Vitalfluid’s reactor feeds greenhouse crops literally at lightning speed
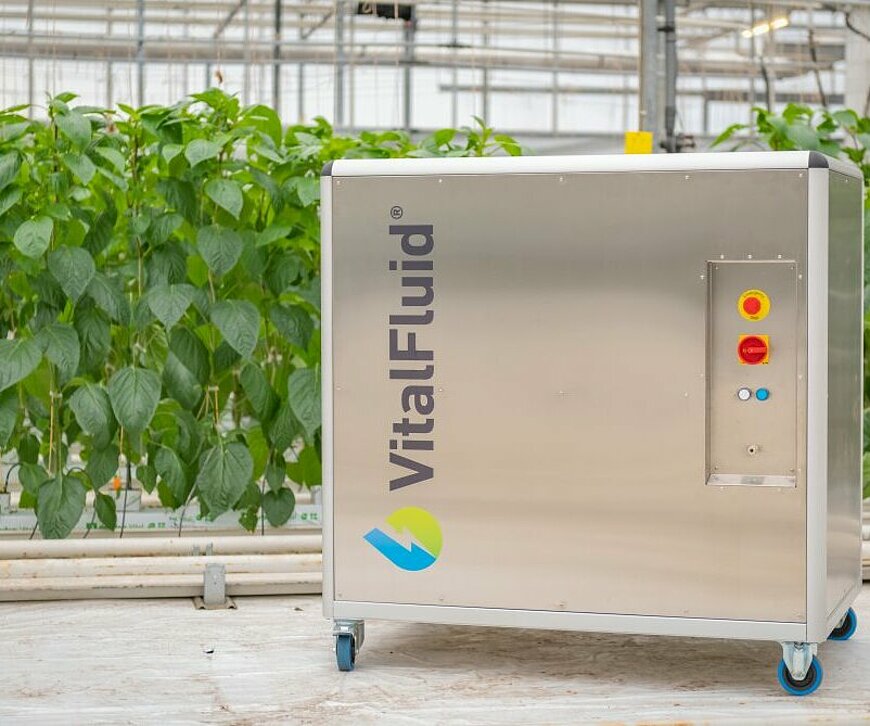
Crops in greenhouse horticulture can be fertilized in a sustainable way by mimicking the action of a lightning bolt.
Ever thought about why lightning happens? It’s one of the ways Mother Nature nourishes plants, trees and forests. The Eindhoven-based company VitalFluid has mimicked that process. By simulating the effect of one of these lightning bolts, it is now possible to fertilize greenhouse crops in a sustainable way. After years of research and testing in collaboration with the Eindhoven University of Technology (TU/e), among others, the company is now close to a breakthrough in the United States. The method could also be used for crop protection in the near future. An application for treating burns and skin diseases is still in a test phase.
CEO Paul Leenders founded the company VitalFluid in 2014 out of his previous company in response to a project with TU/e, Wageningen University & Research, Radboudumc and several companies from Nijmegen. “In that project, we researched medical and agricultural applications of plasma activated water. Those results were so promising that I founded VitalFluid together with co-founder Polo van Ooij from the TU/e. Later on we also started collaborating intensively with the TU/e on the development of the relevant electronics and on account of their test facilities. So it’s actually more of a ‘spin-in’ than a ‘spin-off’,” Leenders laughs.
Disinfectant properties
The theory behind VitalFluid’s application is not overly complicated. Using electricity, the machine brings ambient air into a plasma phase, the 4th state of aggregation (solid, liquid, gas, plasma). Ambient air is composed of 20 percent oxygen and 80 percent nitrogen. Those portions of oxygen and nitrogen become reactive and then dissolve into the water. As a result, this water temporarily acquires disinfectant properties. This effect disappears after about 20 minutes. What remains is water that contains nitrate, which is the most important nutrient for plants and crops to grow.
“That process is taken step-by-step from nature,” Leenders emphasizes it’s cradle to cradle design. “A real ‘nature-based process’; a ‘mimicry’ of a thunderstorm. Because exactly the same thing happens in a thunderstorm. When lightning strikes -and it does so about 8 million times a day – the air around that lightning bolt also enters a plasma phase. It is one of nature’s methods of fixating nitrogen. Ten percent of all fixated nitrogen on earth takes place through lightning. So, that represents a significant contribution. This is how nature feeds plants, crops and forests with nitrogen. It’s a really important natural fertilizer. We have managed to capture that process in a reactor.”
Bundling of processes
The process can be precisely controlled in the VitalFluid reactor. Which means that more or less oxygen or nitrogen can be added to the water as needed. However, a great deal of research was required in order to succeed. This is because the whole concept is a combination of various electrophysical and chemical processes. One of the main research efforts was to find the right kind of control equipment. “It was quite a challenge to get that process right. That’s also where our know-how is at the moment.”
A real ‘nature-based process’; a ‘mimicry’ of a thunderstorm.
Paul Leenders, ceo VitalFluid
Before founding VitalFluid, Leenders focused on the disinfection of living tissue using plasma activated air. “That was together with TNO (Netherlands Organisation for Applied Scientific Research) and Radboudumc back then. We demonstrated that you can disinfect living tissue very effectively and safely using this plasma technique. In that project, we also looked specifically at hand disinfection. But if you want to apply this in practice, you hit a problem. The gases that are generated during this process – ozone gases and NOx – should not be inhaled at all. They are toxic so that was a major problem. Professor Peter Bruggeman, who was working at the TU/e at the time, came up with the idea of first treating the water. You could then clean your hands with that reactive water.”
Collaboration with TU/e
This is how the collaboration with TU/e began, where the knowledge of electronic control systems in particular was used to build VitalFluid’s eventual application. A major advantage for Leenders was that by then there was a lot going on in the field of control electronics for high-voltage applications. For decades, the focus had mainly been on control electronics for low-voltage equipment. Such as computers, telephones and the like. It was only with the arrival of solar collectors and electric vehicles that these techniques were also developed for high-voltage equipment.
“We started out with lab units. With those, we were able to produce plasma activated water on a very small scale. We used those units and leased them to companies that were particularly interested in the disinfectant properties. That’s how we ended up dealing with seed breeding companies. These companies do a lot of R&D, which fits in well with what we do. It also involves relatively small quantities in a controlled environment. We learned a lot from that.”
VitalFluid’s ultimate goal is to bring a system to market that can irrigate large areas of crops with disinfectant water. The plants subsequently become more resilient to pathogens, and pesticide use is reduced. The European Union is also banning more and more crop protection products. Which means that companies will all be forced to look for sustainable alternatives.
Scaling up the process
“We are catering to the greenhouse horticulture sector. But for large-scale disinfection in that sector, so-called flow-through units are needed. We are still working on that. But it is one of our objectives. Our technology for administering fertilizers has already been scaled up, a development which was partly financed by the European Union. We are now going to market that application in the United States first.”
Yet VitalFluid wants more. Together with a number of other parties in India, the company is currently assessing the feasibility of using plasma activated water to treat burns, infected wounds and skin diseases. Projects for this are now in the works. VitalFluid outsources the production of the equipment for sustainable fertilization in greenhouse horticulture to other companies.
“In the Brainport region where we are located, there are plenty of companies that are much better equipped to mass produce these kinds of systems in series, We really see ourselves as an R&D-oriented company that develops equipment and applications in collaboration with our clients -our key partners.”