voor de afdeling personeelszaken van KMWE. “Er is voor veel fasen geen of veel minder manuele capaciteit nodig, alle kennis zit namelijk al in de software waarmee we die machine hebben gevoed. Een productierun, die gemiddeld zo’n tweeëneenhalve dag volcontinu duurt, is volledig automatisch. Dat alles betekent een enorme verbetering van de lead time.”
De nieuwe productiefaciliteit bij BIC zal straks diverse SLM-machines bevatten, waarmee KMWE erin is geslaagd van een belangrijke klant ook een partner te maken. Om de zuiverheid van de eindproducten optimaal te houden, komen er per machine aparte productielijnen. Van Loon: “De samenstelling van het poeder dat als grondstof dient luistert enorm nauw, je wilt geen vermenging met andere poeders hebben. Door altijd dezelfde samenstelling op een machine te houden, weet je zeker dat het materiaal zuiver blijft.” Naast de vervaardiging van nieuwe producten is er ook ruimte voor reparatie van van beschadigde producten en voor thermisch spuiten, iets dat vooral in aerospace van belang is.
BIC heeft zich de afgelopen jaren weten te ontwikkelen als een belangrijke hub voor 3D printing. Er zijn al zo’n 25 AM-bedrijven actief, volop samenwerkend rond design en development. Ook KMWE gaat daar veel gebruik van maken, weet Voncken nu al. “Vanzelfsprekend zal veel van onze R&D aan de andere kant van het pad plaatsvinden, maar ook in onze eigen labs. En omgekeerd zullen wij ook van waarde kunnen zijn voor de overige 3D-bedrijven hier op de campus. Hoe dan ook is het voor iedereen een voordeel om al die kennis en ervaring hier zo dicht bij elkaar te hebben.”
Voor de nabije toekomst zal additive manufacturing alleen maar belangrijker worden in de high-tech maakindustrie, verwacht Voncken. “Wat daarbij een belangrijke rol speelt is dat we onze processen zowel voor bestaande als voor nieuwe markten kunnen inzetten. En omdat circulariteit met additive manufacturing beter bereikbaar is, komen er nog meer kansen voor ons.”
De expertise die KMWE in zowel oude als nieuwe technologieën heeft opgebouwd zou wat dat betreft nog wel eens een extra voordeel kunnen opleveren. Voncken, lachend: “Als we al die krullen die achterblijven uit het verspaningsproces nu eens zouden kunnen omsmelten tot grondstof voor de 3D printing machines, dan zou dat natuurlijk helemaal geweldig zijn. Dan heb je het over tonnen aan krullen per week.” Maar, zo zegt hij er direct bij, dat is op dit moment nog niet meer dan een vergezicht. “Eerst maar eens de hele verhuizing en uitbouw van onze activiteiten in BIC goed afronden.”