“3D-printen van metaal niet verheerlijken, maar kritisch kijken waar toegevoegde waarde zit”
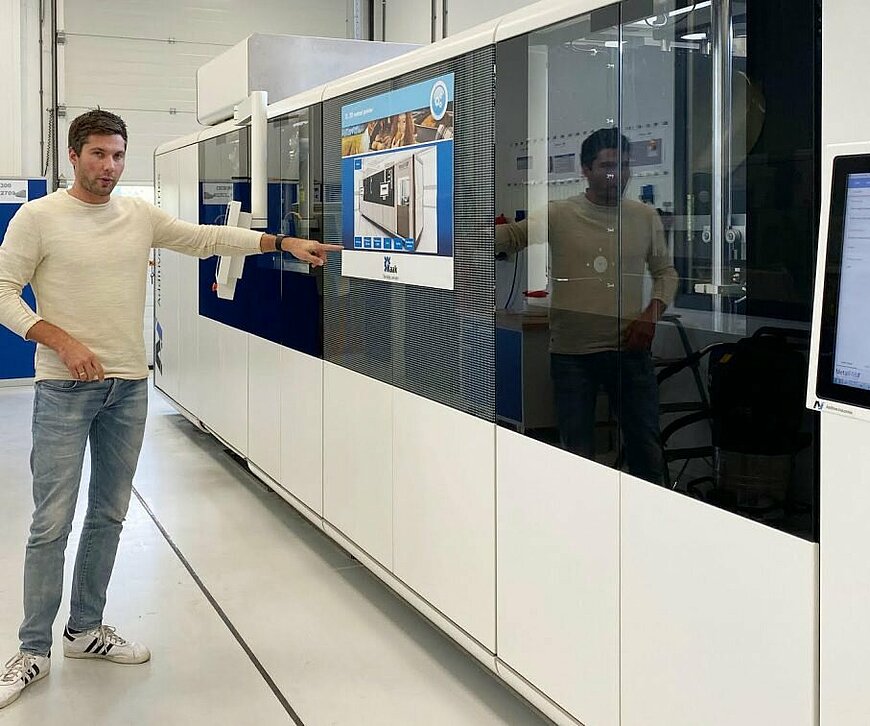
Luuk Wissink van K3D werkt op de Brainport Industries Campus aan het innovatieprogramma K3D-AddFab. Ze helpen hier bedrijven met ontwerp, productie en toepassing van de 3D-metaalprinttechniek.
Een constant gezoem klinkt, de ruimte voor een groot deel gevuld met een rechthoekig apparaat. Door een klein raampje in diezelfde machine zie je vonken oplichten. “Dat zijn lasers die het metaalpoeder in de juiste geometrie aan elkaar smelten”, vertelt Luuk Wissink van K3D wijzend naar de MetalFab1, een grote 3D-metaalprinter van het Eindhovense Additive Industries. De vonken stoppen en een soort automatisch bewegende arm legt een nieuw laagje poeder neer. “Deze recoater legt via een fijnmazig systeem een heel dun laagje op het poederbed. Dan zakt de bouwplaat en de lasers kunnen hun werk weer doen. Met de huidige instelling moet de printer wel twintig van die laagjes op elkaar laseren om 1 millimeter omhoog te gaan”, legt hij uit.
Wissink houdt een 3D-geprint mes omhoog uit de bakkersfabriek van Kaak Group, het bedrijf waaruit K3D is ontstaan. “Omdat de laagjes zo dun zijn, kunnen we het materiaal met een zeer fijne structuur opbouwen. Hierdoor kunnen we materiaaleigenschappen beïnvloeden”, Wissink laat zijn hand over het mesblad gaan, het zit vol minuscule gaatjes waar lucht doorheen geblazen kan worden. “Het mesblad is poreus. Via het luchtkanaal wordt lucht door het handvat naar de poreuze poriën getransporteerd. Door deze luchtstroom blijft er geen deeg aan het mes kleven tijdens het snijden.” Met het ontwerp van het mes won K3D in 2019 de Additive World Design for AM Challenge.


Dit is slechts een enkel voorbeeld van de voordelen van metaal geprinte producten of onderdelen. “Je kunt allerlei werkende onderdelen zoals schroefdraad, of scharnieren in één keer printen zonder dat hier allerlei extra stappen of nabewerkingen in de productie nodig zijn”, somt Wissink op.
Parameters aanpassen en bepalen aan welke eisen een product moet voldoen
Op de Brainport Industries Campus werkt K3D binnen het innovatieprogramma K3D-AddFab samen met partners van het eerste uur als KMWE, NTS, De Valk, Brainport Industries, Additive Industries en Summa College aan manieren om de 3D-metaalprinttechniek verder te brengen. “In de printer kun je zo’n honderdtwintig verschillende parameters aanpassen. Vergelijk het maar met een equalizer als je muziek afspeelt op je laptop. Iedereen vindt weer net een andere instelling mooier klinken. Zo is dat voor eindklanten ook, alleen gaat het dan om de eigenschappen van het product. Voor de ene toepassing is een gladde afwerking erg belangrijk, voor de andere klant is sterkte en lichtgewicht heel interessant. In de luchtvaart bijvoorbeeld. K3D en K3D-AddFab werken nauw samen met de eindklant. We willen hun problemen doorgronden. Per industrie proberen we tot een soort standaard te komen en te bepalen aan welke eisen en kwaliteiten een onderdeel moet voldoen.”
“Zo glad als een spiegel of toch lichtgewicht en sterk? Samen met de eindklant proberen we hun problemen te doorgronden om tot de beste eigenschappen voor een product te komen.”
Luuk Wissink
Zulke standaarden of keurmerken zorgen volgens Wissink niet alleen voor duidelijkheid, maar het wekt ook vertrouwen bij partijen die nog niet bekend zijn met 3D-printen van metaal. “Er staan in Nederland meer printers dan er vraag naar producten is, er is overcapaciteit. Door kennis en ervaringen te delen, willen we hier de markt bekend maken met de techniek. Dat doen we niet alleen in Eindhoven, maar ook in Terborg. Door open samenwerking proberen we bedrijven laagdrempelig kennis te laten maken met ontwerp, productie en de toepassing voor het printen van metaal in 3D.”
Kritisch blijven kijken naar toegevoegde waarde
Op de campus kunnen bedrijven terecht om de mogelijkheden en voordelen van metalen onderdelen uit een printer te bekijken. “Natuurlijk laten we hier veel voorbeelden zien om bedrijven een beeld te geven wat er allemaal mogelijk is. Maar we willen niet doen alsof 3D-printen voor alles een oplossing is. Ik zie sommige engineers die net van een opleiding doorstromen de techniek wel eens verheerlijken. Zonde. We moeten nog steeds kritisch kijken waar het van toegevoegde waarde kan zijn. Hoe breng je het naar de markt? Hoe kun je het in bestaande processen inpassen? Blijft het betaalbaar? Het is een relatief nieuwe techniek, grote bedrijven als ASML zijn nieuwsgierig. Maar ze willen zekerheid, als het op wat voor manier dan ook tegen blijkt te vallen, gaat er meteen een streep door 3D-printen. Maar we zien beweging in de markt, steeds meer bedrijven komen terug na een eerste prototype.”
“3D-printen is geen oplossing voor alles. Sommige engineers verheerlijken de techniek. We moeten nog steeds kritisch blijven kijken waar het van toegevoegde waarde kan zijn.”
Luuk Wissink
Om dit te voorkomen gaan Wissink en zijn team al vroeg met partijen in gesprek. Niet alleen om de techniek en de mogelijkheden ervan aan de man te brengen, maar ook door engineers actief mee te laten denken. “Om de kennis rond het 3D-printen van metaal te vergroten, geven we gastcolleges op opleidingen en workshops aan bedrijven. Het is belangrijk dat bedrijven de techniek omarmen waar het zin heeft. Dus als het niet kan zeggen we dat ook. Het gaat vaak om complexe producten daarom betrekken we hier de engineers met kennis van het eindproject altijd bij. Zij kunnen de vinger op de zere plek leggen en de bal terugkaatsen. Die gesprekken zijn ontzettend belangrijk om tot een goed geprint onderdeel of product te komen.”
Openstaan voor ideeën van anderen
Ook binnen K3D staat de deur van Wissink altijd open om van anderen te horen waar het beter kan. Wissink: “We hebben een jong team van zes man, de jongste is 26 en komt net van zijn studie werktuigbouwkunde en de oudste is 35. Ik vind het belangrijk dat iedereen zich gewaardeerd voelt, veel besluiten nemen we gezamenlijk. Het is een nieuwe markt die we met zijn allen vorm moeten geven.”
Wissink wijst door het glas in de richting van de onderwijsinstellingen op de campus. “Studenten kunnen hier letterlijk naar binnen kijken en zien waar we mee bezig zijn. Ze kunnen hier komen zitten om te werken en we helpen ze graag als ze vragen hebben. We hebben regelmatig stagiaires en laten ze veel nieuwe dingen doen en leren, het is belangrijk dat zij de kans krijgen zich te ontplooien. Ook zij maken straks die markt.”
Op dit moment werken er studenten van Fontys en Summa aan een manier om een geprint product sneller en makkelijker van een bouwplaat af te halen. “Als de producten uit de printer komen gaan deze naar een bandzaagmachine. Deze zaagt de producten van de basisplaat waarop wordt geprint. Zo’n plaat weegt toch al gauw 60 kilo en wordt nu op een wagentje geladen. Wij hebben hen de opdracht gegeven om met een innovatieve oplossing te komen die dit proces kan verbeteren. Ook blijft er best wat metaalpoeder achter dat misschien wel opnieuw gebruikt kan worden als we dit geautomatiseerd opvangen, hier laten we studenten ook naar kijken.”
“Iedereen moet zich gewaardeerd voelen van starters tot ervaren engineers. Maar ook stagiares die het vak nog moeten leren. Het is een nieuwe markt die we met zijn allen vorm moeten geven.”
Luuk Wissink