Pivot Park and Brainport have to get off their islands, but how?
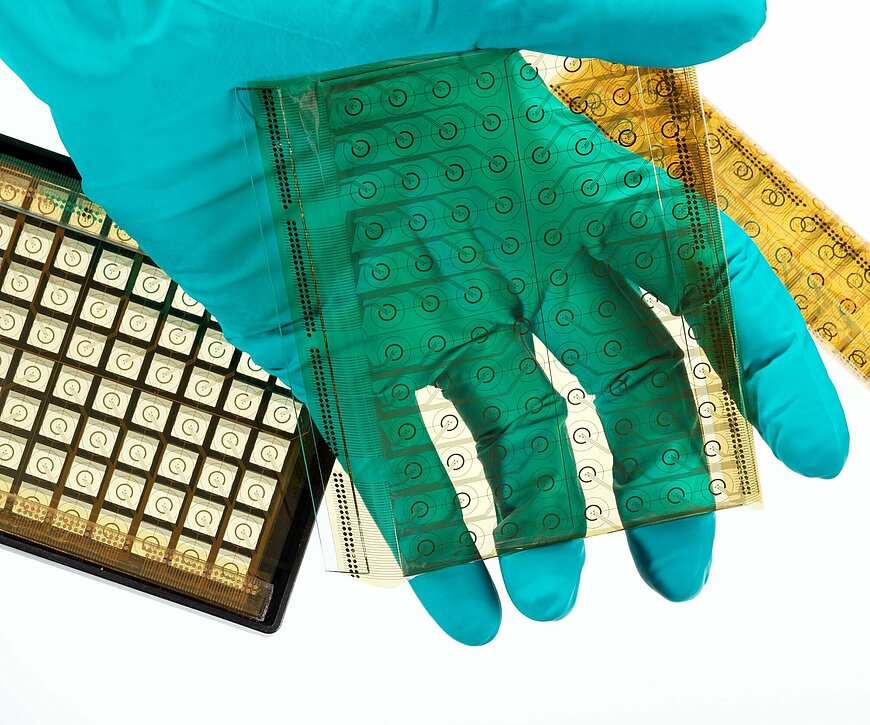
From applications used in batteries, lighting and displays to the life science sector. Holst Centre is doing it all, but those who change course have to be able to cope with a few bumps along the way.
The Dutch province of Brabant occupies a leading position when it comes to medical technology: one in five Dutch MedTech companies is based there. The life sciences and pharmaceutical sector in North Brabant is at least as robust. The sector has an annual production value of five billion euros - half of the total Dutch turnover. If it were up to Jaap den Toonder, professor of Microsystems at the Eindhoven University of Technology (TU/e), the time when the two sectors operated on their own separate islands would come to an end sooner rather than later. What will it take to make that happen? The answer from Den Toonder and Auke Kronemeijer (research manager at Holst Centre) is unanimous: transparency and trust.
Holst is a research center on the High Tech Campus in Eindhoven that specializes in flexible electronics and sensor technology. Traditionally, the institute has been known for applications in vastly different sectors. For example it has made 3D batteries, lightning technology and flexible displays. From 2016 onwards, the center has started to develop technology for healthcare applications.
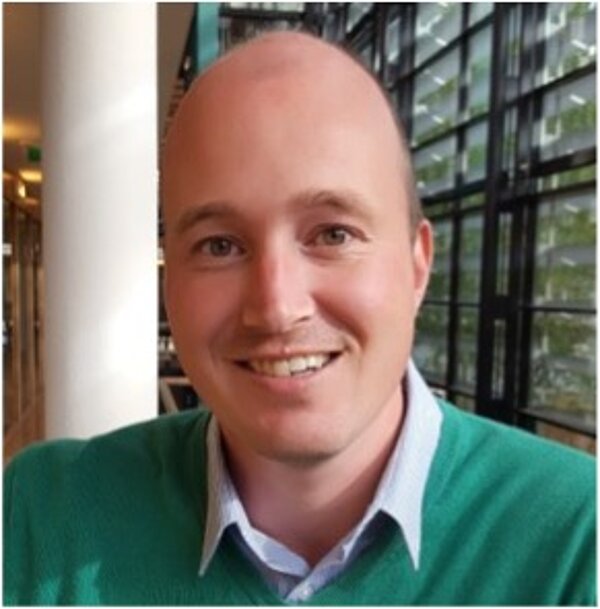
A new direction
In the past year, Holst has been steering more towards a biomedical strategy, as it expects the sector to grow at a rapid pace over the coming years. "Our society is aging. More and more diagnoses will be made at home and more and more care will be provided to people in their own homes. We are tapping into that," Kronemeijer explains.
For instance, Holst specializes in hybrid printed electronics, which it uses - in collaboration with imec - to make minuscule devices that can be incorporated into bandages, clothing or special plasters. These 'health patches' can be worn for seven days and measure, among other things, the heart rate, breathing frequency and level of oxygen saturation in the blood. All information is collected on a chip, which then sends the data to a mobile phone or the cloud. This allows patients to be monitored from their home environment.

Building trust
In the first 30 conversations Kronemeijer had with biologists and pharmacologists he had to explain exactly what they do at Holst. "We still have to build our name in the biomedical industry. Only after parties have become familiar with us, is there room to ask naive questions and sore points can be raised. Which is where open innovation comes in."
Den Toonder also finds that people have to get used to each other before they are willing to lay their tough cards on the table. In order to build up that trust, ICMS - the Institute for Complex Molecular Systems to which Den Toonder's research group belongs - pays visits to companies at the Pivot Park.
"At the university we have the knowledge, we are developing new technology. But, we are unable to implement a product in an already existing technology," Den Toonder explains. For that, ICMS needs parties like Holst. That's why we go to the Pivot Park in Oss to understand what the people who eventually have to use the technology need.

Organ-on-a-chip
The Organ-on-a -chip project - which has received millions euros in subsidies and which Den Toonder oversees - involves technologists, biomedical engineers and pharmacologists working together. The ultimate goal is to develop a standardized technology platform that links organ chips together to simulate a human body. This will enable new medication to be developed and tested in an environment that is as true to life as possible.
Holst Centre is also taking part in the project. Albert van Breemen, senior scientist (i.e., 'manufacturing technologist') at Holst, explains that a clump of human cells needs to be placed in an environment where electrical measurements can be taken. To see exactly what effect a drug has on the cells, for one thing. "Our task is to develop a platform on which electrical tests are possible on a large scale, for example, on neurons or brain cells that are already 'electrically active' by nature. This way, we will ensure that these types of tests can be fully integrated into the development process."
Much to learn
Being part of a biomedical project means having to learn a lot, says Van Breemen. "The first reaction of pharmacologists to our platform was: 'All well and good, but have you checked to see if the cells like the containers?' We didn't have any experience with that at that point."
Smart microtiter plates are another example, these are bits of plastic that Holst adds electronics to. This makes it possible for pharmacologists to conduct a large number of experiments and generate data within a short period of time. "But, then, it is important to know that the pharmaceutical industry is equipped for plates of seven by twelve centimeters. Automated measuring equipment in all laboratories is set up to that standard. We can still make such an ingenious plate, but as long as it does not meet those dimensions, it will never be put into practice."
It is important that people have the courage to ask naive questions, without being afraid of appearing stupid, concludes Den Toonder. As long as that happens, he is extremely optimistic about the opportunities for the medtech sector in Brainport, the region around Eindhoven. In this respect, a stronger link with Pivot Park in Oss is indispensable, he believes. "Technology and pharmaceutical science can no longer do without each other; they are becoming increasingly intertwined. If these two worlds learn to speak each other's language, the opportunities are endless."