Additive manufacturing drives innovation in the Brainport medical technology sector
A lab-on-chip, an intervertebral disc, or an ultra-thin grid in an X-ray machine. All examples of applications with 3D printing in the medical world. Promising production technologies in a world where new products have to meet strict quality requirements. Three companies from the Brainport region are entering the medical market with this kind of "Additive Manufacturing".
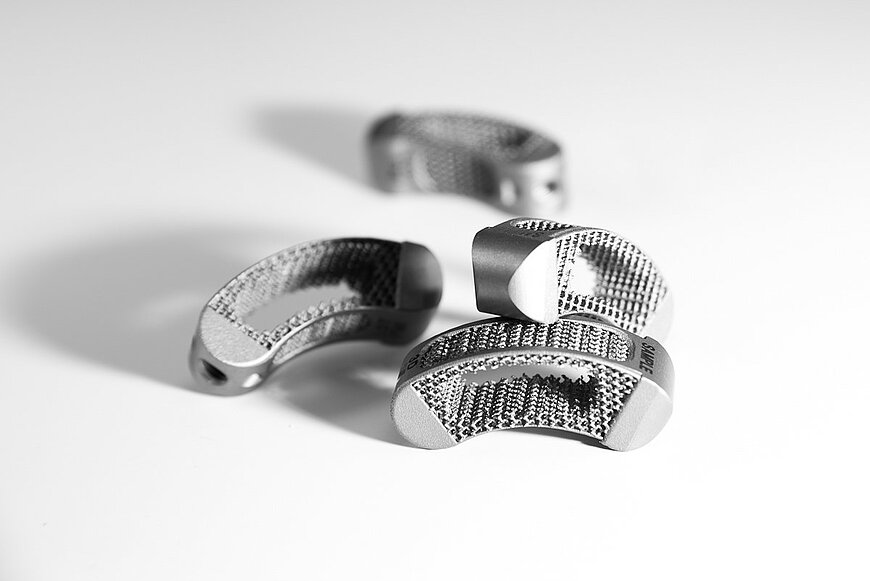
Keiron
Keiron wants to further develop and market the laser printing technology researched and validated by Holst Centre. Last September, the start-up took part in the HighTechXL program, which builds companies around existing and yet to be developed 'deep-tech'.
The technology Keiron is working on is a laser printing method to create functionalities on microfluidic chips. These chips can be used to study liquids and gases on a micrometer scale. "We are developing a method that is affordable, flexible, and scalable," says co-founder Jimmy Sy-A-Chin.
"We are developing a method that is affordable, flexible, and scalable"
Founder Jimmy Sy-A-Chin
On an empty chip, there are all sorts of mini channels. These channels are connected to a point where liquids come together. A laser prints functionalities over the test lanes on the chip, as it were. "This way, you make sure you control the flow of the liquids. That is the basis of what we call a lab-on-a-chip". You can, for example, run blood through the chip, which in turn reacts to, for example, a diabetes test.
"This lab-on-a-chip technology can save an enormous amount of time in the hospital," says Sy-A-Chin. Until now, all blood values have to be tested in a lab. "This can sometimes take up to three days. Sy-A-Chin, therefore, thinks that the first applications of the chip may be in hospital laboratories. But his ideal image is that people will soon also be able to test their blood at home.
Holst Centre worked on this technology for ten years. Keiron is developing a machine that can produce microfluidic chips. With subsidies from, among others, the Netherlands Organization for Scientific Research (NWO) and a subsidy applied for together with Holst Centre at Metropool Regio Eindhoven (MRE), the start-up wants to build the first machine. To show that it works, says Sy-A-Chin. "We have set out a timeline in which we want to bring our machines for mass production to the market in 2025.”
FMI
The metalworking company FMI looks at 3D printing as a strongly growing production branch. The company has branches in the Netherlands and Germany and, among others, ASML and Philips as customers. "Milling is a well-known technique", says Jelle ten Kate, Team Lead Additive Manufacturing at FMI. It remains important, he adds. "I see 3D as an additional machining technology."
Together with KMWE, NTS Group, Frencken, Machinefabriek De Valk, MTA, Philips Innovation Services, Kaak Group, and Additive Industries, FMI participated in a pilot 3D printing plant, AddLab. In that pilot, these industrial partners developed a set of 3D metal printing applications for high-tech and high-end production. This pilot started in 2013 and ran until October 2016. "Based on the experience with AddLab and the demand from the market, FMI eventually decided to purchase a 3D printer of our own," says Ten Kate.
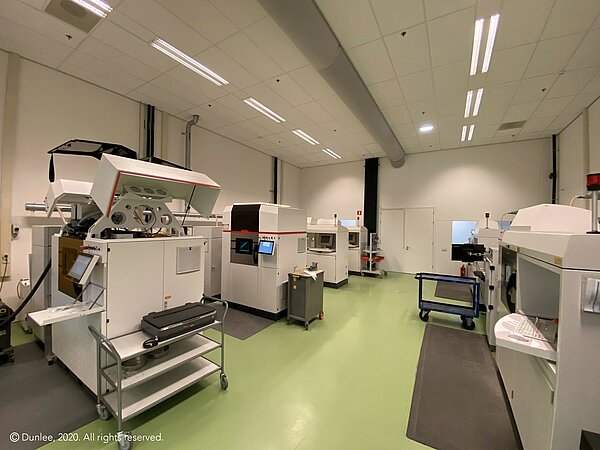
"We saw the potential of it. The first 3D printer turned out to be the fundament of today's success". Among other things, the company prints first prototypes for customers, as well as an entire production line for orthopedic implants and instruments. Such as intervertebral discs for the spine, hip implants, and applications for the knee. Tens of thousands of implants were 3D printed for customers in Europe and America. "Our products fully comply with the quality requirements applicable in Europe and America.”
The range for 3D printing is enormous, says Ten Kate. "There are dozens of different techniques and hundreds of materials to print with. What we do has the collective name of 'powder bed fusion'. A product is created by literally fusing powder. "You merge a layer that solidifies. After that, a new layer of powder is formed, which melts, solidifies and so you build up the product layer by layer.”
According to Ten Kate, the biggest advantage of 3D printing is that it also works with very complex shapes. "This allows an implant to grow very well in your body. A printed intervertebral disc has the same mechanical properties as the bone, due to its open structure”, Ten Kate explains.
Comparable to the current implants are FMI’s titanium prints. "With 3D printing, the finish is very important. It is not the most precise production technique." To get it smoothly into a precise size, it still has to be twisted or milled, for example, and cleaning the 3D printed parts is a crucial step, says Ten Kate. "We also have those techniques in-house.”
"We saw the potential of it. The first 3D printer turned out to be the fundament of today's success"
Dunlee
The international company Dunlee uses the ultra-fine material tungsten for its 3D printing. The wire in a light bulb, for example, is made of that material. Dunlee sells medical components for imaging systems such as CT scanners, MRI scanners, and X-ray machines. Dunlee is headquartered in Hamburg and has an office in Best, near Eindhoven. This site produces grids for imaging systems and has the largest tungsten printer park in the world.
As early as 2007, Dunlee began to explore the possibilities of 3D printing, together with its partner EOS. One promising possibility appeared to be the so-called 'anti-scatter grid', which limits the amount of radiation that reaches the film, or detector, in radiographic exposure. "Normally, these are made from lead or molybdenum plates," says Jan Grage, Product & Business Development Manager 3D Printing at Dunlee. "But the best material turns out to be tungsten. Because of the density of the material, it can absorb radiation best, compared to all other metals."
Dunlee developed a technique that allows you to print the thin material in a very targeted way. "The big advantage for our customers is that we can offer them all design freedom and we can print walls that are thinner than eggshells."


The breakthrough came in 2014 and the company has been producing 3D printed anti-scatter grids on a large scale ever since. Starting in 2018, more and more printers will be added. "Our site in Best now has dozens of those machines. They run 24 hours a day, 7 days a week."
Because much of what Dunlee does is covered by a non-disclosure agreement (NDA), Grage can say little about the projects the company is currently working on. "The use of 3D printing as a viable source for components is increasing exponentially, but there is still a long way to go.” Grage notes that there is a large market for 3D printed pure tungsten and that more and more companies are "opening up to explore the possibilities with us".
In spite of this confidentiality obligation, there is plenty of consultation with companies from the Brainport region. "3D printing is not only about the technology, but also about the steps around the print job. This includes internally developed finishing capacity and the purchase of high-quality materials. There are plenty of companies in this region with whom we can exchange ideas. And local companies come to us as well. They want to find out what they can do with tungsten."
Brainport Mindset
Sy-A-Chin of start-up Keiron experiences a lot of openness between high-tech start-ups. "I also worked with start-ups in Hong Kong for a while, with a totally different work culture. There they are afraid of losing something they don't have yet. If you compare that to Eindhoven, most start-ups here just talk as if they have all the patents in the world. Only then does the question arise as to whether we are competitors. Here we look at how we can find solutions in which we can bring something big to the market together. I love that mindset."