TU Eindhoven werkte aan de voorbereidingen van de langste 3D-geprinte fietsbrug ter wereld
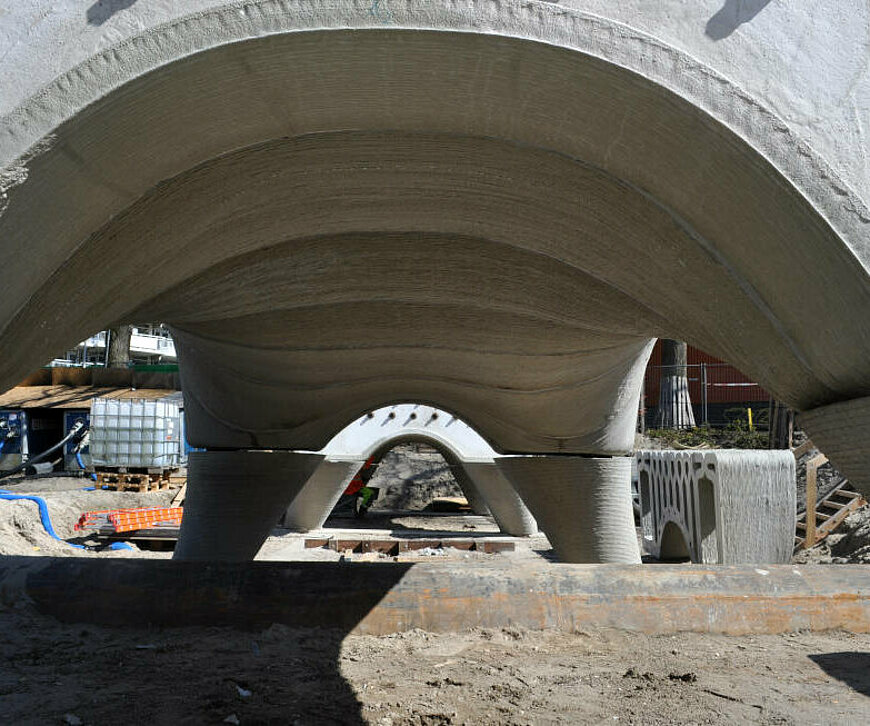
Het Nijmeegse brugproject was geen schoolvoorbeeld van snelle en flexibele realisatie van een bouwproject. Toch is dat wel wat er in de toekomst van de 3D-druktechniek wordt verwacht.
“Het is geweldig om het te zien gebeuren. Na veel praten, denken en pow-wows wordt de 29,5 meter lange brug eindelijk geplaatst. Wow, wat een genot”. Dat waren de woorden van een gelukkige Michiel van der Kley toen een paar weken geleden de bouw begon van een van zijn kindjes, de langste 3D-geprinte fietsbrug ter wereld in de wijk Zwanenveld in Nijmegen.
Opluchting was er ongetwijfeld ook bij Van der Kley, want de brug had al veel eerder moeten worden gebouwd, maar om onverklaarbare reden lag het project heel lang stil, blijkbaar wachtend op de laatste vergunningen. Maar nu is het dan zover, en kunnen binnenkort de eerste fietsers over de brug in het parkje De Geologenstrook.
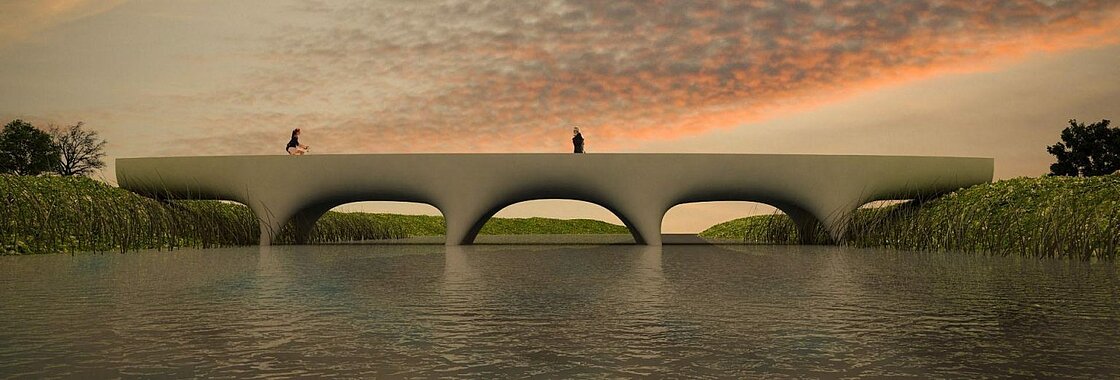
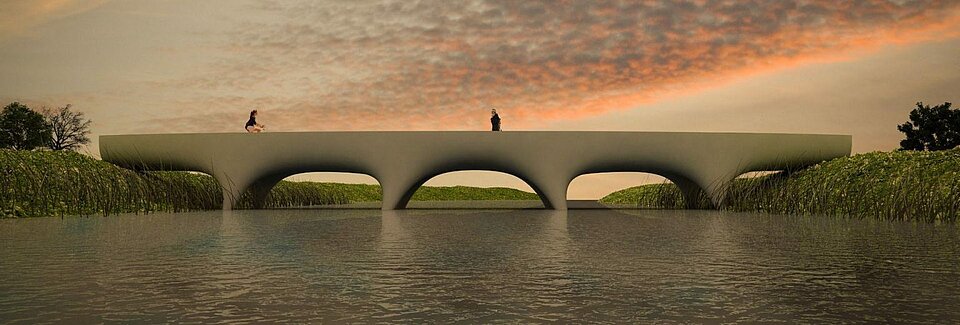
Groene hoofdstad
3D-geprinte bruggen zijn op zich niet uniek. Er zijn er meerdere, maar dit is wel de grootste in zijn soort. Het idee ontstond een paar jaar geleden in het atelier van Van der Kley, waar de top van het ministerie van infrastructuur en milieu op bezoek was. Ze waren daar om te zien hoe ver de techniek gevorderd is van het 3D-printen van beton.
De toenmalige directeur-generaal, Jan Hendrik Dronkers, was zo enthousiast dat hij diezelfde dag Van der Kley nog uitdaagde om een 3D-geprinte fietstunnel te ontwerpen. Bij het zoeken naar een locatie viel de keuze op Nijmegen, dat in 2018 Green Capital of Europe was en zocht naar een blijvende herinnering.
Verder pratend over de precieze locatie werd duidelijk dat het geen tunnel, maar een brug moest worden.
Samen met Rijkswaterstaat en de Technische Universiteit Eindhoven ging Van der Kley aan de slag en in 2019 werd in Eindhoven begonnen met het drukken van de eerste betonnen bouwdelen door Weber-Beamix samen met BAM Infra. Bureau Witteveen+Bos was als technisch ingenieur verantwoordelijk voor de constructie en Summum Engineering voor het “parametrisch modelleren” (zie hieronder).
Gemert
Deze combinatie had al veel ervaring. Sterker, zij hadden in 2017 de wereldwijd primeur voor een 3D-geprinte brug in het Brabantse Gemert. Anderhalf jaar later waren zij ook de eerste in Europa met een industriële productielocatie voor het 3D printen van betonnen bouwelementen. En de Nijmeegse brug was een van de eerste grote projecten die daar werd uitgevoerd.
Heel lang zal de Nijmeegse brug zijn record waarschijnlijk niet vasthouden. Daarvoor gaan de ontwikkelingen te snel en zijn de voordelen van 3D-geprinte bouwwerken te groot. Van der Kley zegt hierover het volgende: “Wij denken dat deze manier van produceren ervoor gaat zorgen dat aannemers, constructeurs en ontwerpers een andere rol krijgen. Ontwerpen worden ‘levende’ ontwerpen, die zich aanpassen aan de omstandigheden; constructeurs worden veel meer in het voortraject betrokken en aannemers zouden wel eens met minder mensen kunnen werken en ook andere mensen.”
Weber-Beamix stelt op zijn website dat deze manier van werken individuele seriematige productie mogelijk heeft gemaakt met ondertussen toch een enorme vrijheid bij het ontwerpen.
Materiaalbesparingen van 30% tot 60%
“Het toverwoord is slimmer bouwen met parametrisch ontwerpen. Dat is een proces waarbij modellen of ontwerpen automatisch worden gegenereerd op basis van parameters, zoals maten, materiaaldikte of geometrie. Sneller en duurzamer ontwerpen dus. In dit geval is het de printrobot die eindeloos kan variëren op basis van verschillende parameters. Je kunt bijvoorbeeld alle kolommen van een brug of viaduct een verschillende vorm geven. Er is daarnaast minder beton nodig voor hetzelfde resultaat. De printer legt namelijk alleen beton neer daar waar het nodig is voor de constructieve sterkte van de brug. We halen besparingen van 30 tot 40%. Maar voor de fietsbruggen die we voor Noord-Holland gaan printen denken we zelfs aan materiaalbesparingen van 50 tot 60%. Ook is er geen bekisting meer nodig, dus is er ook geen afval meer.”
Sneller, veiliger, goedkoper
Het gaat bij de 3D-geprinte bouwelementen zeker niet alleen om onderdelen voor bruggen. Het gaat bijvoorbeeld ook om elementen voor woonhuizen, kantoren en kunstobjecten. Een van de grote voordelen is dat er veel minder tijd hoeft te worden doorgebracht op de bouwplaats. Feitelijk hoeven de onderdelen alleen nog aan elkaar te worden verbonden, wat het hele proces ook veiliger maakt voor bouwvakkers.