Signify reduces carbon footprint with 3D printed luminaires
World leader in lighting Signify (formerly known as Philips Lighting) opened end of 2019 a plant for the 3D printing of luminiaires in Maarheeze. The company has the ambition to open 3D print factories all over the world.
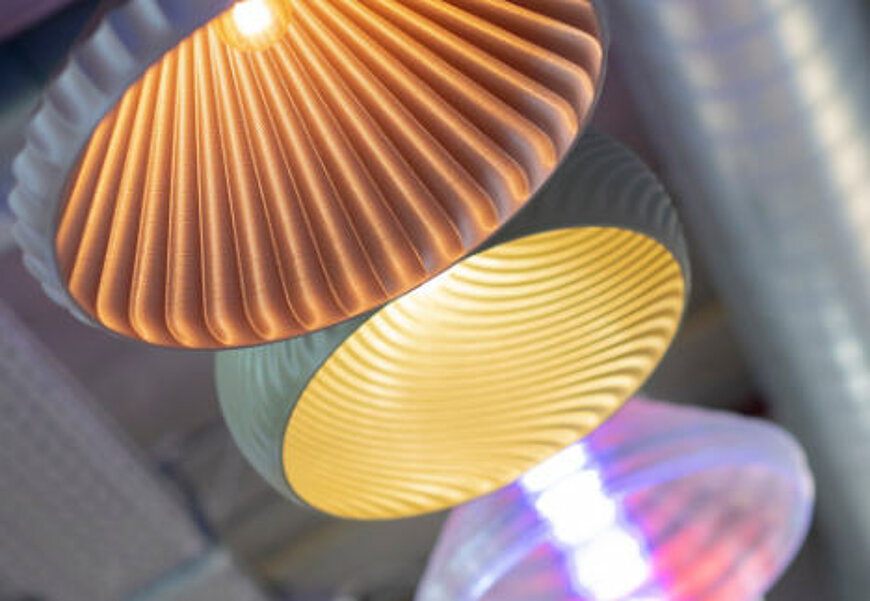
In these 3D print facilities Signify design customized luminiaires. The company has perfected this highly flexible, more sustainable form of manufacturing, using a 100% recyclable polycarbonate material, which allows luminaires to be bespoke designed or tailored to customer’s exact needs and recycled at the end of their life, supporting a circular economy.
Luminaire with 47% lower carbon footprint
A typical manufactured luminaire (excluding electronics and optics) has a 47% lower carbon footprint than a conventionally manufactured metal luminaire. Nearly every component may be reused or recycled, supporting the concept of a circular economy.
“Printing luminaires provides a more flexible, fast and more environmentally friendly way to manufacture. We can create new, or customize existing designs, that fulfill customer needs quickly without huge investments and long development cycles.”
Olivia Qiu, Chief Innovation Officer at Signify
“Customers can have their ideas brought to life in a matter of days rather than months and printing requires less energy. Our 3D printed luminaires have a lower carbon footprint than traditionally built metal luminaires. They weigh less, which enables us to reduce the carbon emissions in shipping by 35%. By keeping production close to urban areas, we reduce the footprint even further. And of course, LED lighting is more energy efficient than conventional lighting.”
Also for consumers
3D printing is nog only available for the B2B market, but also for consumers. Signify offers the world’s first online service to enable consumers to tailor decorative luminaires. Included in the range is a customizable Philips LED table lamp made from 24 recycled CDs.
In 2018, 79% of Signify’s sales comprised sustainable revenues. The company is committed to be carbon neutral in 2020 and was recently named Industry Leader in the Dow Jones Sustainability Index for the third year in a row.