How TNO transformed from broad innovation within 3D printing to specific breakthroughs in food and pharma
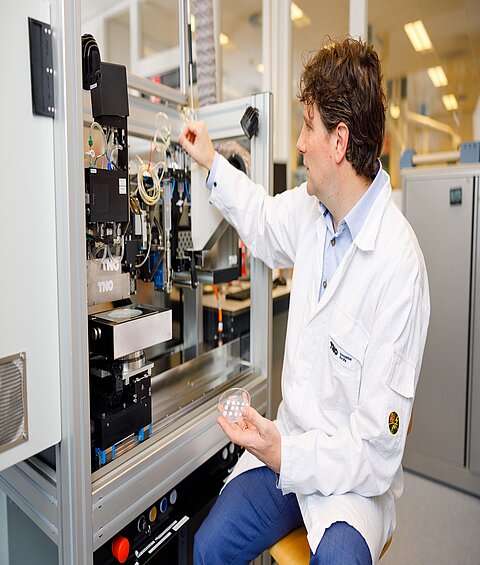
At the heart of most electrical devices are printed circuit boards (PCBs). These thick and sturdy – often green – boards host circuits and are what can be considered the brain of a remote control, a blender, or a TV screen. Instead of having rigid boards, more and more devices need thinner and possibly flexible solutions. The city of Eindhoven, the Netherlands, recently became home to a new factory for bending electronics.
TracXon, a spin-off from the imec and TNO-partnered Holst Centre, opened its foundry to produce hybrid printed electronics. These artifacts are the end result of a manufacturing process that uses conductive inks to print circuitry on materials like plastics and fabric. In the case of the Holst Centre spin-off, printing happens on thin plastic foils.
Using this substrate to embed electronic components opens up a vast array of possibilities. Lighting, health monitoring devices, and electric vehicles battery management systems, thin and bending circuitry can serve them all. Moreover, this technology makes more efficient use of materials, using less of them and choosing glues and inks that can be recycled at their end of life.
All these advantages come without compromising on the product’s accuracy. “The printers at our disposal allow us to achieve maximum detail. Every dot counts here, otherwise, the circuitry will not work. We can achieve pixel-size quality, thanks to the combination of materials, processes, and people”, underlines Ashok Sridhar, CEO of TracXon.
An over 20-meter-long clean room hosts the roll-to-roll production line. All the necessary equipment is stacked in close succession. “Here we can continuously print hundreds of meters of circuitry”, explains one of TracXon’s employees amid the hubbub produced by the machinery. There, foil spools slowly unwind, as they proceed through the line. First comes the printing, with the robotic head scanning the foil and then injecting circuitry. A few seconds later, the foil reaches the curing station, where – like any charcuterie’s ham drying facility – air blows at a controlled temperature. This prevents boards to stick while drying the freshly printed boards.
This production line will soon include machinery for light treatment of the flexible circuit boards between printing and curing. Once the curing is over, the foils are ready to be laser-cut – either by TracXon itself or their customers, depending on their will.
In the assembly lab, electric components are placed on the printed film. Foils pass under a robot that accurately scans them, understanding where to place every little component. After spraying glue, the printer uses a vacuum to pick and place the components. The boards then pass through an oven to dry. Both printing lines assure accuracy, as the company is eyeing laser circuitry printing as the next addition to its capabilities.
Some of the customers who chose the Holst Centre’s spin-off also attended the opening event. One of them is the German MinkTec, which is developing a flexible sensor strip that can measure its shape and display it on devices. One of the use cases is using the strip for detecting back posture. The smart strip features hybrid printed electronics by TracXon that enable shape tracking.
Another domain the Eindhoven-based company is catering to is battery management systems. On thin strips of foil, they integrated circuitry to keep track of battery status. Being flexible and adaptive, strips could be integrated into every battery cell, instead of having a single sensor for the whole pack. This would result in enhanced control of the battery status, pinpointing – thus replacing – only defected cells.
Given the vast number of solutions hybrid printed electronics offer, TracXon aspires to transform this manufacturing technology from a niche to a mainstream one. As of today, PCB technology is still the go-to solution for most companies.
“However, nobody else can print flexible electronics as TracXon does”, states Ton van Mol, managing director of TNO at Holst Centre. “Having set up this production line proves that high-end products can be manufactured this way. The combination of printing and assembling in one factory is something almost unique in the world”, he adds.
On the other hand, Sridhar himself believes that a strong partnership with TNO will be key to the company’s future success. “Being backed and collaborating with them – who have over 20 years of experience with technologies – allows us to bring innovation from lab to fab. Additionally, the region’s ecosystem is a great advantage for us too, since many actors are exploring and thinking about adopting this technology”, TracXon’s CEO underlines.
"The combination of printing and assembling in one factory is something almost unique in the world"
Ton van Mol, CEO of TNO at Holst Centre
Seeing the developments in hybrid printing technology, the decision to take a step forward came naturally. “We believe this is going to be big. Our intent was not to set it up for small-scale production but to become the biggest company in this market space in the next five years. In this span of time, we would like to change the industry’s mindset. Many applications become possible with this technology, and we want to be the first to do so”, firmly states Sridhar.
In the short-term future, TracXon will focus on two application domains: healthcare and automotive. As the company fits in its new production setting, it will specialize in these two sectors first, optimizing production and accommodating the rising number of customers.
In the main picture, © TracXon's roll-to-roll production line