Hoe TNO van brede innovatie binnen 3D printing naar specifieke doorbraken in food en farma transformeerde
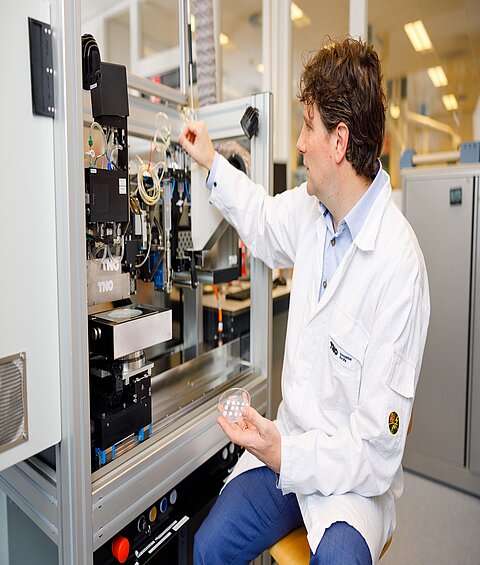
Het hart van de meeste elektrische apparaten wordt gevormd door printplaten (PCB’s). Deze dikke en stevige – vaak groene – platen herbergen schakelingen en kunnen worden beschouwd als het brein van een afstandsbediening, een blender of een tv-scherm. In plaats van starre printplaten hebben steeds meer apparaten dunnere en mogelijk flexibele oplossingen nodig. In Eindhoven is onlangs een nieuwe fabriek voor het buigen van elektronica geopend.
TracXon, een spin-off van het door imec en TNO gesteunde Holst Centre, opende daar zijn gieterij voor de productie van hybride geprinte elektronica. Deze producten zijn het eindresultaat van een proces waarbij geleidende inkten worden gebruikt om circuits te printen op materialen zoals plastic en stof. In het geval van de spin-off van het Holst Centre gebeurt het printen op dunne plastic folies.
Het gebruik van dit substraat voor het inbouwen van elektronische componenten opent veel mogelijkheden. Verlichting, apparaten voor gezondheidsbewaking en batterijbeheersystemen voor elektrische voertuigen, dunne en buigbare schakelingen kunnen ze allemaal bedienen. Bovendien maakt deze technologie efficiënter gebruik van materialen: er wordt minder van gebruikt en er wordt gekozen voor lijmen en inkten die aan het eind van hun levensduur kunnen worden gerecycled.
Al deze voordelen komen zonder afbreuk te doen aan de nauwkeurigheid van het product. “Met de printers waarover we beschikken, kunnen we een maximaal detail bereiken. Elk puntje telt hier, anders werkt het circuit niet. Dankzij de combinatie van materialen, processen en mensen kunnen we kwaliteit op pixelgrootte bereiken”, zegt Ashok Sridhar, CEO van TracXon.
Een meer dan 20 meter lange clean room herbergt de roll-to-roll productielijn. Alle benodigde apparatuur staat dicht op elkaar. “Hier kunnen we continu honderden meters circuit printen”, legt één van TracXon’s werknemers uit temidden van de herrie van de machines. Daar rollen foliespoelen langzaam af, terwijl ze door de lijn gaan. Eerst komt het drukken, waarbij de robotkop de folie scant en vervolgens schakelingen injecteert. Enkele seconden later bereikt de folie het uithardingsstation, waar – precies zoals in een hamdrogerij – lucht wordt geblazen bij een gecontroleerde temperatuur. Dit voorkomt dat printplaten gaan kleven terwijl de vers gedrukte printplaten drogen.
Na het uitharden zijn de folies klaar om te worden gelaserd – door TracXon zelf of door hun klanten, afhankelijk van hun wensen.
In het assemblagelab worden elektrische componenten op de geprinte folie geplaatst. De folies gaan onder een robot door die ze nauwkeurig scant en begrijpt waar elk onderdeel moet worden geplaatst. Na het spuiten van lijm gebruikt de printer een vacuüm om de componenten te pakken en te plaatsen. De platen gaan dan door een oven om te drogen. Beide printlijnen garanderen nauwkeurigheid, aangezien het bedrijf het printen van lasercircuits op het oog heeft als volgende toevoeging aan zijn mogelijkheden.
Enkele van de klanten die voor de spin-off van het Holst Centre kozen, waren ook aanwezig op het openingsevenement. Een van hen is het Duitse MinkTec, dat een flexibele sensorstrip ontwikkelt die vormen kan meten en weergeven op apparaten. Een van de use cases is het gebruik van de strip voor het detecteren van iemands rughouding. De slimme strip is voorzien van hybride geprinte elektronica van TracXon die het volgen van de vorm mogelijk maakt.
Een ander domein waarop het Eindhovense bedrijf zich richt is dat van batterij managementsystemen. Op dunne stroken folie hebben zij schakelingen geïntegreerd om de batterijstatus bij te houden. Omdat de strips flexibel en adaptief zijn, zouden ze in elke batterijcel kunnen worden geïntegreerd, in plaats van één enkele sensor voor het hele pakket. Dit zou resulteren in een betere controle van de batterijstatus, waarbij alleen defecte cellen worden opgespoord en dus vervangen.
Gezien het grote aantal oplossingen dat hybride gedrukte elektronica biedt, streeft TracXon ernaar deze productietechnologie om te vormen van een niche naar een mainstream. Vandaag de dag is PCB-technologie nog steeds de go-to oplossing voor de meeste bedrijven.
“Niemand anders kan echter flexibele elektronica printen zoals TracXon dat doet”, stelt Ton van Mol, directeur van TNO bij Holst Centre. “Het opzetten van deze productielijn bewijst dat high-end producten op deze manier gemaakt kunnen worden. De combinatie van printen en assembleren in één fabriek is bijna uniek in de wereld”, voegt hij eraan toe.
Anderzijds gelooft Sridhar zelf dat een sterk partnerschap met TNO de sleutel is tot het toekomstige succes van het bedrijf. “Door hun steun en samenwerking – die meer dan 20 jaar ervaring hebben met technologieën – kunnen we innovatie van lab naar fabriek brengen. Bovendien is het ecosysteem van de regio ook een groot voordeel voor ons, aangezien veel actoren deze technologie onderzoeken en overwegen toe te passen”, benadrukt de CEO van TracXon.
"De combinatie van printen en assembleren in één fabriek is bijna uniek in de wereld"
Ton van Mol, directeur van TNO bij Holst Centre
Bij het zien van de ontwikkelingen in de hybride printtechnologie kwam de beslissing om een stap vooruit te zetten vanzelf. “Wij geloven dat dit groot gaat worden. Het is niet onze bedoeling om een kleinschalige productie op te zetten, maar om in de komende vijf jaar het grootste bedrijf in deze markt te worden. In die tijdspanne willen we de mentaliteit van de industrie veranderen. Veel toepassingen worden mogelijk met deze technologie, en wij willen de eerste zijn”, stelt Sridhar.
Op korte termijn zal TracXon zich richten op twee toepassingsgebieden: gezondheidszorg en automotive. Naarmate het bedrijf zijn nieuwe productieomgeving inpast, zal het zich eerst specialiseren in deze twee sectoren, om zo de productie te optimaliseren en het stijgende aantal klanten op te vangen.
Op de hoofdfoto, de rol-naar-rol productielijn van © TracXon