Collaboration VDL Staalservice, Berlin Packaging Dangerous Goods and Lithium Safety Solutions for safe storage and transport of batteries
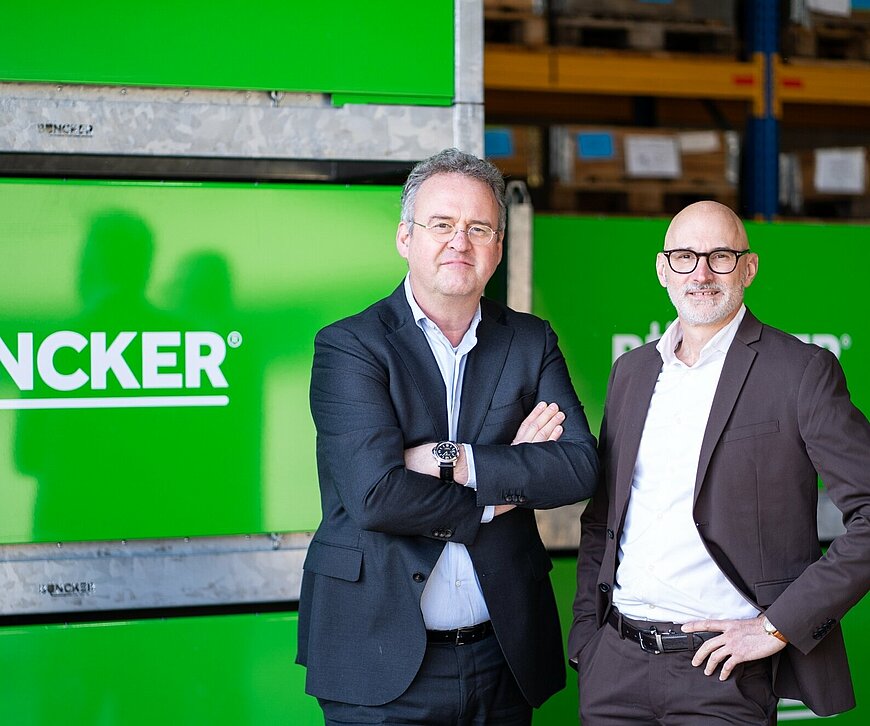
Due to the growing popularity of electric vehicles and the increasing demand for renewable energy, it is increasingly important to transport and store batteries in a safe and efficient way. That is why VDL Staalservice, Berlin Packaging Dangerous Goods and Lithium Safety Solutions are jointly developing BUNCKER®; a safe and user-friendly packaging solution for transport or storage of lithium batteries and battery packs that carry a risk.
The point of the story
Paul Malcontent, General Manager at VDL Staalservice, Lambert Dekkers, Sales Director at Berlin Packaging Dangerous Goods and Roel van Veen, expert in regulation and law on lithium-ion batteries at Lithium Safety Solutions are the initiators of BUNCKER®. Their goal was to create packaging for batteries that can withstand a massive battery fire (a so-called ‘Thermal runaway’), without the outside of the packaging becoming too hot. In addition, the solution had to be able to contain any hazardous gases released during a battery fire. Thus limiting the subsequential damage to the extent possible. “Two serious challenges, but we managed to come up with a solution we are very proud of”, says Paul. “The point of the whole story being that we literally had to change our way of thinking. Where other parties in this area opt for a container with a lid, we choose to do it the other way around. We put the product on a pallet and place a bell jar-like cover over it. Moreover, the double-walled cover contains BUNCKER®’s insulation material, preventing users from being hit by any loose debris. A unique solution. We also especially developed the insulation material, which doesn’t only have a thermal function, but also binds hazardous gases, such as hydrogen fluoride. This combination prevents gasses from escaping.”
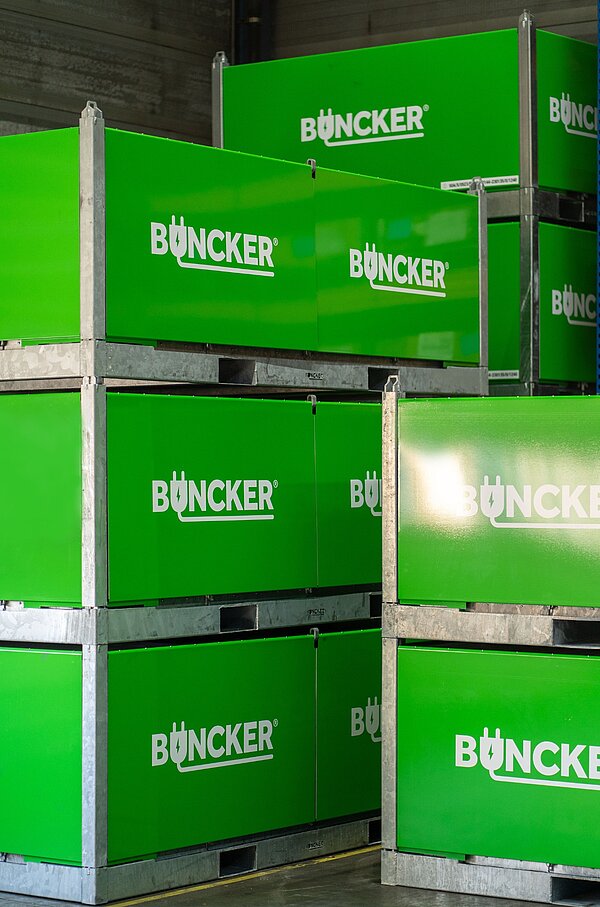
Meeting the most stringent criteria
BUNCKER® has been designed around safety and ease of use. This results in a box that can be used by anyone, regardless of knowledge and experience. By making sure the BUNCKER® design meets the most stringent criteria regarding transport and storage of lithium batteries, the box can be used in all situations. “Transport of hazardous substances is subject to UN certification and regulations, which consist of various modalities,” says Lambert. “Such as ADR, a set of regulations for road transport, IATA for transport by air, IMDG for transport by sea and RID for rail transport. The standards and classifications that all packaging must meet in relation to the status of the lithium battery that is being transported are laid down in these transport regulations. It is interesting to know that the person giving the transport order to an expert must have someone carry out a five-point assessment to assess if the lithium battery is stable. In practice, however, this is exceedingly difficult, if not impossible, for most companies. You will always have to think of the worst-case scenario from a safety point of view and thus use appropriate packaging. If you do not, you are liable if things go wrong. This is especially the case when transporting repurposed or recycled lithium batteries. In addition to transport regulations, there are specific regulations for storage of lithium batteries not being used; PGS 37-2 (Publication Series on Hazardous Substances 37, part 2).
Any company using lithium batteries or battery packs must comply with these regulations. When developing BUNCKER®, we made sure to comply with both transport and storage regulations, because for a company transport and storage are intrinsically linked.”
Trademark design
Apart from the fact that both model and technology differ from any existing solutions, BUNCKER® stands out in terms of design. “We really wanted to create a trademark BUNCKER® design”, Lambert clarifies.
Progress through collaboration
Collaboration is an integral part of Brainport Eindhoven’s Green Transport Delta - Electrification (GTD-E) project. Dozens of Dutch companies are working together as part of this project to develop a strong battery ecosystem to accelerate the transition to climate-neutral mobility. Paul: “That is the best part about collaborating as part of GTD-E; everyone focuses on a specific aspect in the development of a strong battery ecosystem. The project will last for another year. All parties are taking significant steps and ideas are becoming increasingly concrete. It would be great if this would eventually lead to cross-industrious innovation. We meet the other parties during physical meetings and that certainly has its added value. The inter-relationship between parties is great. Dismantling and recycling of batteries are also key themes within the work packages. We may be able to get involved with BUNCKER®, because dismantling and recycling also include transport to varies locations.”
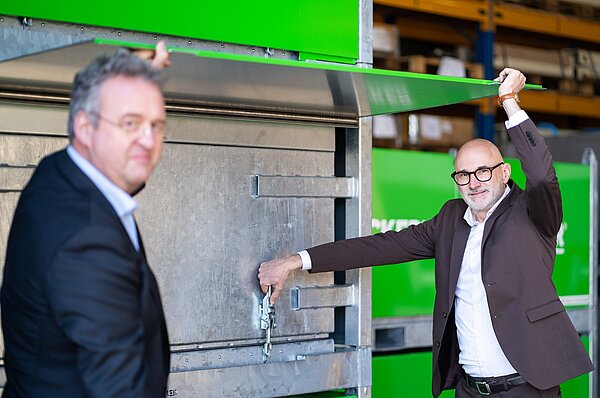
Oldest child
BUNCKER®’s development stage has now been completed and certification is currently underway. The innovation has partly been certified, but it is quite complex to get full certification. “I sometimes compare it to the oldest child in a family, who wants to go clubbing for the first time. We are that oldest child. So, it is immediately clear that we are the first ones to approach the authorities on this topic. They still have to get used to that. It will be a lot easier for organizations that come after us. The standard contains requirements open to interpretation in some respects. We notice that transport authorities interpret these requirements differently and that public authorities are having difficulties making a decision. That is a pity of course,” says Paul. “Because we want to move forward.”
Looking at the neighbors
“In Germany they are quite ahead of us. They already started this process a few years earlier,” Lambert adds. “The German testing authority and the public authorities work closely together because they are closely linked. In the Netherlands and Belgium, they are separate bodies that still have to find a way to work together. In Germany, similar packaging has already been extensively tested and approved for the market. Things are now running smoothly over there.”
There is work to be done
The men are positive about participating in the GTD-E project. Lambert: “A huge advantage is that the project helps us build a network. We have now developed our boxes in five different sizes, and we have already gained some new ideas in this area. One of the knowledge institutes might be able to help. In addition, quite a few automotive parties are involved in the GTD project. They will also electrify their own fleet eventually. Which will be interesting for us because they will be able to use our product. And the recycling parties that are part of the project can use our product to safely transport batteries to their location.
This collaboration between organizations in the field of electrification is important. We are all working with lithium batteries; one party as developer, the other as innovator and the next party focuses on recycling. And each party also has to think of storage and transport."

BUNCKER®’s role
Will these innovations also impact the Dutch citizens? Paul thinks so: “I hope we can help realize a safer living environment. You can hardly open the newspaper without reading about another fire. Either at a waste processing company, a transport company, or a ship full of electric cars. We hope that our product will help improve safety in such situations. People are still quite ignorant; they often do not realize how dangerous some situations are. For example, think of the fun bicycle shop in the city center, which is situated on the ground floor with some nice apartments above. Nowadays, such a store is packed with batteries, which can cause quite a fire. Packaging those batteries in a safe way will limit the risks.” Lambert: “The boxes we have already developed are quite large.
The next step is to develop smaller packaging for critical batteries, which will certainly impact consumers. You will find them in bicycle shops or supermarkets for example.”
Safe living
Hence, we are also developing solutions for small batteries that can be used by consumers. “What people often don't realize is that batteries become increasingly unsafe as they get older”, Paul continues. “The battery of an electric bicycle, for example, works well in the beginning. At some point the bicycle will fall over, is left outside in frost and rain, or is standing in the sun. Such a battery to endure quite a lot before you start noticing it. Each battery has an end of life. The nearer to that end of life, the more dangerous the battery becomes. The industry, but also politicians, are not sufficiently aware of this.
Today's batteries all will have to be recycled or removed from the market. More stringent regulations will improve the safety of bicycle repair shops, garages, and all other places where you can bring batteries for service, maintenance, or recycling. The BUNCKER® might be of added value in all these situations.”