Producent van batterijpakketten ELEO grijpt de kansen die 3D printtechnologie biedt

Voor batterijfabriek ELEO is 3D-printen de normaalste zaak van de wereld. Het is een onlosmakelijk onderdeel van het productieproces
Scale-up ELEO zet 3D-printen nadrukkelijk in om zijn ontwikkelproces te versnellen. De spin-off van de TU Eindhoven ontwikkelt batterijsystemen voor onder meer grote graafmachines in de bouw maar ook voor kleinere logistieke voertuigen in magazijnen.
Al sinds de start als studententeam STORM, 2014, gebruikt het bedrijf 3D-printers, zegt Jules Frints, product developer bij ELEO. Toen kreeg het team een printer gesponsord van het 3D-printbedrijf, Lay3rs uit Brainport Eindhoven, waar zijn collega en vriend Stephan van der Burgh werkte. De twee zijn 3D-specialist binnen het bedrijf.
Frints: “In het begin vroegen we ons nog wel af of we daar echt zo veel mee zouden gaan doen. Maar we raakten zo enthousiast dat we er op een gegeven moment zelf een hebben gekocht. En die werd weer vervangen door een betere versie. Nu hebben we er twee staan.”
In 2016 reed het studententeam op een zelfgemaakte elektrische motorfiets in tachtig dagen de wereld rond. De motorfiets diende als showcase om de wereld te laten zien dat het overal mogelijk is om elektrisch te rijden, aldus mede-oprichter Bas Verkaik in een eerder interview met IO.
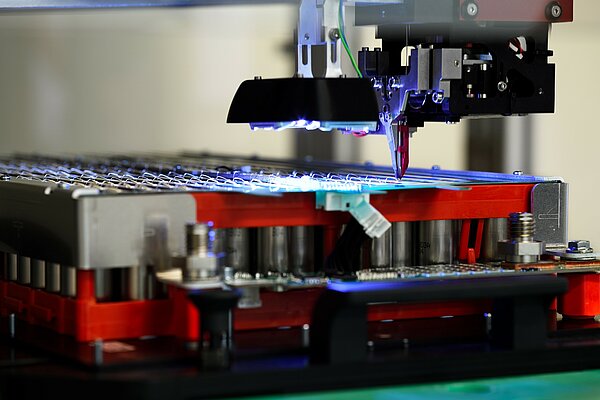
Nu ontwikkelt ELEO modulaire batterijsystemen die de klant in de eigen voertuigen kan gebruiken. Een pakket bestaat uit verschillende modules en een controller. Frints: “We kunnen het helemaal op maat ontwikkelen. Afhankelijk van de eisen aan voltages, capaciteiten en volume van de klant bestaat een pakket uit een of meerdere modules.” Het bedrijf is gevestigd op de Automotive Campus in Helmond.
3D-printen is voor ELEO geen doel op zich, gaat Frints verder. “In de ontwikkelfase is het heel handig om snel onderdelen te kunnen prototypen.” Onderdelen die in een later stadium met spuitgieten worden gemaakt. Die techniek heeft een veel langere doorlooptijd dan 3D-printen. “Je hebt er een mal voor nodig. Die is vrij duur om te maken. Je wilt die mal het liefst in een keer goed krijgen. En dan moeten de producten nog gemaakt worden. Daar kan wel een paar maanden overheen gaan.”
Ook ben je niet afhankelijk van een derde partij en kun je snel iets maken om te testen, stelt Frints. “Het is fijn om in een vroege fase al een product in je handen te hebben. Het hoeft dan nog niet in een keer goed te zijn. Je kan snel in een vrije vorm iets fabriceren en die vervolgens gaan finetunen.”
Natuurlijk is het dan niet van dezelfde nauwkeurigheid of stijfheid als het uiteindelijke materiaal. Dat is bij sommige testen ook niet nodig, aldus Frints. Bijvoorbeeld om te kijken hoe gevoelig een ontwerp is voor elektromagnetische straling. “Daarbij maakt het niet uit of ik een 3D-print gebruik of een plastic spuitgegoten onderdeel. Bij brandveiligheid, trillings- en shocktesten zijn nauwkeurigheid en materiaal wel weer belangrijk.”
De 3D-printer is helemaal verweven in het productieproces van het bedrijf, voor prototyping en tooling. “Voor ons is het heel normaal om van een idee snel een 3D-print te maken. Deze week gebeurde het nog. We moesten verschillende onderdelen assembleren en hebben daar snel een malletje voor geprint. Gewoon om de componenten op hun plek te leggen.”

Soms kan het zijn dat een 3D-geprint onderdeel in de productielijn blijft zitten. “Daarbij gaat het nooit om grote aantallen. Maar soms printen we een onderdeel voor een klant, bijvoorbeeld om kabels bij elkaar te houden, en dat blijft er dan vervolgens inzitten.”
ELEO print niet alle onderdelen zelf. “Het hangt van de functie en benodigde nauwkeurigheid af of we een print uitbesteden.” Het bedrijf beschikt over een FDM-printer en een SLA-printer. Zijn er andere printers nodig dan besteedt Frints die opdracht uit.
“Een Multi Jet Fusion printer print bijvoorbeeld met een soort nylon. Daarmee zijn mooiere en nauwkeurigere producten te maken dan wij met onze printers kunnen. Ook hangt het van de geometrie van een onderdeel af. Is de vorm te complex, ook dan hebben we een bedrijf dat dat voor ons print.” Kleine sterke en grote grove onderdelen print Frints zelf.
Frints werkt nu aan de prototypes van de nieuwe generatie batterijen, die het bedrijf later dit jaar lanceert. Daarvoor is de geprinte testversie van een zogenoemde cell spacer vervangen door een variant uit een stalen spuitgietmal. “Daar kunnen een paar honderdduizend producten uitkomen.”