Eindhoven University of Technology prepared the longest 3D printed bicycle bridge in the world
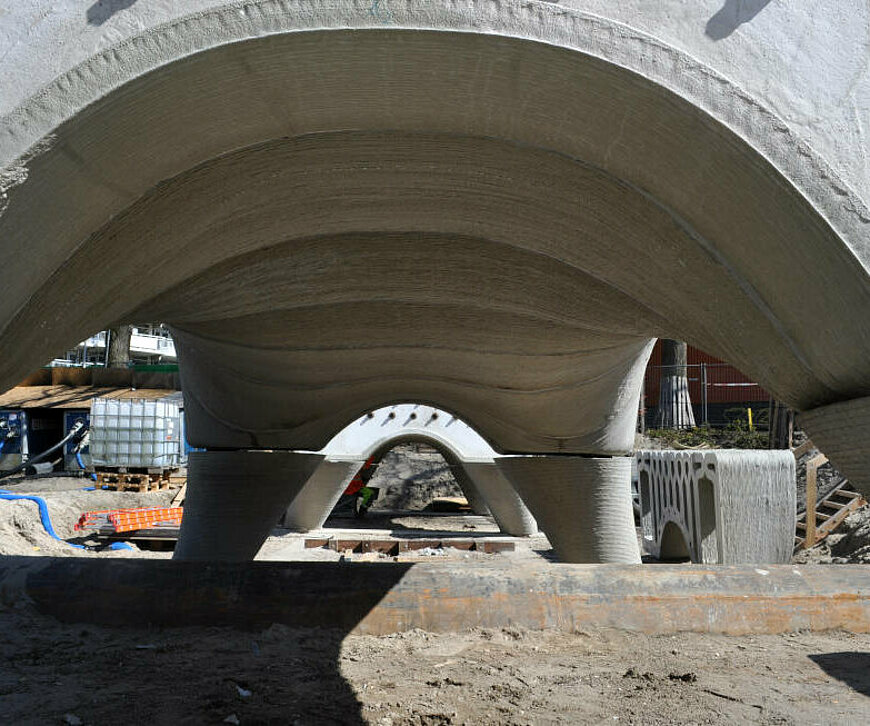
The Nijmegen bridge project was not a textbook example of fast and flexible completion of a construction project. Yet that is precisely what is expected from 3D printing technology in the future.
“It is wonderful to see it is finally happening. After a lot of talking, thinking, pow wows and other things, finally, the 29.5 meter 3D printed bridge is being placed. Wow, what a joy!” Those were the words of a happy Michiel van der Kley when a few weeks ago construction began on one of his babies, the longest 3D-printed bicycle bridge in the world in the Zwanenveld district of the Dutch city of Nijmegen.
Van der Kley was no doubt very relieved as well, because the bridge should have been built much sooner. But for some inexplicable reason the project was put on hold for a long time. Evidently this was due to the lengthy wait for the final permits. But now the time has finally come! And soon the first cyclists will be able to cross the bridge in the De Geologenstrook park.
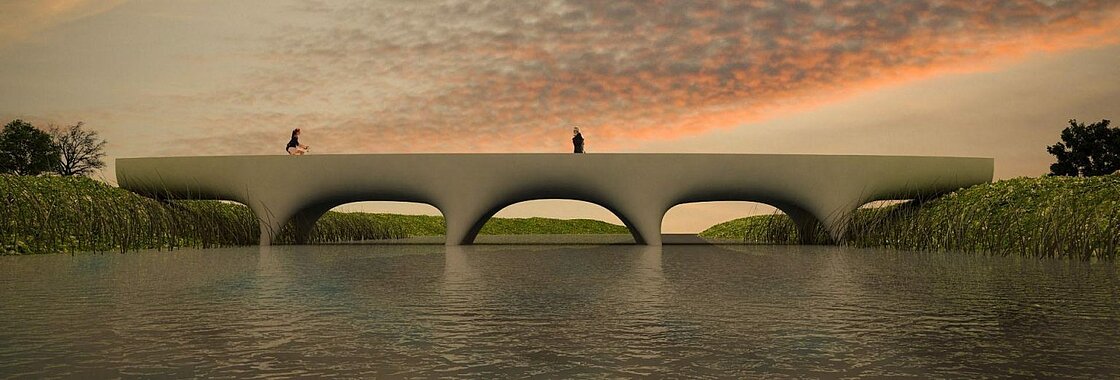
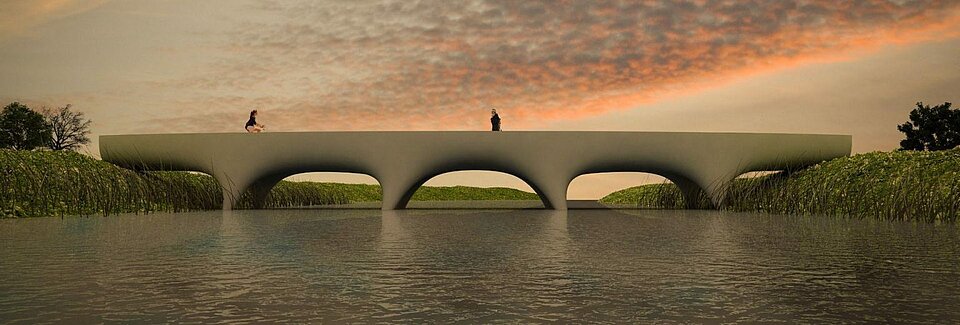
Green Capital of Europe
3D printed bridges are not unique in themselves. There are several, but this is the largest of its kind. The idea originated a few years ago in Van der Kley’s studio. That was when the leaders of the Dutch Ministry of Infrastructure and the Environment paid a visit. They were there to see how far the technology has advanced in the 3D printing of concrete.
The Director General at the time, Jan Hendrik Dronkers, was so enthusiastic that he challenged Van der Kley that same day to design a 3D-printed bicycle tunnel. When a location was sought, the choice fell on Nijmegen. This was the European Green Capitol in 2018 and as such, wanted to have an enduring reminder of that.
During the discussions about the exact location, it became clear that it should not be a tunnel, but a bridge instead. Together with the Directorate-General for Public Works and Water Management (Rijkswaterschap) and the Eindhoven University of Technology (TU/e), Van der Kley went to work. In 2019 the printing of the first concrete structural parts began in Eindhoven in partnership with BAM Infra and Weber-Beamix. Witteveen+Bos was responsible for the structural engineering of the bridge and Summum Engineering for “parametric modelling” (see below).
The Dutch town of Gemert
This partnership already had a lot of experience. In fact, they had the worldwide premiere in 2017 for a 3D-printed bridge in the southern Dutch town of Gemert. A year and a half later, they were also the first in Europe with an industrial manufacturing site which used a 3D printer to make concrete parts for construction. The Nijmegen bridge was one of the first major projects to be carried out there.
The bridge in Nijmegen will probably not hold its new record for very long. Developments are moving too fast for that. Plus the advantages of 3D-printed structures are too many to ignore. Van der Kley says the following about this: “We think that this way of manufacturing will ensure that contractors, structural engineers and designers will be given a different role. Designs will become ‘living’ designs, which adapt to the circumstances. Structural engineers will be involved much more during the preliminary stages, and contractors might end up working with fewer people and with other people.”
Weber-Beamix states on its website that this method of working has made individual series production possible while still allowing for a tremendous amount of creative freedom.
Material savings of 30% to 60%
“The magic term is smarter building with parametric design. This is a process in which models or designs are generated automatically based on parameters, such as dimensions, material thickness or geometry. In other words, faster and more sustainable design. In this case, it is the printing robot that can vary endlessly according to a variety of parameters. For example, you can give all the columns of a bridge or viaduct a different shape. Moreover, less concrete is required for the same result. The printer only pours in concrete where it is needed for the structural strength of the bridge. We achieve savings of between 30% and 40% that way. In fact, when it comes to the bicycle bridges that we’re going to print for North Holland, we are even estimating material savings of 50% to 60%. Also, no formwork is needed anymore, so there is no waste.”
Faster, safer, cheaper
To be sure, the 3D printed construction elements are not just about parts for bridges. They also involve, for example, components for residential buildings, offices and art objects. One of the major advantages is that considerably less time needs to be spent on the construction site. In fact, the parts only need to be joined together, which also makes the whole process safer for construction workers.