How TNO transformed from broad innovation within 3D printing to specific breakthroughs in food and pharma
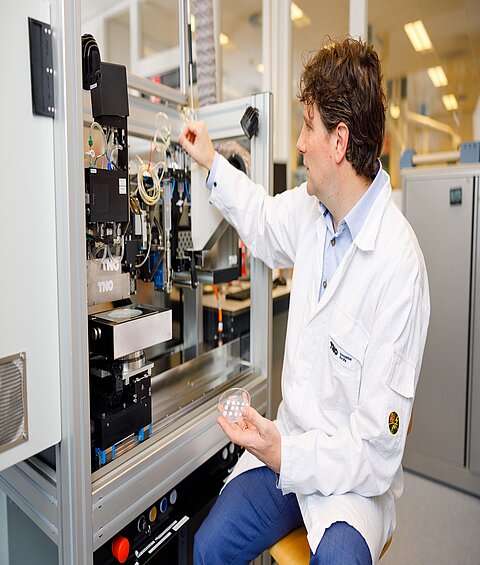
Is additive manufacturing about to become part of the standard toolbox of the manufacturing industry? Yes, according to knowledge institutes in Twente and Brainport. The sector is taking steps to make better use of 3D printing as a full-fledged manufacturing solution.
At the end of March, with the support of Brainport Development and Flam3D, Mikrocentrum organized the first edition of AM for Production, which emphasizes 3D printing as part of the toolbox of the (high-tech) manufacturing industry; as a production technique with a clear added value compared to the current production techniques. This is also the domain of Fraunhofer Innovation Platform at the University of Twente (FIP-AM@UT), one of the institutes that bridge the gap between research and industry in the Netherlands. Professor Ian Gibson, director of the Twente platform, is convinced that we are on the eve of more and broader applications of additive manufacturing. In his long career he has experienced several hypes around 3D printing: “The reality is that it takes time to arrive at additive manufacturing as a production technology. Those who are familiar with production know that this is done in small steps. But we'll get there. The AM industry has enjoyed double-digit growth since its inception in the early 1990s. The only other sector that has shown such sustainable growth is the computer industry.”
Two major changes that Ian Gibson expects in the coming years are multi-material 3D printing and the breakthrough of bioprinting. The first is especially important for the manufacturing industry: “Some call this 4D printing: multi-functionality in one part by combining different materials.” He sees materials as a key to the breakthrough of additive manufacturing. “Many more specific materials are needed for this technology. The current ones, especially polymers, are basically less suitable for 3D printing.”
How realistic is a real breakthrough of AM in the manufacturing industry? Fontys researcher Rein van der Mast has noticed that expectations for 3D printing have gradually been adjusted downwards in recent decades. At the end of the last century, insiders foresaw that 3D printing would push many manufacturing techniques out of the market. It still hasn't come that far. However, it has now been shown more than once that 3D printing can lead to objects that other manufacturing techniques are not capable of. And vice versa, because it is completely complementary to all conventional, more traditional production techniques.
“What the 'traditional' manufacturing solutions cannot do, can be done with 3D printing, and vice versa. This has greatly increased the diversity of the solutions currently available,” says Rein van der Mast, who started his PhD research at KU Leuven at the end of 2022. In his research he involves IAMM, the partnership between the universities of applied sciences Fontys, Saxion and Windesheim, which was created on his initiative and in which Flam3D, K3D, Materialise, ASML and FIP-AM@UT also participate, for example. Rein van der Mast had his first prints made in 1996. “It is high time that the market started to pull it off, instead of a few overenthusiastic techies continuing to develop. To really bring about a change, we need to show where 3D printing can be used to deal with all kinds of current problems: the speed at which objects are created, the stocks that are held, the risks involved in producing them. are at issue, the extent to which there is variation in series (such as with personalization), and the topicality of the business models used.” He points out that the entire chain has to change to make its implementation a success: “Buyer, seller, designer, manager, you name it, everyone has to participate!”
“Buyer, seller, designer, manager, you name it, everyone has to participate!”
Rein van der Mast
However, additive manufacturing is not yet a mainstream production technology today. The sector still needs to take a few steps to achieve this, says Professor Ian Gibson. For example, he believes that costs must be reduced in order to be able to scale up volume applications. “The providers of the technology are now focusing on that. They are mainly focusing on lower costs by scaling up AM production.” Material costs will also have to fall: “We need materials and cost prices per part that allow us to compete with mass production.” Changes in this direction have been initiated, not only in metalworking, but also in other applications of 3D printing, such as healthcare, construction, shoe sole production, et cetera. We can expect a lot in this area in the coming years, he says. Step by step, additive manufacturing then becomes a production technique that belongs in the industry. The industries that will benefit the most from this are the sectors that are not yet doing anything with additive manufacturing at all.
“Companies that are not yet using AM will benefit the most if the machines become cheaper and faster.”
Professor Ian Gibson
Rein van der Mast sees more in a 'chain-long' approach, where AM is 'just' one of the available manufacturing solutions: “It's about applying AM where its added value really exists along the entire chain. The 'profit' must also be achieved in combination with a smaller number of parts, a limited number of assembly steps, a lower weight, things like that.” He sees new techniques for other applications, such as car parts: slightly less accurate and strong, but also less expensive. He also sees an untapped market: small prints with high detail that require little or no post-processing. “It seems that the industry is not interested in small prints. Remarkable, because per print series of dozens of pieces can be produced in one go, in a short time, even with complex shapes with diverse function integrations.” That is where he focuses his PhD research: small parts with a higher 'resolution' with standard machines based on powder bed and laser.” Some high-tech companies are showing interest in this in order to integrate channels, spring blades, arms, deliberately porous areas, etc.