Start-up Zavhy plans to turn construction world upside down with 3D concrete printing
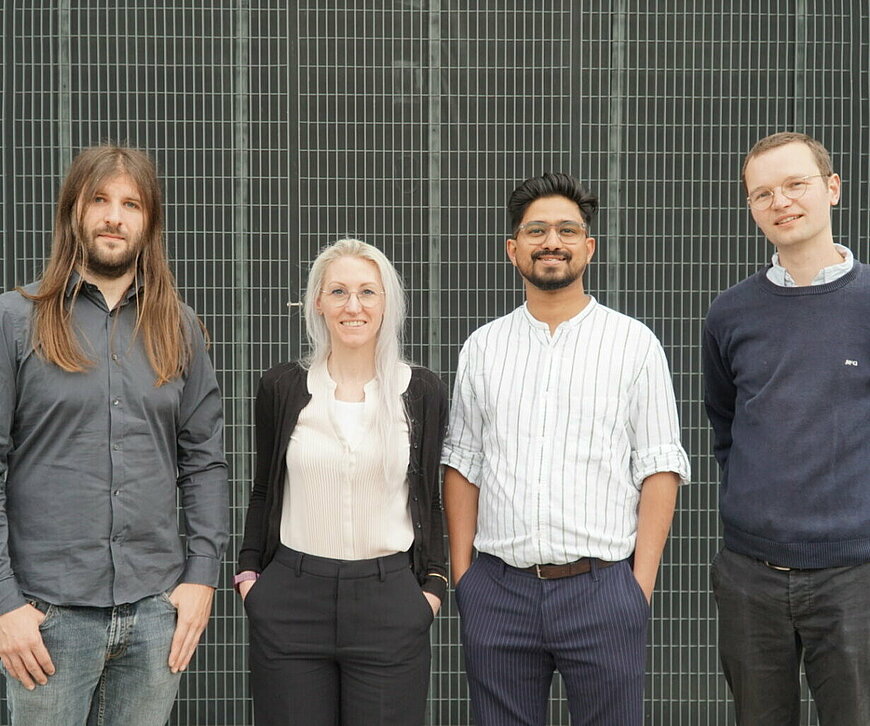
The construction sector lags behind when it comes to sustainability and digitalisation. Start-up Zavhy wants to change this with 3D concrete printing.
Spin-offs en Start-ups
TU Eindhoven is a breeding ground for new ideas that rely on scientific research. These ideas come a step closer to society in the form of spin-offs and start-ups, which are often located on the TU/e campus. In cooperation with The Gate and Innovation Origins, TU/e puts an innovative company that results from scientific research in the spotlight every month. This time: Zahvy.
In Nijmegen the longest 3D printed bicycle bridge in the world was put into use last year. What makes the 29-metre-long structure unique is that the architect had the design freedom to explore free-form shapes to optimise the structure. The realisation of the bridge was possible thanks to the research carried out by Zeeshan Ahmed during his PhD under Professor Theo Salet at Eindhoven University of Technology (TU/e).
Big ambitions
Zeeshan has big ambitions. He sees his PhD research as a way of developing knowledge about 3DCP, but he also wants to put the technology into practice. So on 1 April 2020, he founded start-up Zavhy.
Zavhy has a clear mission. The company wants to automate and digitise the construction sector and address its setbacks related to productivity, sustainability and affordability with 3D concrete printing (3DCP). “With 3DCP, we can build faster and improve the quality of construction. Besides that, the process will become cheaper and more sustainable, because of the efficient use of material,” explains the entrepreneur.
Especially in the beginning, things weren’t easy. “I started a company without any entrepreneurial experience. With Covid-19 everything got even more difficult. Without the support from my family, friends and colleagues at TU/e, it would’ve been impossible.”
That Zavhy’s mission is an important one, proves the MGI Industry Digitization Index. On this digitisation ranking, only the agricultural sector scores worse. In 2021, for example, only forty per cent of construction companies and clients used Building Information Modeling (BIM) software. This programme, which has been around for more than thirty years, is used in the construction industry to work together efficiently during planning, design and construction. Moreover, the sector emits a lot of CO2 and takes few reduction measures. Because of this high CO2 footprint, countless construction projects stand still every year, despite the fact that the construction sector in the Netherlands must be emission-free by 2030.
Reinforcement for 3DCP technology
During his PhD at TU/e, Zeeshan focused on finding a solution for two major disadvantages of 3DCP technology. One was the lack of steel reinforcement in 3D-printed concrete structures that provide strength. Besides that, additives such as fibres and aggregates that improve the material properties of concrete, were missing.
Keeping an eye to industrialise the technology, he developed two machines. One to add steel cable reinforcement into the concrete called Reinforcement Entrainment Device (RED) and a Fibre Reinforcement Entrainment Device (FRED) to add fibres and aggregates.
The RED system was used as one of the means to reinforce both the 3DCP bridge at Gemert (the first reinforced 3DCP bridge in the world) and the 3DCP bridge at Nijmegen. His research also contributed to the design and construction of the Milestone 3D concrete printed house in Eindhoven. “These projects allowed me to valorise my scientific research,” says Zeeshan.
The struggles payed off in July last year, when the start-up secured a REACT-EU grant of €420.000 to further develop the FRED system. In November 2021, a second grant (the MIT R&D grant) of €200.000 followed, which enabled the company to work on developing the RED system, too. Both the RED and FRED projects are being carried out in collaboration with engineering companies Van Beek and TBRM ES, who also received part of the funding. “The external recognition we received with those fundings, was very important to overcome any self-doubt we had regarding Zahvy. We could show everyone that what we’re trying to accomplish is important.”
It also helped Zavhy secure new collaborations with companies who are trying to address similar issues for the 3DCP technology. Zeeshan: “We’ve come full circle now that we have sold the first prototype of the FRED system to TU/e, so they can carry out new research.”
Besides that, the fundings contributed to breaking the vicious circle Zavhy was in. “Without money, we can’t hire employees or build a factory where we can demonstrate our technology. Then you don’t get anywhere. With this grant, we have been able to make important steps.” For example, an R&D material engineer Taco van Meeteren was recently added to the team, which in addition to Zeeshan consists of CFO Wendy Volkers and CTO Frits Rooyackers.
“The external recognition we received with those fundings, was very important to overcome any self-doubt we had regarding Zahvy. We could show everyone that what we’re trying to accomplish is important.”
Zeeshan Ahmed
Three business models
The young company consists of three branches. It develops and valorises new 3D printing hardware and software technology, it contributes to construction projects and is in the process of setting up a 3DCP facility in Eindhoven, where structures and designs can be printed. Ultimately, Zeeshan wants to franchise his company, to support the Dutch Governments goals of building a million houses by 2030. By 2025, at least ten other 3DCP franchises should be working with Zahvy’s system.
Because 3DCP technology is still so new, Zeeshan and his company have deliberately chosen to cover all aspects of the technology in order to best support the growth of the 3DCP market. He wants to create a consortium of companies and connect the value chain around 3D concrete printing so that issues can be addressed collectively. “That way, everyone involved in the construction industry could benefit from it and stimulate others to change their mind when it comes to 3DCP. It’s about the whole process. We need to valorise the technology and keep doing research, but also work on the hardware and software. And then apply what we do in projects. We develop the material, develop the system that allows that material to be printed, and contribute to the design and construction.”
Start-ups involved in 3D printing in construction are popping up like mushrooms, but for Zeeshan that is a good thing. “It’s not about my business. I want to support others and make construction more sustainable together. My biggest competitors are not the start-ups, but the traditional construction companies. I need to show them the benefits of adopting 3DCP technology and get them on my side of the table.”
Foto, v.l.n.r.: Frits Rooyackers, Wendy Volkers, Zeeshan Ahmed en Taco van Meeteren.
This story is written in collaboration with Eindhoven University of Technology.