Siemens Digital Software helpt innovatie versnellen
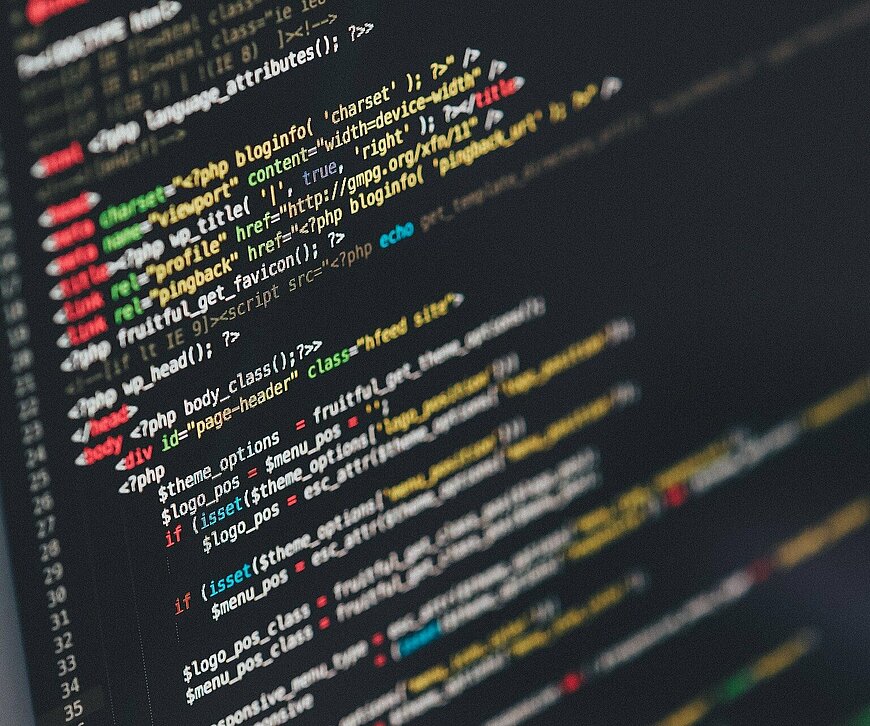
"Je kunt niet om digitalisering heen als je innovatie wil versnellen."
“Zie onze applicaties als de pen en het papier van engineers”, aan het woord is Piet van Dongen van Siemens Digital Software. Eind vorig jaar verhuisde Siemens Digital Software van Den Bosch naar Brainport Industries Campus. Het bedrijf ontwikkelt softwareoplossingen waar fabrikanten hun complete ontwerp- en productieproces mee kunnen verbeteren. Van idee tot productie, allemaal volledig gedigitaliseerd. En dat gaat niet slecht, want hiermee behoort Siemens wereldwijd tot de top tien van softwarebedrijven. “Voor engineers zijn deze digitale tools wat elektriciteit voor een fabriek is. Je kunt er niet omheen als je innovatie wil versnellen”, legt hij uit.
Siemens Digital Software nam met de verhuizing zo’n 150 man personeel mee. Volgens Van Dongen zitten ze hier nog dichter op waar het gebeurt: “In deze regio zitten niet alleen veel innovatieve bedrijven, maar hier op de campus wordt een omgeving gecreëerd waar innovatie de ruimte krijgt. Het is een energierijke omgeving waar samenwerkingen ontstaan vanuit allerlei bedrijven en disciplines. Hier op de campus hebben we bovendien alle ruimte om workshops, trainingen of andere evenementen te organiseren. Je hebt hier R&D, onderwijs en industrie, die combinatie is hier drijvend. Ook studenten worden vanuit de verschillende onderwijsinstellingen op BIC betrokken bij dit soort samenwerkingen.”
Een van die samenwerkingen op de campus is het High Tech Software Cluster. Hier werken bedrijven samen aan slimme producten, diensten en businessmodellen die ze met behulp van geavanceerde software ontwikkelen. Sinds kort is Siemens hier ook bij betrokken. Binnen dit fieldlab stelt het bedrijf verschillende tools beschikbaar voor bedrijven die betrokken zijn bij deze samenwerking. Software om productieprocessen digitaal te simuleren bijvoorbeeld. Maar het bedrijf ondersteunt ook onderwijsinstellingen en studententeams als InMotion en Solar Team Eindhoven met hun oplossingen. En ook bedrijven buiten het fieldlab kunnen er terecht om te zien wat mogelijk is.
Nieuwste software en technologie
Van Dongen: “Op de campus proberen we niet alleen potentiële klanten aan ons te binden. Hier worden de engineers van de toekomst opgeleid. We vinden het belangrijk dat studenten al tijdens hun opleiding de kans krijgen om te leren werken met de nieuwste software en technologie. Het zorgt voor een betere fit met het bedrijfsleven en een sterkere positie op de arbeidsmarkt voor de student. Wij zien dit als een investering voor de lange termijn.”
Steeds meer industriële processen zullen in de toekomst digitaal zijn, weet Van Dongen. Het begint al bij het idee dat in 3D wordt uitgewerkt. “Om innovatie te versnellen kun je niet om deze digitalisering heen. Het stelt engineers in staat niet alleen een idee uit te werken, maar ook digitaal te testen, simuleren en uiteindelijk te valideren of een idee ook werkt in de praktijk”, legt hij uit.
“Stel, ik ontwikkel een bottelmachine voor een bierbrouwer. Met een digital twin van de brouwerij kan ik mijn machine digitaal laten proefdraaien. Ik zie hierdoor meteen of deze aansluit op de rest van het proces. Als dat niet zo is, kan ik relatief goedkoop aanpassingen doen, zonder eerst fysieke prototypes te hoeven bouwen.”
Voorspellingen en preventief onderhoud
Ook als de bottelmachine eenmaal draait in de fabriek, monitort de software de performance van de machine. “Wat is de temperatuur? Wordt hij niet te warm? Wat is de conditie van bepaalde onderdelen? Via sensoren gekoppeld aan een Internet of Things platform (IoT) wordt de productie constant gemonitord. Door de verzamelde data te analyseren, kunnen producenten niet alleen hun productie optimaliseren. Maar kunnen ze ook voorspellingen doen over de staat van de machine en zo preventief onderhoud plegen.”
Volgens Van Dongen vergroot dit de ‘up-time’ van een fabriek. “Zo voorkom je dat de fabriek onnodig stil komt te liggen doordat onderdelen niet tijdig zijn vervangen. Dit principe wordt bijvoorbeeld ook al toegepast bij windparken op zee, waar het op tijd vervangen van bepaalde lagers, ergere schade voorkomt.”
Deze digitale manier van werken, of digital thread, zoals Van Dongen het noemt, heeft in de maakindustrie grote voordelen als de hele supply-chain is geïntegreerd. Neem Apple dat telefoons ontwikkelt, maar deze niet zelf produceert. Toeleveranciers krijgen hele specifieke instructies waar ze niet zomaar vanaf kunnen wijken. “Het verschil in toleranties is erg klein, alles moet precies in zo’n telefoontje passen. Door het hele proces te digitaliseren kun je de tijd die tussen een order en de aflevering van het product zitten – de doorlooptijd – verkorten en voorkom je fouten”, aldus Van Dongen.
Ervaring en kennis vergroten
Het van oorsprong Duitse bedrijf richtte zich in het verleden vooral op fabricage van hardware. Maar met de overname van UGS in 2007 kwam daar verandering in. Een Amerikaanse partij met een uitgebreid softwareportfolio gericht op het managen van de volledige productlevenscyclus. “Dit vormt nog steeds de backbone van Siemens Digital Software”, aldus Van Dongen.
Met verschillende overnames van succesvolle softwarebedrijven in de afgelopen jaren vergroot Siemens zijn kennis en ervaring binnen nieuwe domeinen. Het Rotterdamse Mendix, gespecialiseerd in low-code, is hiervan een recent voorbeeld. Van Dongen: “Een andere belangrijke toevoeging was LMS uit Leuven. Zij zijn gespecialiseerd in simulatie- en testoplossingen. Simulaties, digitaal testen en data-management worden steeds belangrijker in een productieomgeving. Al die tools willen we kunnen ontwikkelen en aanbieden aan klanten. Wil je innovatie blijven versnellen, dan kun je hierin niet achterblijven.”