Senergetics can reduce millions of pounds of COâ‚‚ emissions with integrated photonics
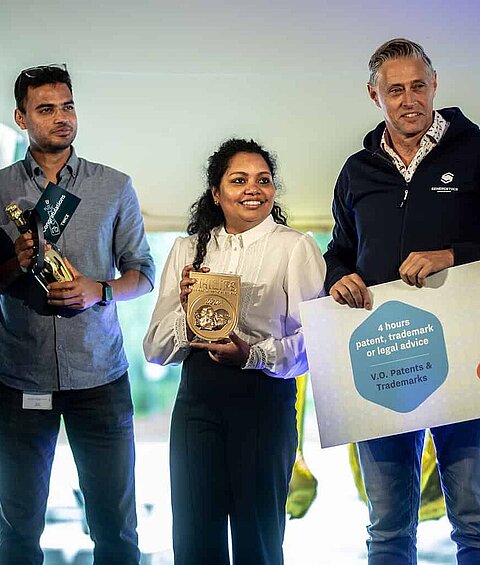
Cleanliness is an issue for many OEMs in the manufacturing industry. However, the requirements are not the same everywhere. Nor can they be, states Rients de Groot of Thermo Fisher Scientific. The high-tech systems are too different for that.
The fact that researchers worldwide soon knew what the Covid-19 virus looks like is partly thanks to Thermo Fisher Scientific in Eindhoven. The electron microscope makes cell structures and, for example, proteins visible at the atomic level. The TEM (Transmission Electron Microscope) and SEM (Scanning Electron Microscope) bring samples into focus at sub-nanometer level. With the Eindhoven company's Krios G3i cryo-electron microscope, scientists are using frozen tissue from patients to conduct research into diseases such as cancer, Alzheimer's and others worldwide. The Eindhoven electron microscope is over 70 years old. The current generation resembles the first models in almost nothing. However, the beam of electrons radiating and projected through the sample is still the heart of the system. And that electron beam creates very specific requirements for part production, especially when it comes to cleanliness.
''We can be quite proud of our supply chain in Dommel Valley''
Ton van den Broek
Molecular contamination listens much more critically to Thermo Fisher Scientific than particle contamination. The energy of the standard 300,000V electron beam is so powerful that particles are less disruptive. "But when an electron hits hydrocarbon, it decomposes into carbon and hydrogen. The beam takes the carbon with it, which precipitates on the specimen," explains Ton van den Broek, Technical Supply Chain Engineer. Carbon buildup occurs on the surface of the sample the researcher wants to look at. This reduces the transmission for the electron beam and makes the projected image worse. Incidentally, preventing particle contamination does become more important in recent years because the new generation of electron microscopes operate at low voltages. In the cryogenic systems, widely used in tumour research, Thermo Fisher uses a 30 kV electron beam. Electrostatic lenses are also more sensitive to particle contamination.
Ton van den Broek was present all day during Mikrocentrum's Clean Event 2023 (18 April 2023) for one-to-one discussions with suppliers who had questions about Thermo Fisher's making, cleaning and cleanliness levels. Rients de Groot, Senior System Design Engineer, presented these in a lecture at the event. Both feel it is important to increase understanding and knowledge about these specific cleanliness requirements in the supply chain. "We can be quite proud of our supply chain in Dommel Valley. Suppliers have capabilities regarding cleanliness and production that you find much less elsewhere in the world," says Ton van den Broek.
For decades, Thermo Fisher has relied heavily on two suppliers in the region. Specifications with regard to manufacturing were well developed, including the way each material was cleaned. However, the demand for the microscopes is increasing to such an extent that the supply chain has now expanded and needs to be widened and deepened even further. Therefore, dissemination of the specific cleanliness knowledge is needed, because the electron beam ensures that Thermo Fisher Scientific has very different requirements than, for example, the semiconductor industry. "More stringent," both say. That has everything to do with the ultra-high vacuum where the source for the beam sits: 10-12 mbar or better. By comparison, high vacuum at ASML means 10-5 mbar after which a controlled, reducing atmosphere is created with a hydrogen gas.
''With us, you are really talking about ultra-high vacuum and that is a challenge in both machining and cleaning processes''
Ton van den Broek
"With us, you really talk about ultra-high vacuum and that is a challenge in both the machining and cleaning processes," notes Ton van den Broek. "For example, we have more problems with contamination from the bulk of the material. In terms of materials, austenitic stainless steel, aluminium-copper, other copper-containing materials, lead and aluminium are widely used. Aluminium is not used in the load-bearing main structure because it offers low shielding against X-rays.
For ultra-high vacuum, rubber o-rings are out of the question; they are too water-permeable. Metal seals are necessary for this. The surface roughness of parts listens closely. Sometimes a high-gloss part turns out to be non-functional. Rients de Groot: "We see every surface as a ploughed field; pollution is stored under the material." The processing method influences this. Grinding, for example, gives a lot of plastic deformation and also creates stresses in the material, which in turn is bad for the magnetic properties of the material. Polishing with a loose grain and hydrocarbon carrier, on the other hand, produces contamination. Something similar plays out with deburring with regard to finishing: scraping or with a cutter? Or blasting with grit? "Blasting creates an embedded alumina and blasting grains, which can come loose," warns Ton van den Broek.
''We see every surface as a ploughed field: pollution is stored under the material"
Ton van den Broek
All mono parts from suppliers go through the cleaning line again at Thermo Fisher, aqueous alkaline dipping or via dipping and vapour degreasing with a solvent. At least 17 different cleaning recipes are available for this, developed by the company itself. Each step is precisely defined in terms of cleaning agent, temperature and time. The result of years of experience. By the way, 100% clean is not possible, but you should not exceed certain values because a so-called 'stinker', a contaminated part, becomes a source of contamination when you start to gas out the part in vacuum. After cleaning, the parts are fired out in an oven at a high temperature to get the water out. The nitrogen molecules on firing take the place of water, called diffusion cleaning. "Cleaning with modified alcohol at 110 degrees is not good enough for us because you don't remove all the oxides with that. We need to burn out." Every morning at 10am, the oven opens and cleanroom assembly staff take out the parts for the day. These are stored in a cabinet with nitrogen atmosphere. Even the plasticiser in a plastic bag to store the part cleanly can cause contamination.
The easy solution seems to be for suppliers to copy the cleaning line and 'recipes'. Wrong, both respond. Cleanliness starts at the very beginning. Even if Thermo Fisher cleans every mono part that comes in, if the supplier has not done certain steps properly, Thermo Fisher cannot make the part functional with the in-house cleaning. For example, the cooling lubricant during machining that the supplier uses is important; whether or not the part is intermediate cleaned immediately after machining. Ton van den Broek: "Companies often work with pallet loaders; unmanned. But if you produce unmanned, you never reach ASML's Grade 2 and 1 requirements or our highest cleanliness levels." For that, the robot then has to do intermediate cleaning. Suppliers also have to adjust their production strategy: the parts that have to meet the highest cleanliness levels are not processed until, say, Sunday night so that they are in the cell for as short a time as possible. Gripping parts with bare hands is disastrous because of hand acids.
''If you produce unmanned, you will never achieve ASML's Grade 2 and 1 requirements, or our highest cleanliness levels"
Ton van den Broek
Thermo Fisher Scientific wants to and is going to grow in Eindhoven. For this, the supply chain has to grow with it. This requires focus from every cog in the chain, believes Ton van den Broek. "Tier 1 suppliers have to share our specs with the rest of the chain. That's where things often go wrong already. Buyers do not sufficiently realise that cleanliness is so important." Rients de Groot sees another bottleneck: manufacturing companies in the Netherlands are investing massively in cleaning capacity, but do they have sufficient knowledge about what and how to clean and how to verify the specification? He gives the example of an RGA measurement: it yields different results if you fill the chamber with all kinds of products or with just one part. And are the RGA heads calibrated before the measurement? A third example: when Thermo Fisher puts parts into the metal baskets of the cleaning line, they are hung on plastic holders. "Otherwise, a potential difference is created in the cleaning bath and an oxide layer can form," he says. Or scratches, fatal to the operation of the electron microscope.
Thermo Fisher buys mono parts and assembles the subsystems itself. There is a good reason for this. "If we were to buy module-by-module, we need to be able to functionally check the module. This is difficult because incorrect steps in the manufacturing process only come to light once the microscope is assembled. "Then you have to make the specs very detailed and precise," says Rients de Groot, who fears that even the best cleaning at a supplier is not good enough for Thermo Fisher. Even the permitted bandwidth for alloys in and treatment of certain materials is too wide for some parts, Ton van den Broek outlines a recent experience. "Due to material scarcity, a supplier buys the same material elsewhere, but the variation in alloys already affects functionality." Thermo Fisher's customers are all about the very smallest details they want to see, the atoms. In the production of the electron microscopes, the same applies: the devil is in the details.