Lightweight and efficient battery thanks to 3D technology and solid-state materials on thin film
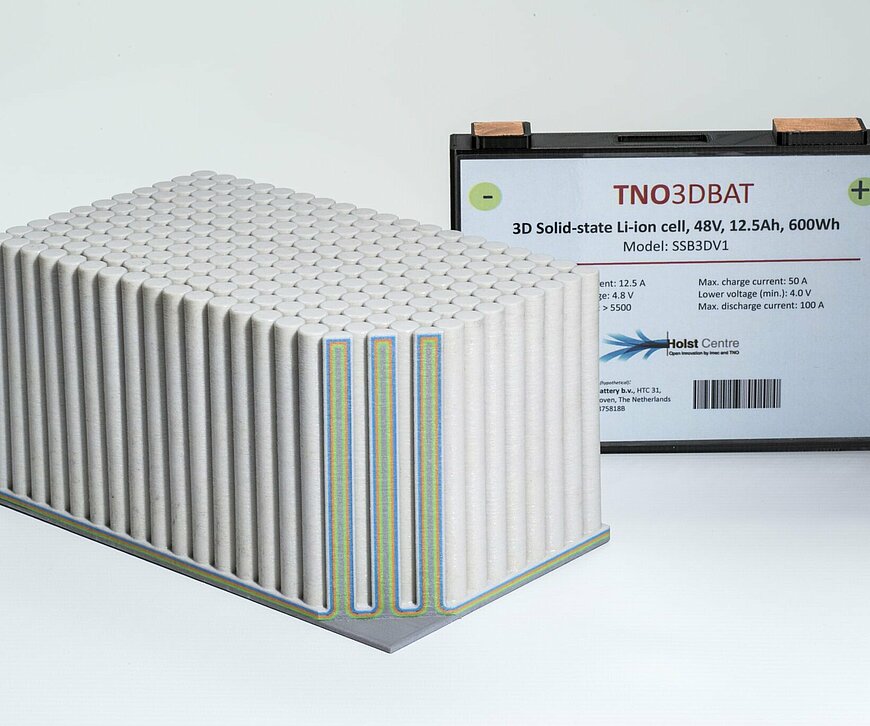
The spin off from TNO, LionVolt BV, has promised a 3D solid-state thin film battery that is lighter, safer and more efficient than current lithium batteries.
Batteries for energy storage, e.g., in electric cars, are becoming increasingly important. LionVolt BV, a spin-off from the Netherlands Organisation for Applied Scientific Research (TNO), promises to build a 3D solid-state thin film battery that is lighter, safer and more efficient than the current lithium batteries. The ‘Proof of Concept‘ has already been delivered. They are now waiting for investors so that the first pilot factory can be built. Will this innovation from the Dutch province of Brabant conquer the European market?
3D technology, thin film and solid state
Demand for batteries is growing. They can be used, amongst other things, to store sustainably-generated energy in electric cars. LionVolt BV, a spin-off of the Brabant TNO Holst Centre, offers a highly promising technology for future batteries. This innovative technology is not entirely new as it builds on an earlier concept developed by Philips Research. Underlying these batteries is a 3D technology and various solid material layers, known as ‘solid state’. This 3D structure is created using billions of rods covered with thin layers of functional material.
Advantages: third time lucky
What is promising is the combination of a 3D structure, thin film and a solid electrolyte that enables the conduction of electric current. “The 3D structure provides a large surface area as well as small distances between the electrodes,” explains Ton van Mol, managing director at TNO at Holst Centre in Eindhoven, The Netherlands.
“Because lithium ions only have to cover a short distance, this leads to very fast charging and discharging rates. As a consequence, the battery can be charged within 10 minutes. In addition, it can achieve an energy density that is two to three times greater than that of existing batteries. Which means that the batteries need to be recharged less often. This makes them more efficient than traditional batteries. In practice, this means that cars with such a battery on board would be able to cover a distance three times greater than at present.”
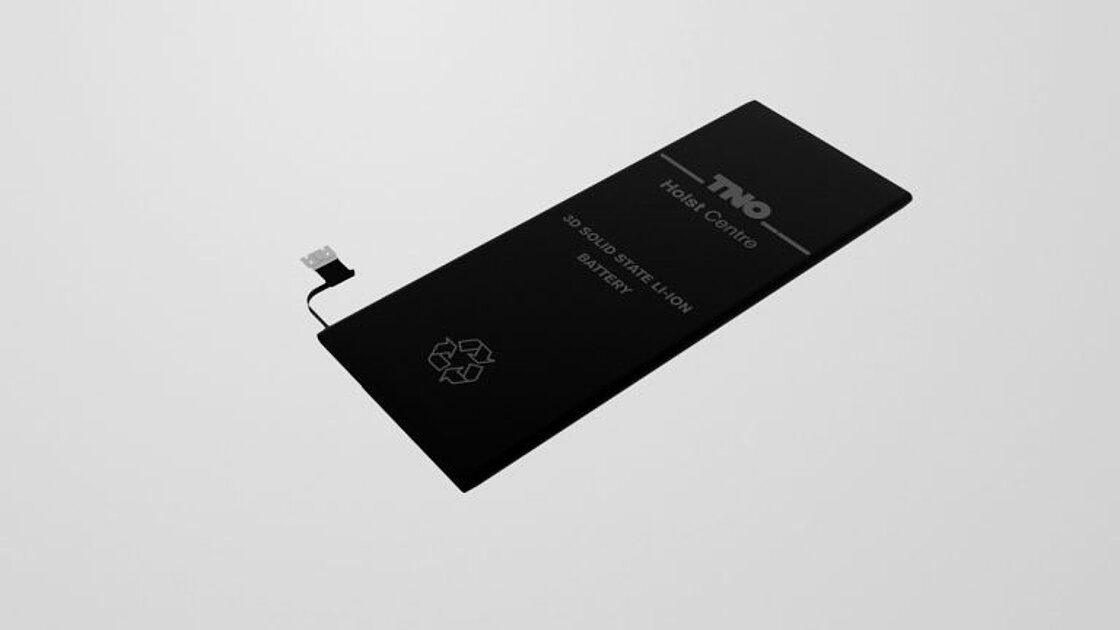
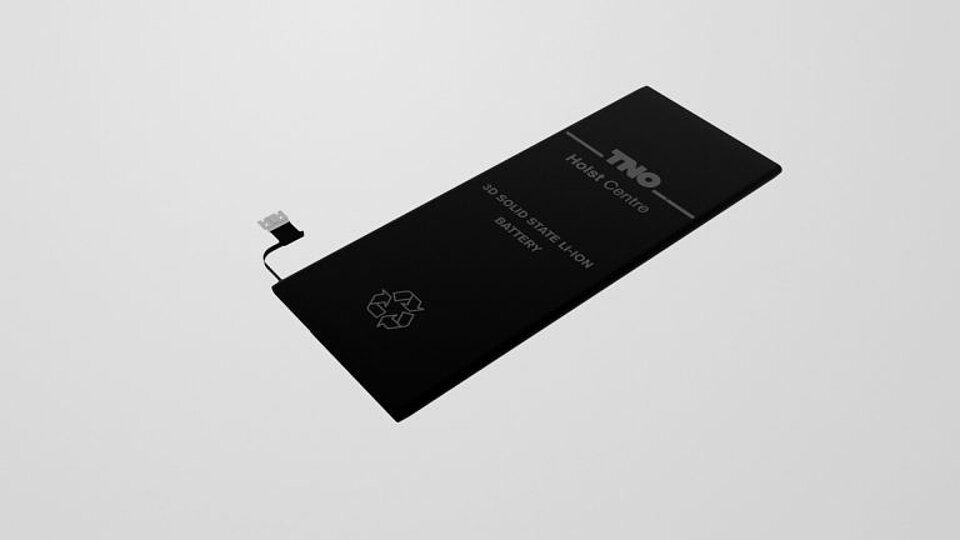
In turn, the thin film allows for more flexibility and a lighter weight. The flexibility of the material lends itself to applications in all kinds of clothing and wearables, while its light weight makes it especially well suited for vehicles, such as cars.
Finally, compared to “wet” batteries, which contain a liquid electrolyte, the ‘solid-state’ materials make them a lot safer. For one thing, they cannot leak. There is also no danger of them exploding or catching fire. Which is the case with the batteries that are currently often used in e.g. laptops and smartphones.
From proof of concept to pilot factory
New production technologies – which still need to be scaled up – are used to produce the batteries. Van Mol is optimistic, though: “With the production ‘spatial atomic layer deposition‘ technology developed by TNO and partners (a technology that has already been commercialized by TNO for solar cells) we can quickly build up large surfaces atomic layer by atomic layer. We now want to enter the market with this combination.”
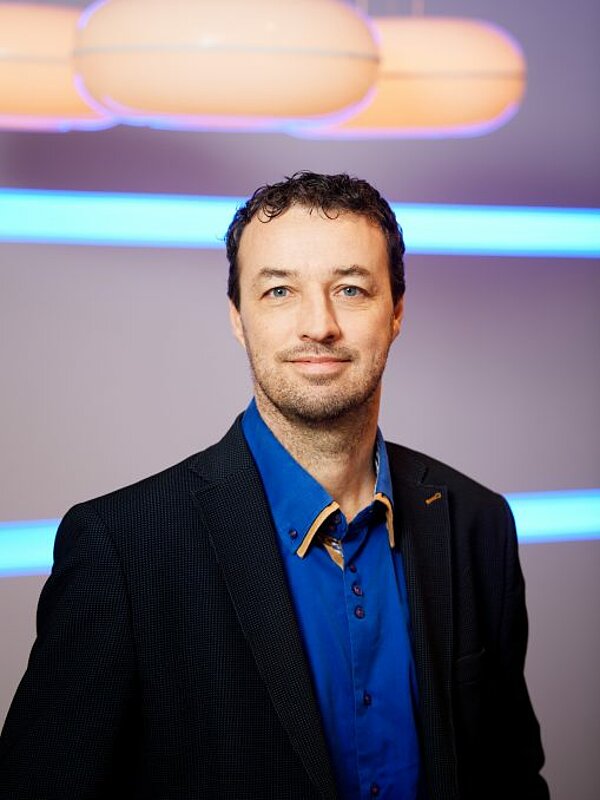
For the past six years, the Holst Centre has been working on a scalable model. This culminated in the founding of LionVolt BV last March. A proof of concept was achieved in December. Van Mol: “The LionVolt technology can already be used in all sorts of wearables. Such as wearable health patches that you can attach to your upper arm for telemonitoring patients.”
However, now is the time for investment so that the first pilot factory can be set up. Then it is a matter of scaling up, according to Van Mol. “For a disruptive technology like this one, you need to stay committed for a long time. And besides a lot of money, that also takes a lot of patience. It will take at least four to five years to set up the first pilot factory. This is why LionVolt will first focus on smaller volumes. We will then have to expand production step by step, one factory at a time.”
European alternative
The end goal for Van Mol is “a completely new architecture” for batteries. “This type of battery can be used for anything. It could actually offer a European alternative to current batteries, which at the moment are still all sourced from Asia.” But in that respect, Van Mol feels that this disadvantage also has its advantages. “Converting existing factories is very complicated and usually not very profitable. Whereas you can immediately set up a factory with the right facilities for this new technology.”
Less dependent
The good news is also that the market for batteries is huge. And Van Mol predicts that the end is far from sight. “Europe still has only a few of its own battery factories and a few more that are under construction. Meanwhile, car manufacturers are all lining up for them. For instance, Volkswagen recently said it would aim for 70 percent electric cars within five years. While also all kinds of other car manufacturers, from Volvo to BMW, are all also working on making their cars electric.”
And what about the future prospects for aircraft and ships, where weight is also an important factor? Van Mol does not yet dare to think that far ahead, although he is very confident about the outlook for the future. “With a battery from our own country, not only the Netherlands, but also Europe, will be able to become less dependent on Asian players. How wonderful would that be?! A factory, right here in North Brabant, that will also provide employment for thousands of people!”