How TNO transformed from broad innovation within 3D printing to specific breakthroughs in food and pharma
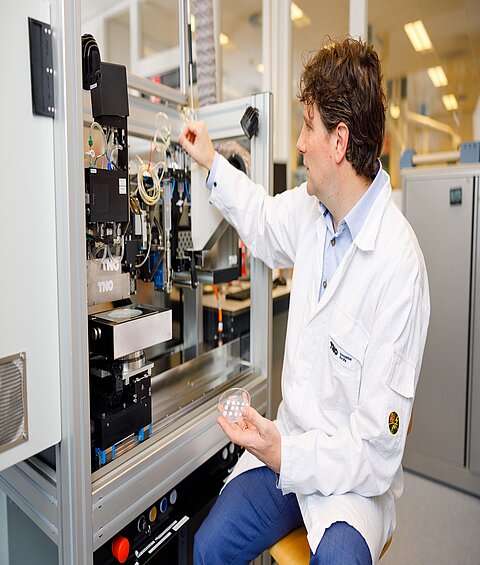
The number of applications using additive manufacturing as a production technique is growing steadily. Companies each have their own reasons for choosing 3D printing. Supply chain problems is one of them. For what other reasons would you use additive manufacturing to produce end parts? And are buyers picking up this new technology well?
AM for Production, Mikrocentrum's new knowledge event, brought the entire supply chain around additive manufacturing as a production technology into focus at the end of March 2023. This provided a stage for knowledge sharing on how to deploy 3D printing as a production technique. Applications in Dutch industry range from a dozen to several hundred pieces on an annual basis to series of 100,000 parts. The latter group is finding out that it might be smarter to order smaller batches more often. Parts on Demand has one such customer. It used to balk at the move to 3D printing because of the large quantities needed on an annual basis. "With 3D printing, it doesn't matter if you order 100 or 1,000 pieces. This makes the customer much more flexible because they can now change the design between orders," said Neil van Es, CEO of Parts on Demand. The Utrecht-based 3D printing company has customers who have converted their entire injection molding work to 3D printing. And that work no longer goes to a low-wage country but is produced in the Netherlands.
Supply chain problems since the first Covid-19 lockdowns and after the Suez Canal blockade have shaken up manufacturers, you hear in more places in the 3D printing industry. "It has become painfully obvious that all it takes is for something to go wrong in the supply chain and you have to wait months for your stuff," said Neil van Es. Marloes Homburg, sales and marketing manager at MakerPoint DigitalFabrication Solutions, recognizes this picture. She is increasingly seeing end part printing pop up as a reason in requests for 3D printers. Along with 3D printing of tooling, this is the application that customers from the mechanical engineering industry, among others, think of most often. The reason: supply chain problems. Marloes Homburg: "They are increasingly running into problems because parts cannot be delivered on time. Production times and costs are rising sharply and becoming more unpredictable. Companies then start looking for ways to produce parts in-house." In recent months, this has been playing out a lot in mechanical engineering for the food industry, she notes from the number of inquiries about food safety of materials, for example from manufacturers of conveyor belts. Some machine builders, because 3D printing technology is sufficiently developed, are bringing production back in-house. "They see that their suppliers are sending 3D printed parts. So why not do it themselves?" In doing so, companies are trying to cut costs and move faster.
Supply chain problems as a trigger for additive manufacturing have increased dramatically especially since the corona crisis. This is also noticed at QDP in Duiven, a supplier of not only 3D printing parts but also injection molded parts including the necessary mold.
"The acceptance of 3D printing as a production technique is increasing," . "Three years ago we were still printing 70% prototypes and 30% final parts, today it is exactly the other way around."
Maick Klaassen, director-owner
He also sees reasons other than supply chain problems, such as the use of lattice structures to make parts lighter yet strong. "Then the production process is already determined; then there is no alternative." Function integration is another reason he encounters. As an example, he gives a hearing protector with internal tesla valve geometry. "As an injection molder, I wouldn't burn my fingers on that. You then have to micro-inject and then ultrasonically weld or otherwise join the parts. Now we print it in one piece." This feature integration may be a good reason to 3D print. Manufacturing companies are feeling the tightness in the labor market.
At MakerPoint, Marloes Homburg sees another signal indicating an increase in AM for manufacturing purposes: the shift in material use. She sees an increase in materials like ABS, TPU and PC but also a high-performance plastic like PEEK. An AM system like the miniFactory Ultra then comes to mind. "Melting PEEK is no art, but printing a dimensionally stable, semi-crystalline part is another story. If you want a validated process, say for parts for trains, you end up with the high-end machines." Demand for these is also increasing. Companies looking to replace milling parts with 3D printed parts made of ultrapolymers, for example. "In the requests that are coming in, we really see a shift that people also want to invest in more expensive machines." This development does force potential buyers to think about the investment they are about to make. A complete SLS system from Formlabs requires an investment of roughly half a ton. "Then you do need a business case." She also notes that interest in 3D metal printing with FFF printers is increasing, even if it takes additional time because the filament manufacturer performs the sintering process.
"Some customers buy this because it gets them around the procurement of CNC milled parts. They print themselves and no longer have to create a purchase order."
Indeed, manufacturers are beginning to see that with 3D printing - whether outsourced or not - they gain flexibility. Neil van Es: "If we need to print 100,000 parts, our cost price is higher than with injection molding. But they do have the ability to adjust the design between each batch." This allows them to respond more quickly to feedback from the market, for example, if a snap connection doesn't really fit nicely after all. "Customers find the extra cost of 3D printing more than worth it because of the flexibility." Flexibility can also be in customization: with 3D printing, it is easy to customize a product to the customer, to produce oneoffs. For example, QDP prints grips for a Spanish manufacturer of racing bicycles.
There is another argument for manufacturing with 3D printing: sustainability. Less material loss. This is going to weigh more heavily in the coming years if printer manufacturers are to be believed. Neil van Es notices that customers are currently not paying enough attention to it. "They don't start talking about it themselves. It should be higher on the agenda." But he realizes that many manufacturers have to compete with companies in Asia and America. Then cost becomes a factor again. That 3D printing is material-saving is beyond dispute for him. Parts on Demand processed about 12 tons of polymer last year. "Of that, we left 500 kilograms of waste," he says.
As 3D printing becomes more widely used as a manufacturing technique, there is more interest in the technology. Industrial techniques are now emerging. Last year, QDP more than doubled capacity by installing the latest Carbon M3 printer in addition to the Carbon M2 printer. QDP also regularly 3D prints parts for sides of the critical automotive industry. Maick Klaassen attributes this step to the development of both AM technology and materials and that post-processing has been optimized.
"We can print consistently with the Carbon printers and materials, with materials that are really UV resistant and consistent post processes." And that, he says, is what final part production demands. "Customers don't want problems; materials have to be OK, even in the long run. You are now starting to see the difference between different systems and materials. Not all printing technologies are equally stable. "In addition, QDP runs into the fact that buyers often do not look at the integral cost price but at the unit price. Buyers often don't include tooling costs. "If you do include those, then the 3D printed part is competitive. "
Although he is pleased with how Parts on Demand is developing, Neil van Es notes that some customers still have cold feet after ten years. One of the shortcomings of additive manufacturing, he says, is that it is a catch-all name for a lot of techniques, some intended for form and fit prototypes, others more for end applications. "The industrial market sometimes gets snowed under among all the applications," he says. Unjustly, he thinks. "I therefore hope that AM for Production will become the trade show where the broader public comes to see how to use 3D printing for production purposes."