Senergetics can reduce millions of pounds of CO₂ emissions with integrated photonics
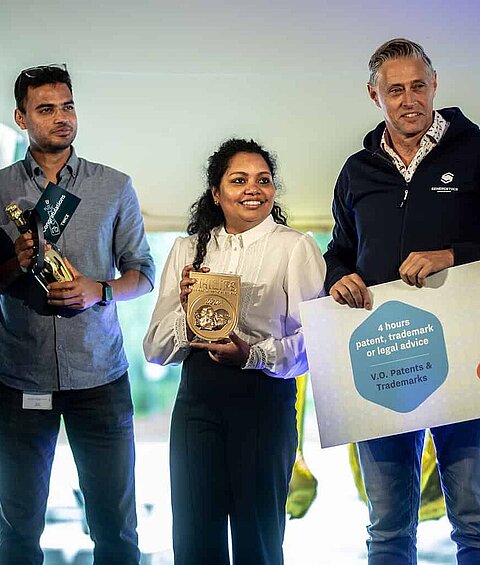
In cleanliness aspects such as process control, knowledge and skills and cooperation throughout the chain are important. If you want to play at the highest level in terms of technical cleanliness, you will have to invest in knowledge and skills and spread them throughout the chain. Cleanliness has become a competence, according to two leaders in the manufacturing industry, Frencken Mechatronics and NTS Norma.
In mid-April, Mikrocentrum has organized the Clean Event 2023. What started as a niche event a few years ago has grown into the annual meeting place for everyone who is professionally involved with high-tech cleanliness. Rob Leussink and Frank van Otten, Cleanliness Experts at NTS Norma and Frencken Mechatronics respectively, are not surprised by the growth of this community. It is not only ASML that is constantly raising the bar in this area. Other customers are also asking for cleaner parts. “They set the bar high with their own specifications. For one, the emphasis is on particle cleanliness; in others, more on molecular contamination,” notes Frank van Otten.
The different standards used by OEMs sometimes make it difficult for their suppliers. But, as both say: they also learn from the experiences they gain with the various customers. Each time, cooperation in the chain proves to be crucial to achieve the desired end result. Process descriptions and agreements about this are very important. Frank van Otten: “Grade 1 (ASML's new standard) has such an impact that, if you don't have the entire chain under control, you end up with irreversible contamination at the end of the process. Think of drying spots that you can't get rid of.” Prevention is better than cure. For Rob Leussink, collaboration falls under the heading of process management. He considers the process not only as the processing steps that NTS Norma carries out in Hengelo itself; the steps taken by chain partners are also part of this. Rejection due to, for example, stains that arise somewhere in the process, disrupt the entire process.
"Every link counts"
Rob Leussink, Cleamliness Expert at NTS Norma
Exchanging ideas and experiences is becoming increasingly important. The Clean Event 2023 was the place for that. Frank van Otten and Rob Leussink were both keynote speakers this year. They invest a lot of time in communication, both with their own production departments and with external suppliers. Frank van Otten: "It starts with awareness, becoming aware of why cleanliness is important and why it is necessary for an operator to wear gloves, for example." Recording knowledge, providing training in this area and ensuring awareness are very important. Both internally as with suppliers, support is required for the implementation of high cleanliness requirements.
“It is very knowledge-intensive and challenging”
Frank van Otten, Cleaniness Expert at Frencken Mechatronics
In recent years, the high-tech manufacturing industry has invested heavily in the theme of cleaning. Where Grade 2 cleaning was still the domain of specialists a few years ago, you see more and more Tier 2 and 3 suppliers investing in this. This is partly because the technology has become more accessible in every respect. It's one of the reasons why cleanliness costs are on the rise. A relatively new fact that drives up costs is how you demonstrate cleanliness (verification). Rob Leussink and Frank van Otten wonder whether the costs of demonstrating the cleanliness level will not get out of hand in the coming years. Rob Leussink therefore advocates a different approach: “If the entire process is under control and stable, we no longer need to measure everything. Then the verification is part of the process and we can suffice with taking samples.”
The cleaning line, at the very end of the process, is a place where Statistical Process Control (SPC) is already properly applied, together with an Out of Control Action Plan (OCAP). Frank van Otten thinks these are good tools that you can also use in other places. By doing this in every critical step of the process, you make departments self-reliant and you ensure peace in the organization. “If there is a problem, departments can solve it themselves in 80 percent of the cases. Then we remove the mistakes because the people are educated and trained.” However, SPC remains a tool; cleanliness ultimately starts with the human factor in the entire chain from design to end product. “The higher the cleanliness requirements, the more important the people and discipline factor become.”