VDL wants to set an example for making business premises more sustainable
During our series "Grid heroes - pioneering in solutions against grid congestion”, we let pioneers who are working on the energy transition have their say. In this edition: Arnold van Triest, who works as an energy coordinator at VDL Group which has the aim of making their 105 companies more sustainable.
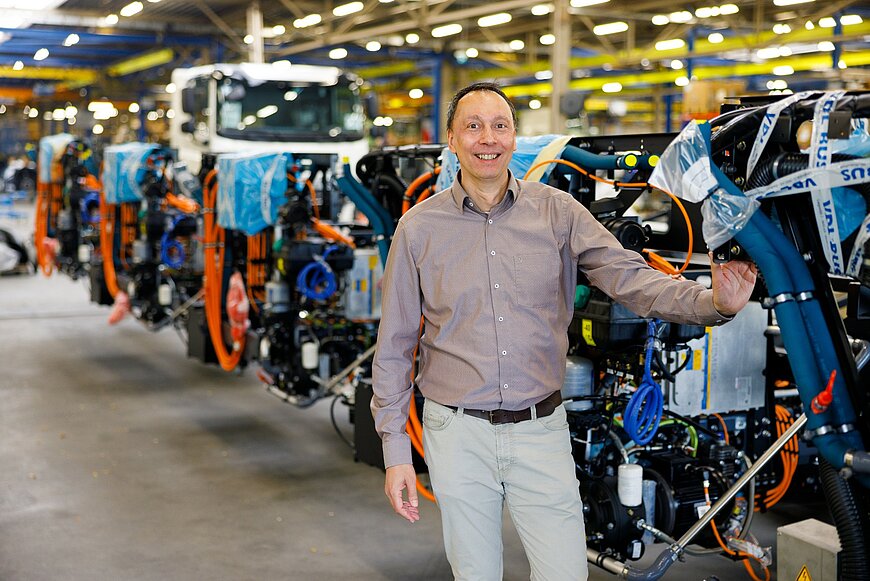
At the beginning of last month, Dutch energy grid manager Enexis warned that part of Southeast Brabant was turning 'yellow' on the demand map for electricity. This means that there is only limited capacity left to source more electricity. The energy transition, the desire for independence from Russian gas and the high gas prices are causing demand for electricity to soar. However, the limited feed-in is an even bigger problem, Van Triest points out. "Large parts of the Netherlands are on red alert, which means that it is not possible to feed electricity back into the grid."
VDL wants to use pilots to show that it can do both: relieve the strain on the grid as well as promote the energy transition, as the energy coordinator explains, who has been working for the Eindhoven family-owned company since 2019.
"Everyone wants to set up large energy parks in central locations now, but they generate so much energy that the grid becomes congested. So, there are bottlenecks in the grid. This is a problem throughout the Netherlands, but particularly in the Brainport region. If you are able to generate energy on location and use it yourself, you put far less strain on the grid." In the pilots, VDL is therefore focusing on local generation and local consumption of energy. Either independently or with the help of neighboring companies. The company then wants to use that energy in an efficient way itself.

Electric and thermal batteries
For example, Van Triest is working on a pilot together with VDL Apparatenbouw. This company will relocate to Hapert at the end of next summer into the building where VD Leegte Metaal is currently housed. "They will then move back to the Kempische Bedrijven Park," Van Triest goes on to explain. Apparatenbouw is a relatively small consumer with an energy consumption of approx. eight hundred MWh per year. The roof of the new building will be covered with around 3,500 solar panels, which will be able to generate enough energy. Yet the classic problem is also present here. The times when energy is generated and the times when energy is needed do not always line up with each other.
This is why Van Triest deploys a battery system. This system is supplemented with a thermal battery; a system based on volcanic rock. "We can heat that material up to five hundred degrees Celsius with the surplus energy we have from the summer months. We can then use that heat in the winter, because the rock is able to retain that heat for several months."
With this system, VDL Apparatenbouw can cover 95 percent of its electricity needs and 100 percent of its heating needs, which makes it virtually independent of the grid.
Cooperation with neighbors
VDL Parree is also relocating next year and is part of a pilot scheme. But that is more or less where the similarities end. The manufacturing process of the plastic injection molding factory releases a lot of heat. So, additional heat generation is unnecessary. On the other hand, the company does need 3,500,000 kWh of electricity on an annual basis. "We can't generate that amount on our own site; we have to do that together with nearby businesses and the surrounding area. One of those neighbors is a distribution center that itself uses a small amount of energy, but does have a huge roof packed with solar panels. We are going to see if their electricity surplus can be fed directly into our premises. It would be nice if we could also establish a link with a wind farm. But that is still at an exploratory stage."
From mobile to stationary uses
A deliberate choice was made for two companies with distinct profiles. "The intention behind this is to learn from them. In addition, it is also an opportunity to show the energy storage systems of VDL Energy Systems in actual practice.
VDL is a frontrunner in the electrification of heavy transport and transportation. Here, too, the use of batteries is important. The company is now looking to move from mobile battery applications to stationary applications. It is logical - and a must - that the company itself should also become sustainable on a large scale. “We don't just want to put products on the market, we want to use them ourselves. Moreover, this also provides us with some immediate benefits, as we are less dependent on the grid. Previously, these initiatives were unable to compete with the existing market. Now they can, thanks to the high energy prices. Moreover, the expectation is that the costs of these systems will continue to fall over the coming years."
Exchange of energy
As the energy grid is approaching its maximum capacity, the growth of economic activities is likely to be hampered. This is why it is important that solutions are found quickly, Van Triest believes. Some legislative changes are also needed for this. "The grid is currently not allowed to be used for the reciprocal exchange of energy, although that could provide a significant solution. We are now working out the technical details with a working group for the Kempisch Bedrijven Park, where VD Leegte Metaal will be located next year. VDL Fibertech is already located at the park as well.
VDL is not just carrying out all these pilots, innovations and ideas for its own benefit. Van Triest thinks that the initiatives can be a solution to the problems that are common across the whole country. "If we can demonstrate that we can reduce the load on the grid and promote the energy transition, then we will have a concept that can be implemented everywhere. That is in the interests of the entire energy transition."