LeydenJar: unique technology as the key to efficient and clean global battery production
A successful energy transition requires super-energetic batteries with a low footprint. Coincidentally, the renown Dutch research institute TNO came across a discovery that could mean a huge breakthrough in this area.
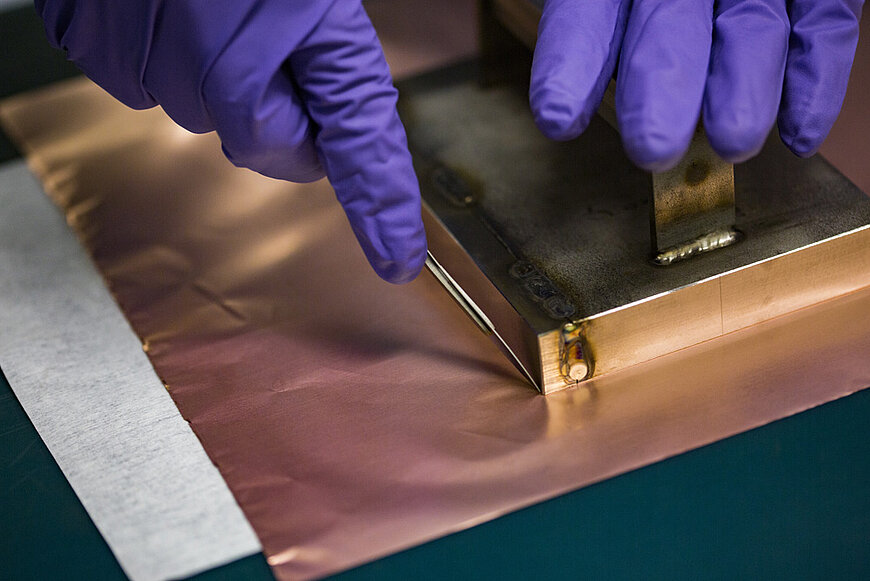
By making anodes from pure silicon, the storage capacity of batteries increases by at least 50%.CO2 emissions from the production process are drastically reduced. The technology has been embraced by CEO of the Eindhoven-Leiden start-up LeydenJar, Christian Rood and his business partner. The company now consists of a battery lab, a pilot plant and twenty employees. LeydenJar's battery technology is expected to be market-ready in 2022. ‘Our ambition is to use our technology to provide battery manufacturers worldwide with the key to the sustainable production of highly energy-dense batteries.’
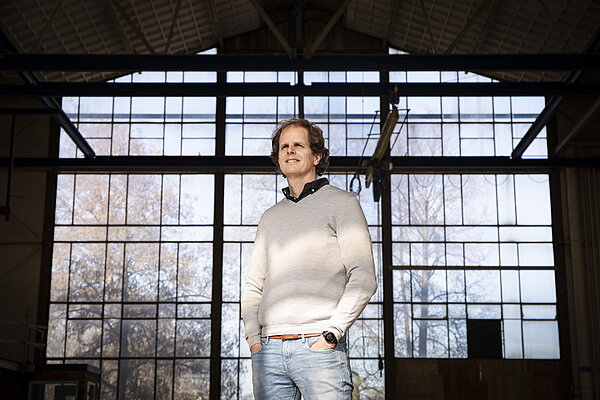
“At LeydenJar, we are working on breakthrough battery technology with the highest energy density in the world,” says Rood. “Current battery technology, the lithium-ion battery, can never reach this type of density. The anode, or the negative pole, is the biggest obstacle here. That anode now consists of copper foil, carbon and graphite. We still use copper foil but replace the graphite with silicon. This means that the storage capacity of the batteries on the negative layer is 10 times as large, which causes an increase of the energy density of the batteries by at least 70%.”
CO2 emissions during production 85% lower than production process of regular batteries
“What also sets us apart is how clean the process involved in producing batteries with our technology actually is. When you produce anodes with our technology CO2 emissions are 85% lower. Mining graphite has a major impact on the environment. Silicon, on the other hand, is one of the most available raw materials on earth. The footprint you leave behind is many times lower.”
Pioneering with the energy storage of the future
“We are one of the few companies in the world that can make pure silicon anodes. Normally this breaks down because silicon expands enormously when you use it to store lithium ions. You have to do something special to prevent that from happening. Coincidentally, TNO discovered how when making thin film solar technology. Because they used plasma to apply thin layers of silicon, a certain porosity was created in the silicon. That was not suitable for solar cells, so the project went into the fridge, but later the inventor realized that it was very suitable for battery technology and for pioneering with the energy storage of the future.”
Perfect example of a crossover and therefore unique
“At that moment I came into the picture. Due to my background in investment banking in areas such as cleantech, I have a good relationship with TNO. I had previously guided some of their promising technologies to commercialization. I founded LeydenJar in 2016 together with my business partner Gabriël de Scheemaker. The production process that we use comes from the semiconductor and solar industry and has never been used in the battery sector before. It is a perfect example of a crossover. As a result, we really have something unique here.”
Pilot plant in Eindhoven and battery lab in Leiden
“LeydenJar works from two locations. In Leiden we have a battery lab for making prototype Li-ion batteries based on our silicon anodes. Our main goal at this location is to make the battery's energy density as high as possible and the lifespan as lengthy as possible. Our other location is a pilot plant for silicon anode roll production of 400 m2. It is in Eindhoven. There our focus is on making the production process suitable for industrialization. Brainport Eindhoven is an excellent location for this. We can work with many parties who have experience in this technology, and it is easy to find people with experience in these types of high-tech industrialization processes.”
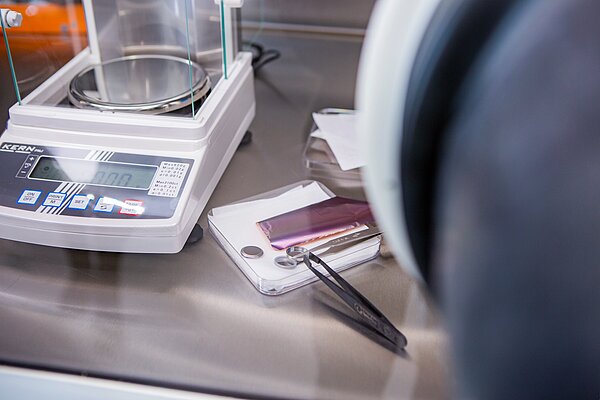
Creating ‘ASML for batteries’ requires thinking big
The Netherlands has an opportunity to create an ‘ASML for batteries’. Making progress in the density of batteries will have huge impact, just like in the chip industry, where circuit density enables a wave of product innovations. This impact varies from driving electric cars for a longer distance to enabling smaller, smarter consumer products and to enabling new industries such as electric flying. As a country, we need to think big, invest big and claim a position in this rapidly emerging industry.”
Resources needed for growth
“After our start, we had three months to prove that our technology was really valuable and to deliver a prototype. This required a relatively small amount of funding. A requirement for funders was that the prototype must be able to load and unload 100 times at a certain capacity. We have more than achieved that. In total, we have now raised around 7 million euros in various phases, a combination of equity, subsidies, and investments. That took time and attention, but we managed. We expect to complete our first commercial activities next year. Now, our efforts are focused on closing another major financing round.”
Market entry in three phases
“We bring our technology to life in three phases: we start with sampling; with these samples the manufacturers can make a number of batteries themselves. The second phase is a proof-of-concept, the third phase is a design-in, then our technology is drawn into the customer’s product. That is the phase that we are currently approaching. When marketing our technology, we start with the markets that demand the least in terms of cost and lifespan: wearables and other special applications. We then move on to consumer electronics. A battery must be able to charge and discharge 500 times. Our ultimate goal is automotive and storage of sustainable energy at home. To do this, a battery must be able to fully charge and discharge 800 times and then it still needs to have 80% of its original capacity.”
Making technology more efficient and production process suitable for industrialization
“At the moment we have to deal with a number of challenges before we can go to the market. First, we need to make the technology and production process as efficient as possible. Second, the production process must be faster, so that you end up with the same cost price as lithium-ion batteries. We are therefore developing a street with plasmas through which the copper foil is guided. We do this together with several organizations in the Netherlands and Germany.”
Ensuring visibility of distinctive Dutch battery technologies
“In Europe, the establishment of 24 giga battery factories is planned to reduce our dependence on batteries from other continents. This would make Europe the largest battery producer in the world. Then you must also differentiate yourself from the rest of the world. It must be cleaner and faster. In the Netherlands we have various highly promising technologies for this. That is why we work closely with parties such as Brainport Development and other Dutch parties working on breakthrough technologies. Together we work on our visibility in Europe. Our right-to-play as the Netherlands is mainly based on our non-traditional production processes that can have a significant impact on battery performance.”
Creating a healthy ecosystem through breakthrough technologies for societal challenges
“When we talk about the future, I believe in decentralized energy storage. We will generate and store energy closer to home. Batteries are essential for this. I want to make a difference in that. My personal motivation as an entrepreneur is to align inventors, public and private financiers, battery producers and end customers in order to come up with solutions for this major societal challenge, with a major impact for everyone involved.”