Industrial 3D printing: from prototyping to serious production technology
In Brainport Eindhoven the entire network of Additive Manufacturing is working together to accelerate innovation in the industry.
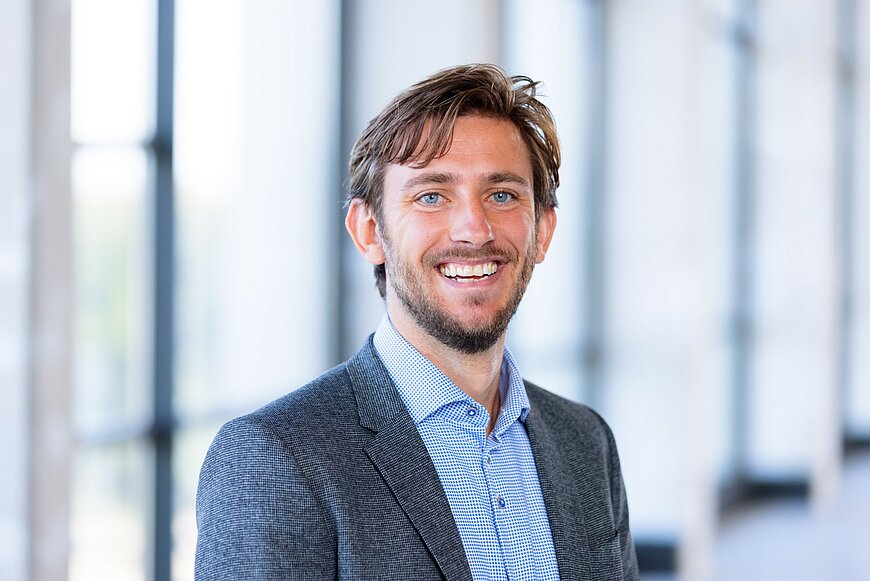
3D printing is developing rapidly as a digital production technology. Companies are deploying it to speed up product development, for example, or to create complex shapes. "It is a production technology that has passed the stage of prototyping," says Ruben Fokkema, Ecosystem & Business Developer at Brainport Development. "3D printing has become an accepted manufacturing technology. 3D-printed parts are found in finished products; companies are generating business with them."
Ask Fokkema for examples and he immediately lists a whole list of applications. Such as the stock management of the Dutch Railways, NS. "A train can last thirty to forty years. Spare parts are kept in stock for years. That requires extra storage. The Tilburg start-up Castlab now scans those parts and then examines what can be 3D-printed. That way, the parts no longer need to be kept in stock."
We are also seeing 3D printing more and more in complex and safety components, Fokkema continues. "Take for example Sauber’s Formula 1 car. There are 130 3D-printed parts in there. Among other things, pieces that are important for the safety of the driver himself." For this, the Formula 1 team works together with Eindhoven-based Additive Industries, which specializes in printing with metal.
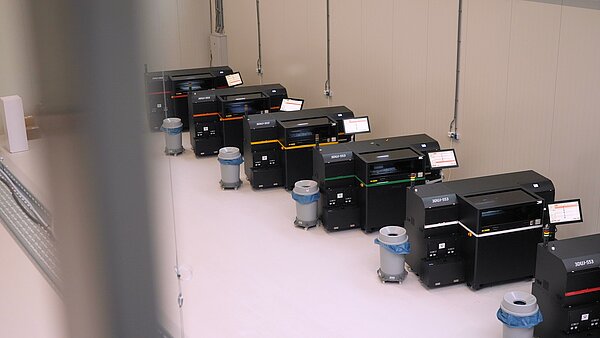
These complex forms can be very large, such as a bridge printed with concrete. Or they can be very finely woven. Fokkema: "Look for example at the radiation grids that Dunlee, a division of Philips, makes. A branch in Best prints beautiful honeycomb structures from extremely fine material, tungsten. Without 3D printing, they wouldn't be able to do that."
The Brainport region can be called a frontrunner in 3D printing, says Fokkema. "In this relatively small area, of about thirty kilometers in circumference around Eindhoven, there are 70 suppliers in Additive Manufacturing (AM), as 3D printing is also called. That is a high concentration. There is a lot of knowledge here about materials, mechatronics, and design. These three competencies are important to achieve an application. You don't see that unique concentration of competencies in many regions."
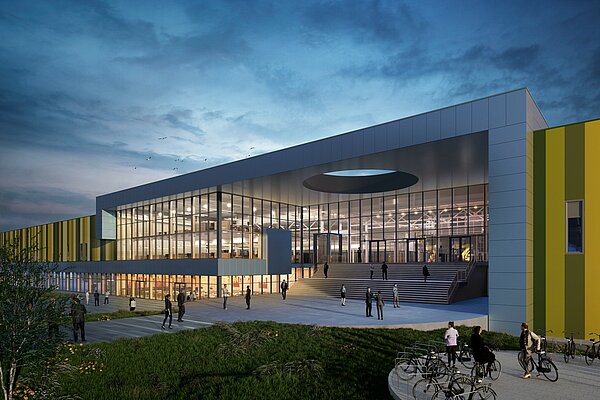
In addition, there is another aspect at play, says Fokkema. "You can have all different suppliers, but this production technology means a radical change in the entire chain." It is disruptive production technology, according to Fokkema. "The possible applications, their production, and the supply chain require serious development to achieve change," he says.
"You have to work together to achieve the change in the total chain. That collaboration can be seen within Brainport Industries Campus (BIC). Some 25 AM suppliers are already active there. In this way, a lot of knowledge comes together and you can find the right partners for a particular application, development, or production line."
Despite the growth, there is also still a lot of ignorance among entrepreneurs, Fokkema knows. "Ignorance about all that is technically and commercially possible, but also where you can go if you have an idea for an application. For this purpose, Brainport Development organizes master classes on specific applications, such as in the field of public safety and security or 3D printing for electric cars and applications in the medical sector on June 22.
In addition, 3D printing means a total change in the development and production process and in the supply chain of a company. "This disruptive technology is not ready-made," says Fokkema. "It requires a different development with each customer. The threshold to invest in that development seems and sometimes still is too high."
"Within Brainport Development we want to lower it. By sharing knowledge, such as in the master classes, but also by referring to relevant suppliers and facilities. Parties that are well suited to the specific need and want to bring something extra to make such a development a reality."
Fokkema wants to expand and strengthen the network around AM. "We provide strategic collaborations. So that, for example, large long-term plans can be realized. By bringing the stakeholders together you can find suppliers who are prepared to invest in a new application. You can form a plan together, make a business case for it and recruit public and private investments."
The 3D Delta Week from June 20 to 24 is organized to bring the whole network together. Companies can experience how to integrate additive manufacturing into their production processes. Spread over five days, master classes, conferences, open days, and networking opportunities will take place.