Prodrive Technologies uses AI to accelerate automation of manufacturing industry
Jeroen Spijker is program manager Industrial Automation at Prodrive Technologies. Together with Quinten Oostvogel, who is involved in the program as project leader, he works on accelerating the automation of the manufacturing industry so that the industry becomes more efficient, qualitative and sustainable. Prodrive Technologies mainly uses AI to detect defects by applying visual inspection to improve internal processes. With success. Prodrive Technologies is committed to achieve zero defects for all deliveries to its customers.
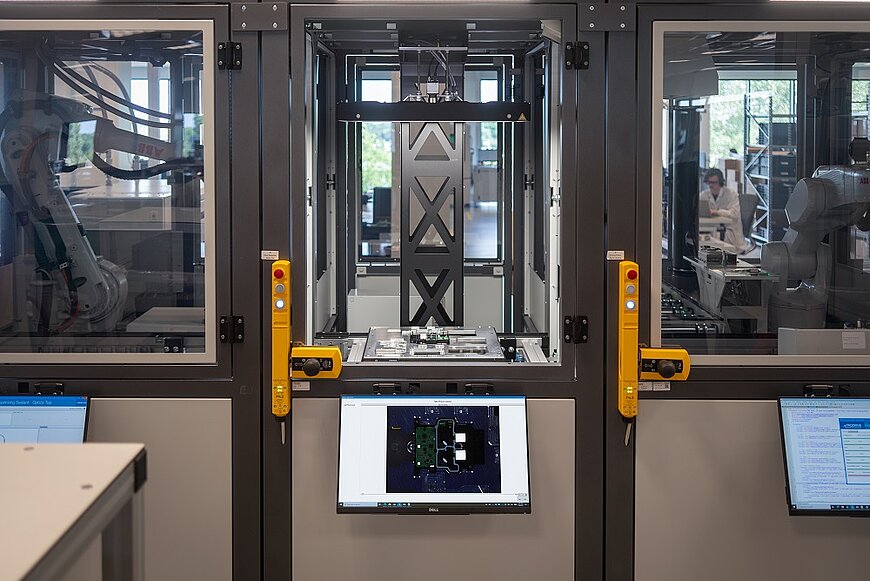
“At Prodrive Technologies we are organized in six technology programs,” says Jeroen; “Industrial Automation is one of those technology programs. We are a supplier of factory automation, both for job shop environments where small series of complex products and components are made and for repetitive processes that occur in the manufacturing industry. These kinds of operations range from injection molding to milling, system assembly and so on.”
AI as enabler for transition manufacturing industry
“The mission of our program is to accelerate the transition of the manufacturing industry towards autonomous and sustainable production. We do this through automation and digitization. We want to achieve improvements in productivity and quality. In our own factories we are automating logistics, manufacturing and testing as much as possible. Applying AI, in fact, enables Prodrive Technologies to grow and achieve sustainability and productivity goals at the same time. Our ultimate goal is to set up a factory of the future, a so-called Lights-out factory.”
Visual inspection to identify defects
“Our first application of AI is automating internal processes such as human visual inspections.” explains Quinten. Our aim is to speed up processes and increase quality. We usually deal with a high mix of products with a low volume, but in some cases also with mass production such as in the automotive industry. In both cases, visual inspection helps us to see where errors arise in the production process. This enables us to improve processes. As a result, in the end, you have fewer defects and higher yields. In this way you reduce waste and add value. That is interesting from both a sustainability and economic point of view.”
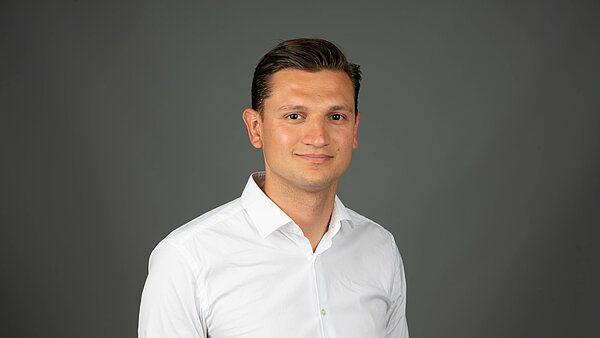
AI that is supportive to mechanics
“We do noy only apply visual inspection in production lines but also at workstations. This means that mechanics are supported in their work by a camera with AI algorithms. A person simply cannot work accurately for eight hours in a row. The AI algorithm, for example, checks whether screws are installed in the right place. Accordingly, a mechanic will receive a confirmation. AI supports people and ensures that they can do their job better. During this process, it is important that the model can explain why, for example, it indicates that something is defective so that the mechanic understands why it was rejected.”
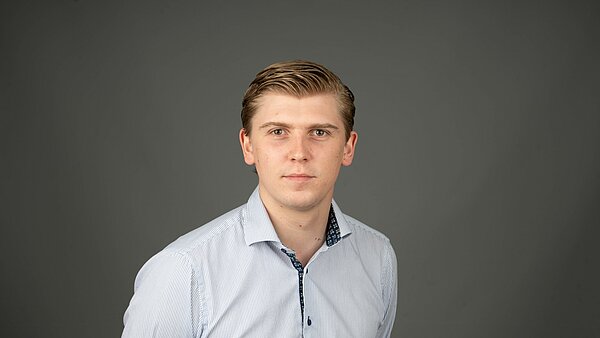
Provide insight in the way technology works
“An example is the inspection for cables,” Jeroen continues. “The AI algorithm detects whether cables have been incorporated deep enough into the products and have been installed in the correct order. In case of an error, an employee will receive the message: 'this is a fail'. Chances are he won't see where the mistake lies. Then it is very important that you add explainability to the model so that the technician understands what is wrong and why it was rejected. Our AI system creates a heat map so that technicians can see where the errors are so that they gain confidence in the model. They succeed because they see that quality is increasing.”
Creative work will be done by people
“People have a central position,” Quinten also emphasizes; “It is important that technicians embrace the technology, in the end no one knows such a process as well as the mechanic. AI only has added value when mechanics see the possibilities AI offers and use them fully. A Lights-out factory might sound a bit scary in that sense,” Jeroen continues; “but you only want to automate activities where you don't have to think outside the box. In this way, repetitive tasks will be automated, the creative tasks remain.”
Visual inspection pays off
“We started with visual inspection because we think that this will lead to the fastest results,” explains Jeroen. “And we see that our approach works. We know the so-called failure modes very well. Significantly fewer products are added to rework because AI is already significantly more consistent than the human eye. We are adjusting our strategy to the topics that we expect to make progress in. “
Different challenges when applying AI
“The challenges we face in applying AI primarily concern technology. The process of being able to make an inspection can easily take hundreds of hours. One of the biggest bottlenecks is that you need a lot of pictures of defects to train a model. However, we we are in the luxury position of not having that many defects. We have to overcome that. Another challenge is that we need people who can work with this new technology.”
Wide range of education for AI is necessary
“One of the biggest points of attention in becoming successful in AI as a region and country, in my opinion, lies in creating a wide range of training opportunities when it comes to educating and training specialists for the application of AI. Then, I mean training at all levels. What you now see is that AI specialists are being educated, especially at an academic level. We believe that you make huge progress when you educate people at all levels. We should look at the wide range of education, including secondary school students, senior vocational education and universities of applied sciences.”
Regional cooperation requires transparency
“Collaboration is desperately needed to accomplish these types of developments. There is a great need for applying AI in a high-tech region like Brainport Eindhoven. This also means that we face common challenges, such as structuring data properly. If we are transparent about what we encounter, we can tackle challenges more quickly. I think a lot of regional companies and organisations are working on the same thing right now. That is not efficient. AI will become a commodity over time, the challenge is in being able to apply it. I think innovation should be driven by research and knowledge institutes, public authorities should look at regulation and stimulating AI innovation by offering tax benefits to companies working on it and companies should focus on the implementation and practical side of it.”
Having cold feet when it comes to AI unnecessary
“What you see now is that many companies have not yet adopted AI. They have cold feet. If we were to go from fifty companies in the region to one hundred and fifty companies that apply AI, then developments would go ten times faster. My message to companies that are not yet working with AI would be don't be put it off. As Prodrive Technologies, we would like to contribute to accelerating the application of AI in the region and help companies with that.”