'The more knowledge we can disseminate, the better'
Interview with Roeland Fraters of VDL Nedcar, partner of Green Transport Delta-Electrification
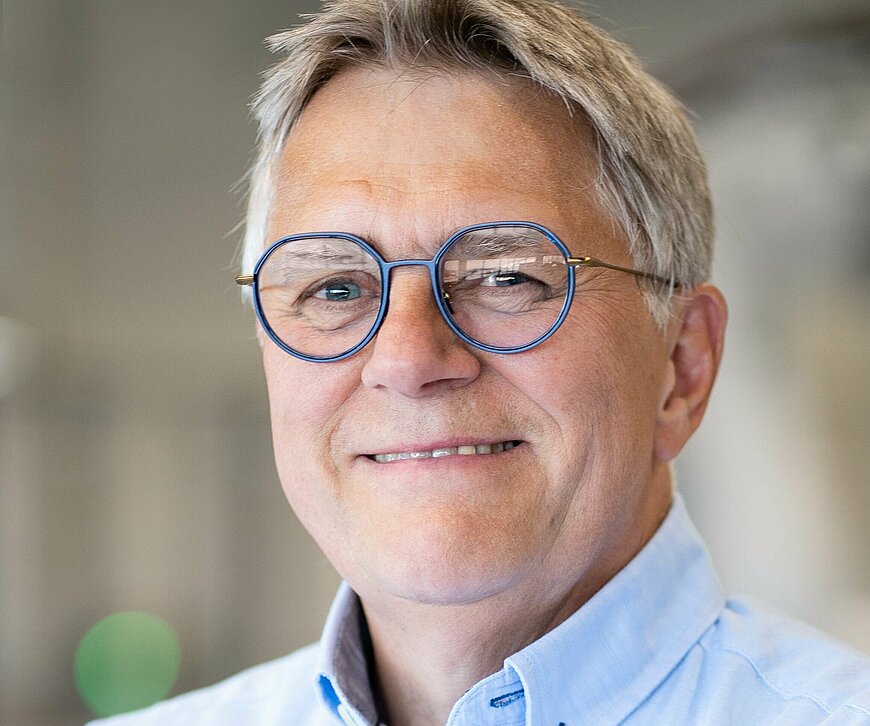
Please introduce yourself!
My name is Roeland Fraters. I have been working for Nedcar since 1985. I started at the Volvo division, where I held various positions. My previous department was responsible for all final assembly equipment. Since 2021, I have been managing VDL Nedcar's Battery Competence Team, which consists of four colleagues, all engineers with a lot of experience in process automation. It is great to jointly work on innovations.
I have seen lots of developments in passenger transport. Starting with the Volvo 300, then the 400, S40 and V40. Followed by the Mitsubishi Carisma, Outlander, Colt and the Spacestar. And not to forget, the Smart.
The Green Transport Delta-Electrification project started in 2021. I am project leader of work package two. On behalf of VDL Group, VDL Nedcar and VDL Steelweld take part in this work package. Jointly, we are realizing a flexible demo production line for assembly of various battery packs. This way, we help increase battery knowledge in the Dutch manufacturing industry to accelerate the transition to climate-neutral mobility.
VDL Nedcar receives requests to build cars. These days, we mainly receive requests for electric vehicles. It's great that we are also able to build battery packs for the brands concerned. We would never have been able to do that without the GTD-E project. We are just over a year in, and we have gained a lot more knowledge. By the way, we do not only build battery packs for cars, but we build them for all battery-driven applications used within, among others, freight transport, the maritime sector, or the construction industry. We cannot do this alone, that is why our partnerships with Airborne, ELEO, DAF, EST-Floattech, TU/e, NPS Driven, TNO, Maastricht University are so important.
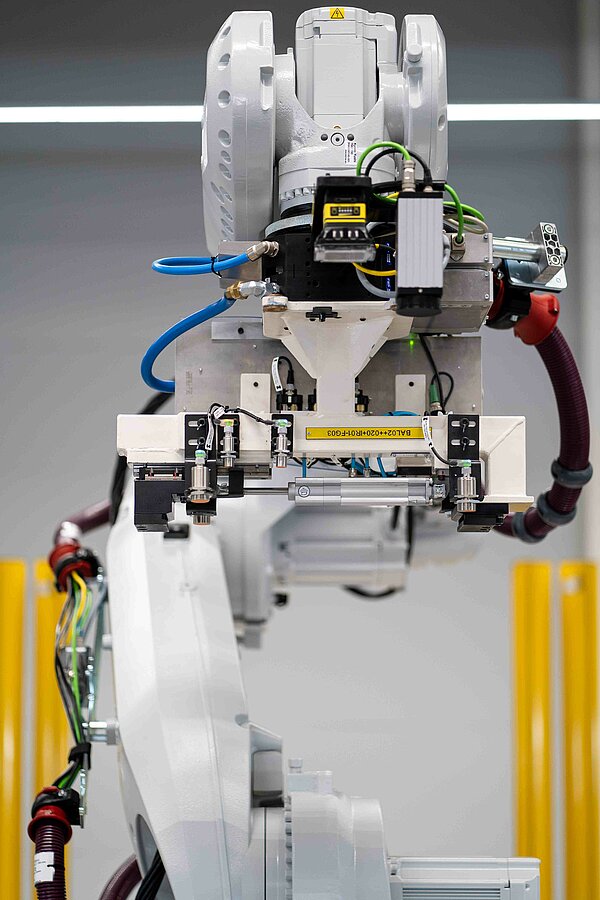
What is the objective of the Green Transport Delta-Electrification pillar you are working on?
The goal of the project is twofold; on the one hand, we want to increase knowledge on battery assembly in the Netherlands and work towards a semi-automated battery assembly line. On the other hand, we want to give our customers the opportunity to develop their battery concept into a product that is ready for regular production. VDL supports the automatic battery assembly line’s design for manufacturing principles and the design choices to allow for cost-efficient production of batteries. The first step is the demo line we have set up here at VDL Nedcar. This is a flexible and automated pilot production line for battery packs, which is accessible to everyone.
We have gained an enormous amount of knowledge in the area of battery packs and battery pack production. The collaboration between the various parties is also working very well. Each party has its own area of focus and expertise, and all areas are complementary to one another. ELEO has brought in a micro factory with battery modules especially for this project. DAF is working on a new battery pack and wants to develop a high-volume production line. EST Floattech has developed its own battery pack. Airborne is working with robotization. They have developed a program that allows for robots to learn things by scanning drawings. NPS Driven is working on a battery pack for the maritime sector. TU/e is adding logistics routes to the production line and Maastricht University is working with AI. And TNO is conducting research and providing auxiliary technical work.
At VDL Nedcar, we know a lot about assembly of parts. We can share that knowledge. For example, our people are helping our colleagues from EST and ELEO with the assembly of certain parts. We all work well together and the ultimately goal is that everyone within the work package will experience a win-win situation. Perhaps VDL can build battery packs for our partners for example, or VDL Steelweld can build the battery assembly lines. And our partners will gain knowledge via us. As a result, the level of knowledge throughout the Netherlands will be raised.
Why is it important to participate in this project?
Several VDL companies and many new partners are taking part in the GTD-E project. For example, Airborne in The Hague has wonderful technologies. We recently held our project meeting at their premises. That was fantastic and very inspiring. Also for everyone at VDL.
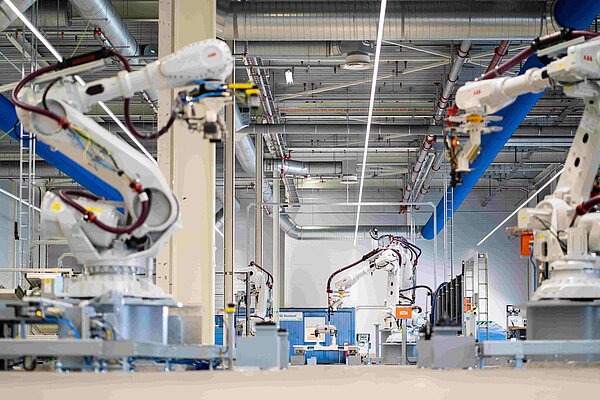
How will these innovations affect the Dutch citizens?
If we gain more general battery knowledge, we will all benefit. As a small country, we are still facing quite a few challenges and we still have to solve some problems. For instance, we have to increase the stability in the power grid. Using the right battery packs can help create that stability. All GTD’s projects have an impact. All work packages are working towards the energy transition. After this project, we will focus on the National Growth Fund and then we will take steps to further scale up our projects. When the projects grow, the national battery knowledge will grow accordingly. By involving knowledge institutions, we hope that schools will take up the developments. Connecting education to the developments in the market will help us get ready for the future.
VDL is in the process of launching the Mobility Innovation Center. One of the spearheads is the battery ecosystem. If we can make battery packs for third parties, employment will increase. By expanding our knowledge, smaller companies can also greatly benefit, making it easier for them to scale up production. I think you shouldn't start too big. That is why we are trying to establish a production line with a high level of flexibility for a relatively small volume, which can be easily scaled up. By growing slowly, you can often attract more customers.
We are operating in quite a difficult market. China is very competitive, and many car companies keep their battery assembly production lines in-house. Maybe that will change in the future. For instance, very few car manufacturers are still building their own seats nowadays. That part of the production process is being outsourced. Maybe battery pack production will also be outsourced in the future. Free storage of batteries is regarded as dangerous, and more requirements have to be met than when storing other components. If you can centralize battery storage by producing battery packs and storing them in large, specialized businesses, things will be easier for small companies.
What parties would you like to work with to achieve success and what are the topics people can contact you for?
Anyone active in the battery field is of interest to us. And we have a lot to offer, because we are working on a really great and important project. We are also working with VDL Bus & Coach, for example. They use very large battery packs with a stainless-steel casing. Airborne is one of our partners in GTD-E and they are making composite materials. Composite casings are much lighter and just as strong as the regular casings. Jointly with Airborne, we are doing a test to see if we can make a demo casing as part of the GTD project. At VDL, we will try to use the production line to both produce the composite casing and the battery pack. Creating a win-win situation for all parties.
The GTD project focuses on connecting all businesses that are working on battery development and battery pack production. Whether you are working on electric passenger transport, or battery packs for agricultural vehicles or the maritime sector; everyone is welcome to join. We can share knowledge about process engineering, and we can help you test your products. Say you have thought up three or four ideas for a battery pack. We can further develop those ideas and print them. Those printed parts can then be tested on our test line to see which idea works best. The test line has been especially set up for this purpose and can be used by everyone. Call me, so we can make an appointment. Because the more knowledge we can disseminate, the better.
Email: R.Fraters@vdlnedcar.nl
Mobile phone: +31 (0)6 51586172