Werken aan een blauwdruk voor de digitale fabriek van de toekomst
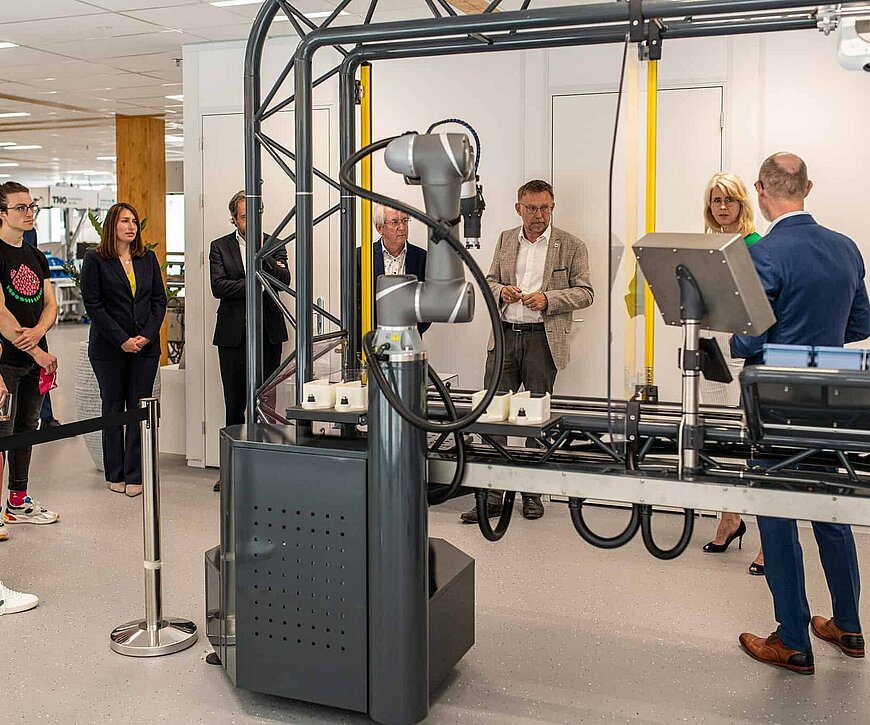
In dit fieldlab van Brainport Industries Campus werken maakbedrijven, solution providers en kennisinstellingen samen aan een omgeving die in de praktijk de voordelen van digitalisering laat zien.
De ‘Fabriek van de Toekomst’, met Brainport Industries Campus (BIC) als hoofdkwartier, kent negen aparte projecten, of fieldlabs. Eén daarvan is de ‘Digitale Fabriek’, geleid door Laurens Meijering van Brainport Industries. Doel van dit fieldlab is de omstandigheden te creëren waaronder de maakindustrie de slag kan maken naar volledig digitaal werken. Het integreren van data-gedreven innovaties vormt daar onderdeel van.
In het fieldlab werken maakbedrijven, solution providers en kennisinstellingen samen aan een omgeving die in de praktijk laat zien wat de voordelen en voorwaarden zijn van digitalisering. Er wordt geëxperimenteerd en er zijn experts die belangstellenden op weg kunnen helpen.
“Uiteindelijk draait het voor die bedrijven om productiviteitsverbetering”, zegt Laurens Meijering.
“Dat kan in de machine zijn, op de werkvloer of in de toeleveringsketen; digitalisering speelt op al die plekken een rol. Doel van de Digitale Fabriek is om dat proces zo toekomstvast mogelijk in te richten. Daarbij kijken we ook naar (internationale) open standaarden, want het is natuurlijk wel het beste als je er allemaal op dezelfde manier mee aan de slag gaat.”
Van digitale pleister naar blauwdruk
Waar in het verleden hier en daar een ‘digitale pleister’ werd geplakt is het volgens Meijering voor de toekomst van belang om tot blauwdrukken met daarbinnen digitale tools of apps te komen. “Daardoor kun je niet alleen binnen je organisatie beter communiceren, maar ook met partijen daarbuiten. Machines kunnen makkelijker interacteren en medewerkers hebben een gezamenlijk kennisfundament.”
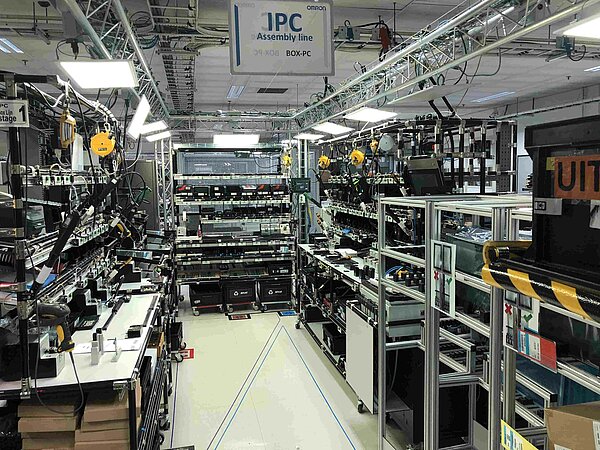
Maar zo’n blauwdruk is nog behoorlijk ingewikkeld, zeker ook omdat die op allerlei niveaus moet functioneren. “Datauitwisseling is overal. Voor een deel kan dat op bestaande standaarden, maar er zijn ook nog volop standaarden in ontwikkeling.” In de Digitale Fabriek wordt daar op drie manieren naar gekeken, zegt Meijering. “TNO, een van onze kennispartners, maakt een raamwerk met daarin alle standaarden. Soms zijn dat gewoon appjes, soms wat ingewikkeldere tools. Dit is de top-down benadering, de basis voor de blauwdruk. Ten tweede zijn er de initiatieven vanuit de bedrijven zelf, die hun eigen kennis inzetten en tot oplossingen komen gebaseerd op de blauwdruk. Het mooie is dat die oplossingen ook voor anderen geschikt zijn en dus vermarkt kunnen worden. Tenslotte is er het fieldlab hier in BIC, het experience center waarin je al die ontwikkelingen zelf kunt komen bekijken. Je kunt dan zelf zien wat er nodig is om zo’n gedigitaliseerde productielijn tot stand te brengen. We blijven dat intussen stap voor stap verder ontwikkelen.”
Mens en machine
Omron is een van de aangesloten maakbedrijven. R&D manager Tim Foreman ziet dat het mes voor hem aan twee kanten snijdt: “We helpen, als ‘solution provider’, met onze kennis mee aan de realisatie van de testomgeving, maar het is tegelijkertijd onze fabriek in Den Bosch die daar het eerste de vruchten van kan plukken.” Hij focust daarbij op een goede samenwerking tussen mens en machine. “Samen met TNO zijn we bezig de productielijn te herontwikkelen. Daarbij kijken we niet alleen naar machines, maar naar alles wat daarop van invloed is, dus ook de mensen. Machine-efficiency is maar één ding, algemene efficiency is het doel. Met TNO hebben we dit eerst geanalyseerd om vervolgens te zien hoe we de resultaten kunnen onderbrengen in TNO’s blauwdruk.”
Maar daar zijn meer partijen bij nodig, zeker ook in de categorie ‘solution providers’. Een daarvan is Itility, een IT en engineeringbedrijf uit Eindhoven. Managing consultant Geert Vorstermans voelde zich direct aangetrokken tot het project met Omron waarin techniek en data gecombineerd worden. “De ambitie is om voor de hele fabriek, met een twintigtal productielijnen, de Overall Resource Effectiveness (ORE) met 10 tot 15% te verbeteren. Dit door eerst klein te beginnen met het toetsen van de aanpak en blauwdruk op één machine en daarna uit te breiden naar de gehele productielijn. Daarbij kan zowel vanuit Omron als Itility gebruik gemaakt worden van technologie die nog niet te koop is, maar wel getest kan worden; een win-win voor beide bedrijven.”
Al snel bleek dat de succesformule. Vorstermans: “Een hele fabriek willen digitaliseren is te groot, dat werkt niet. Met alleen praten of afwachten kom je geen stap verder, je moet beginnen met iets kleins. Toen hebben we de blauwdruk erbij gepakt en zijn gaan kijken naar de technieken die ons zouden kunnen helpen. Wat werkt en wat niet? We kozen een productielijn, een machine en een industriestandaard voor onder andere de machine states, en toen zijn we gestart. Zo zijn we vanuit de blauwdruk alle bakjes in gaan vullen. Van daaruit kwam een van die ‘appjes’, zoals we ze noemen, die nu ook in de Digitale Fabriek te zien zijn.”
Grenzen
Niet alles lukt meteen, soms loop je tegen grenzen aan, zegt Foreman. “Sommige technieken zijn wel interessant maar niet functioneel voor ons doel. Soms is er een functionaliteit die ontbreekt en dan kan TNO die weer inbrengen in standaardisatiegroepen. Dat is de kracht: uitproberen, ergens tegenaan lopen en zo verder komen.”
Het concept ‘asset administration shell’ is zoiets. Je kunt er alle onderdelen van een productielijn mee digitaliseren. Van het kleinste schroefje tot de grootste machine. Op zich een prima concept, want theoretisch kun je zo de hele wereld digitaal opbouwen, compleet met materiaalpaspoorten enzovoorts.”
Maar het blijkt niet voor alles geschikt. “Zo hadden we hoge verwachtingen van een traject waarbij we in een asset administration shell ook de statusdata van de machine elke seconde – of sneller – wilden gaan opslaan. Maar dat bleek met de huidige stand van zaken niet echt haalbaar.”
Een soortgelijk idee voor de walsstraat bij Tata Steel werkte dan weer wel, vult Meijering aan. “Dat is een straat van honderden meters lang, met honderden walsrollen. Die slijten en moeten tijdig worden vervangen. Niet te vroeg en zeker niet te laat. Rond een groot aantal walsen zijn toen digitale schillen gebouwd; het is nog steeds giga, maar wel haalbaarder. Je hoeft in elk geval niet op de milliseconde te meten.”
Tot eind 2023
Het project Digitale Fabriek loopt minimaal nog tot eind 2023. “Maar deze ontwikkeling stopt natuurlijk nooit”, zegt Meijering er meteen bij. “Het kan altijd beter en slimmer. Maar dan wel zo eenduidig mogelijk, met de standaarden die daarbij horen. Ik heb niet de illusie dat ons project wereldwijd de standaarden gaat bepalen, hoogstens beïnvloeden, maar we proberen wel de ontwikkelingen op te pakken. En in de tussentijd zijn er zoveel bedrijven bij ons langs gekomen dat we daadwerkelijk een impact hebben kunnen maken voor de digitalisering van de maakindustrie.”
Ook interesse in de Digitale Fabriek? Meld je dan aan bij projectleider Laurens Meijering.
Meld je aan