How TNO transformed from broad innovation within 3D printing to specific breakthroughs in food and pharma
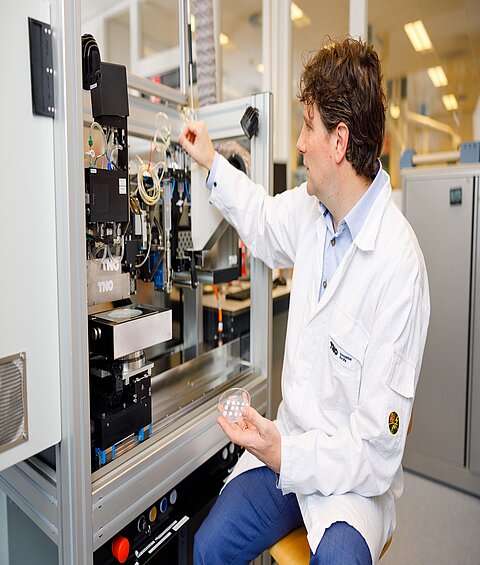
The high-tech industry in the Benelux is embracing additive manufacturing after years. The group of high-tech suppliers adding 3D metal printing to their technology portfolio is growing. How important is their knowledge of the whole AM process to achieve successful applications?
Belgian Melotte, one of the exhibitors at AM for Production (29 March), was at the time one of the first precision toolmakers in the Benelux to bring 3D metal printing in-house. In recent years, the supplier has noticed that AM projects are coming back on a regular basis. "From exploratory, it has gone to a known process," says Bram Grandjean, account manager. At Wilting, which commissioned the first AM systems two years ago, demand is higher. Series production of manifold-like products runs on both systems. "Customers are increasingly recognising how an AM part can improve the functionality of their machine, for example in terms of the flow of a gas or liquid or heat capacity," says Remon Haarsma, AM engineer.
Demand is increasing to such an extent that Wilting expects to expand its AM capacity this year, also because this offers the opportunity to offer stainless steel as a third material. KMWE also sees demand for serial production with additive manufacturing taking off. This is why the supplier is investing in its own AM capacity this spring. Edward Voncken, CEO, feels that the supply chain problems of the past few years have accelerated adoption. For casting and forging parts for the aerospace industry, you're talking leadtimes of 60 weeks these days. "With 3D printing, that's days rather than weeks," he says. Moreover, customers now order the quantities they need; not 100 pieces because the foundry sets that as the lower limit.
So the acceptance of additive manufacturing has improved. But what about the specific design knowledge: has it landed with the OEMs or do suppliers have to provide it? That varies, it turns out. Overall, more and more companies have AM expertise in-house and are designing with the aim of maximising the benefits of the technology. "We see more and more customers recognising the added value and making real functional improvements in their products with AM," says Remon Haarsma. He notes that some engineers have already gained the necessary experience with 3D metal printing; senior engineers, in turn, are more often more familiar with conventional machining techniques. Suppliers prefer to sit down with their customers as early as possible to work with their customers' design engineers. "It's not wrong to have engineers ping-pong in the design phase about what the effect is if you do this or that," says Bram Grandjean. From the supplier's expertise, details can be added that improve manufacturability, for example adding a rib to prevent distortion of the product due to heat input.
Indeed, the design of the part has a lot of influence on printability, more so than with other production techniques. "If we are involved too late in the design process, more effort is needed to make the part printable. And sometimes we conclude afterwards that more could have been achieved in terms of functionality," says Adwin Kannekens, commercial director at Andra Tech Group, to which Wilting belongs. Thinking along about design is a balancing act on a thin rope. Rob van Loon, AM engineer at KMWE Precision, always wants to know what comes before and after the part the customer wants printed. To see if parts can be integrated into one whole. He does this not only to save costs. "Sometimes you can't meet the requested tolerances per part but you can with the composition," he says. Still, this remains a delicate balancing act, Adwin Kannekens believes. Against the cost savings in assembly are the higher costs in the AM process. "For the customer, cost is ultimately euros at the bottom of the line," he says.
''We see more and more customers recognising the added value and making real functional improvements in their products with AM"
Remon Haarsma, AM engineer at Wilting
Is the communication between supplier and OEM different when it comes to AM parts compared to milling and turning parts? Peter Perremans (Melotte) thinks there is more frequent contact with the customer for AM parts, but he does not see any substantial differences here from work for the other techniques Melotte uses. "The type of products we are in always requires consultation. A tolerance of a few microns is easy to put on a drawing, but not always easy to make and certainly not when you are dealing with deformation-sensitive 3D printed parts. Do you really need that tolerance? Complexity towards manufacturability determines the price," says Peter Perremans. He and Bram Grandjean do welcome early involvement. 3D metal printing is a very different process from milling, turning, grinding and the other operations that high-tech suppliers perform every day. Support, for example, is such a special issue, which can have a big impact on manufacturability and cost price. Orientation plays a big role in this. The same applies to whether or not tensions arise. And then for the manifold-like products that Wilting produces: how do you remove all the powder particles from the internal channels? Are these questions you are saddling the customer with? Adwin Kannekens doesn't think so. The manufacturability knowledge and the knowledge of post-processing 3D-printed parts flow together at the supplier. "We shouldn't expect the customer to think about support, but we should expect orientation because then you know whether certain features are printable or not."
Rob van Loon, AM engineer at KMWE, prefers to call communication "different". He says: "Just because a miller starts with a semi-finished product. We still have to define the starting points." He thinks that especially the combined knowledge of additive manufacturing and machining finishing is an asset of high-tech suppliers. For example, by positioning the part in a certain way, support material can be avoided. That saves post-processing. Or by including a fixture in the design in such a way that it does not have to be removed afterwards. KMWE prints a dovetail joint along so that the parts can be placed directly in the machine clamp of the CNC machine. "This makes milling as post-processing less man-dependent. Clamping up takes a few more minutes and the piece sits well. By sometimes printing 20% more, we reduce the total milling time by half," he gives as an example. Thinking along in the preliminary process can save dozens of percent in cost price. These are things where the AM supplier's expertise can create value for the customer. "Thinking along from the beginning saves headaches in the production process."
''By sometimes printing 20% more, we reduce the total time of milling by half"
Rob van Loon, AM engineer at KMWE Precision
Anno 2023, you could say that additive manufacturing has - finally - taken off in the Dutch high-tech industry. The flywheel to get additive manufacturing going further is to convince design engineers even more of the added value the technology can offer. "The rest are challenges for which there are solutions," thinks Adwin Kannekens. Quality control and assurance need no longer be an issue, believes Rob van Loon. If you control the whole process and are critical of how you 3D print parts, you don't need to measure everything after the fact. "The first step is never changing materials and the second step is periodically testing powder. Know what is in the machine; traceability from powder to finished product, then you don't need to measure everything after." The biggest brake on the breakthrough, according to Adwin Kannekens, is the shortage of CNC practitioners. Wilting is set on unmanned production; it also prefers to finish AM workpieces unmanned. 3D printing unmanned for 48 hours or more and then needing a CNC specialist for 20 hours to post-process the pieces is not Wilting's choice. "In terms of cost, it's a world of difference whether you do manned or unmanned post-processing. Before we put in the third 3D metal printer, we want to make big steps to make the milling process operator-independent."
What is still holding 3D metal printing back? Actually nothing, as long as you have the right application in which the benefits emerge. Peter Perremans remembers articles 15 years ago predicting that there would be a print shop on every street corner to pick up parts. "We are a long way from that. Certainly for the first 10 years, the technology will remain complementary to conventional technology." Additive manufacturing comes into its own especially for very organic shapes, integrating functions to reduce the number of components and extreme weight savings. "Then AM is worth its money," says Perremans. But any price tag also has its effect on usability. That is where he still sees an obstacle. "If the process does not become cheaper, then it will remain a complementary technology."