Roads, paths, junctions and hubs: how Brainport Eindhoven wants to get mobility on track
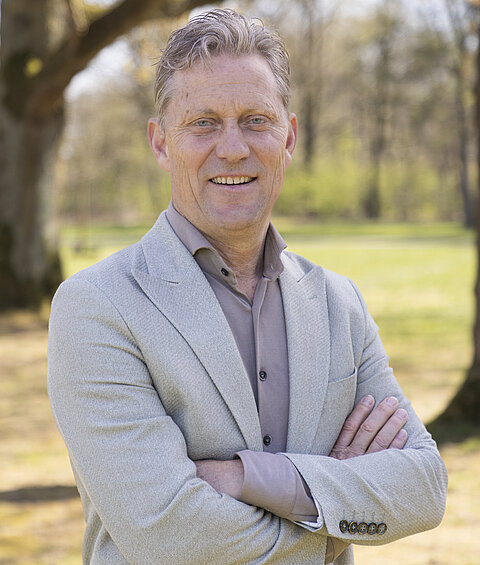
Now, charging your electric car takes 20 to 45 minutes in most cases. But soon you might just be able to get back on the road after paying for a Snickers and a quick visit to the toilet. Yesterday, TU Eindhoven (TU/e) student team InMotion unveiled an electric race car with a charging time of just 3 minutes and 56 seconds.
The battery pack has a charging power of 322 kW, a total capacity of 29.2 kWh, and a range of 250 kilometers. The team managed to cut 66 percent off the charging time in the past 2.5 years – last year it was 12 minutes. As far as is known, it is the fastest-charging long-distance electric race car in the world.
On the other side of the screen are team manager Julia Niemeijer and partnership manager Hieke van Heesch. They have had a “rather hectic year.” Queen Maxima, Minister Harbers, and CEOs of major car manufacturers; all listened to the story of InMotion, based at the Automotive Campus in Helmond.
“We almost all live in Eindhoven, but occasionally dragged mattresses and sleeping bags here so we could work through the night,” Van Heesch says. It characterizes the passion of the 30-member team. For example, the delivery of a coupling piece for the cooling solution was delayed just before an important deadline in the production process. “We heard about that on Wednesday evening, and six o’clock the next morning two team members were on their way to the United Kingdom to go get the part themselves then.”
The key to the revolutionary charging time is in the innovative cooling technology. When a battery pack is charged quickly, a lot of heat is released. Heat is bad for batteries: it causes battery degradation and you lose range. Previous years’ student team developed an innovative cooling technology at the battery module level, placing cooling plates with coolant between the modules.
To get the heat out of the battery pack even better, InMotion yesterday presented a new method, which allows them to cool at the cellular level. Niemeijer: “Coolant now flows between all the cells. So we can now cool the cells individually. This ensures an extended lifespan and also repeated fast charging is no longer harmful to the battery this way.” The team did multiple tests where they (dis)charged the car at race pace for 24 hours and saw no degradation. Exactly how the system works, the team is keeping secret.
Cooling at the cell level is not yet common in electric cars, so InMotion also developed its own modules. “Our technology works at the cell level. There are only a few millimeters between cells, so we really worked on a very small scale,” Niemeijer said. “In addition, it was also a big challenge to integrate our system into the battery box that was developed in previous years,” Van Heesch adds to her teammate. “You only have one year, we can’t reinvent everything and focus on where the innovation is.”
Getting everything ready in time for the presentation that year was a tough job. “Actually, by definition, you set unrealistic goals. But on the other hand, you also want to achieve something in one year. I have eaten at the office more often this year than at home, we can cook very creatively with our sandwich iron,” Van Heesch laughs.
Whereas the current system is specifically designed for race cars, the students want to make electric driving easier – and thus more accessible – to consumers. This summer, the team will make the car roadworthy and test it on the track. The challenges that result will be used by the next batch of InMotion graduates. The team has implemented the technology in an LMP3 race car. The ultimate goal? “Competing in the Le Mans 24-hour race, so we can test our battery pack under the toughest conditions. That is why we have already implemented our technology in an LMP3 race car, the Le Mans prototype class,” Niemeijer replied.