Nooit zonder perslucht in een fabriek dankzij digitalisering
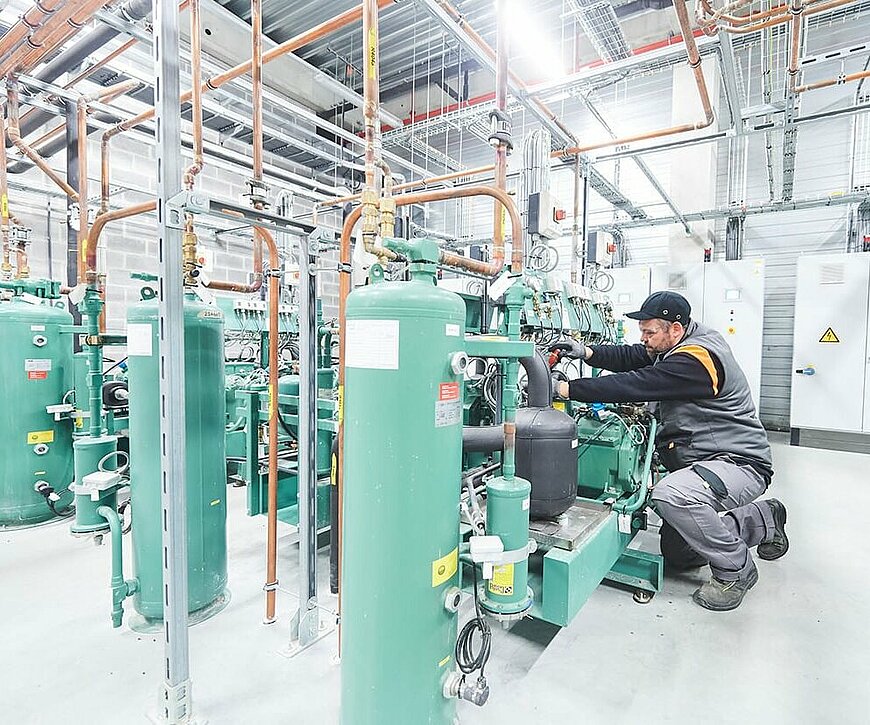
In het innovatieprogramma Digitale Fabriek onderzoekt ENGIE voorspellende algoritmen waarmee bedrijven op BIC nooit zonder perslucht, koelwater of andere gassen of vloeistoffen komen te zitten.
Het is voor Nederlanders zo normaal dat we er eigenlijk niet eens meer over nadenken: water, stroom en warmte. Maar achter deze ‘vanzelfsprekendheden’ gaat vaak veel meer schuil dan we denken. Zeker in high tech productieomgevingen zoals op Brainport Industries Campus waar bedrijven complexe producten produceren. Een afwijking in bijvoorbeeld de waterdruk of een afwijking in de klimaatcondities in een cleanroom, kunnen hier voor problemen zorgen.
Om aan te tonen dat producten of onderdelen onder de juiste omstandigheden zijn geproduceerd, moeten de producenten vaak certificaten opstellen. Op de campus kloppen ze hiervoor aan bij ENGIE. Dit bedrijf levert naast water, stroom en warmte ook perslucht, gedemineraliseerd water en allerlei andere gassen of vloeistoffen.
Jeroen van Schilt is bij ENGIE verantwoordelijk voor de automatisering van bedrijfs- en productieprocessen in Zuid-Nederland. Binnen het project Digitale Fabriek werkt het bedrijf samen met andere bedrijven en kennisinstellingen aan onder andere een manier om deze kwaliteitscertificaten te automatiseren. Van Schilt: “Als een producent een belangrijk onderdeel doorstuurt naar de volgende partij in de waardeketen, moet die er zeker van zijn dat dit onder de juiste omstandigheden is gebeurd. Was het koelwater op de juiste temperatuur of druk? Is het juiste gas gebruikt? Allemaal zaken die van invloed kunnen zijn op de kwaliteit van een product.”
Handmatig klusje
Nu is het opstellen van zo’n certificaat handmatig werk. Een tijdrovende klus waar verschillende gegevens over een bepaalde periode bij elkaar gezocht moeten worden. “Ook moeten er vaak onafhankelijke partijen aan te pas komen om de echtheid van deze data te waarborgen”, aldus Van Schilt.
Dat moet anders kunnen, was zijn gedachte. “Wat nu als producenten met één druk op de knop een certificaat kunnen uitdraaien, waarmee ze aantonen dat hun onderdeel of product onder de juiste omstandigheden is geproduceerd? Veel van die data hebben we zelf, maar voor zo’n certificaat kun je ook machinegegevens nodig hebben bijvoorbeeld. We zijn nu bezig om al die verschillende datastromen bij elkaar te krijgen en te bundelen in de cloud. Samen met TNO en de betrokken bedrijven werken we nu aan een soort watermerk om aan te tonen dat deze gegevens niet zijn gemanipuleerd. Dat ze echt zijn.”
Waar een stijging van een paar tienden veel verschil maakt
Met de gegevens die binnenkomen kan al veel gedaan worden, zo verzekert Van Schilt, maar om echt nauwkeurig te checken hoe het met hun diensten gesteld is, moeten er soms ook meer sensoren komen. “Om de kwaliteit zeker te stellen is het uiteindelijk de bedoeling dat op ieder punt zowel de opwekking als de afname wordt gemeten.”
Zo kan het koelwater bij de koelopwekkers op de campus van temperatuur verschillen met wanneer het wordt afgenomen bij een bedrijf. Van Schilt: “Door een verstorende warmtebron dichtbij de koelleiding bijvoorbeeld. In een hightechomgeving maakt die stijging van een paar tienden ontzettend veel verschil. Door meer te monitoren kunnen we betere kwaliteit leveren. Ook stelt het ons in staat om te voorspellen wanneer onze systemen onderhoud nodig hebben. Aan dit soort voorspellende algoritmen werken studenten van Fontys en de TU/e op dit moment. Het gaat ervoor zorgen dat we altijd de kwaliteit leveren die we hebben afgesproken met de huurders.”
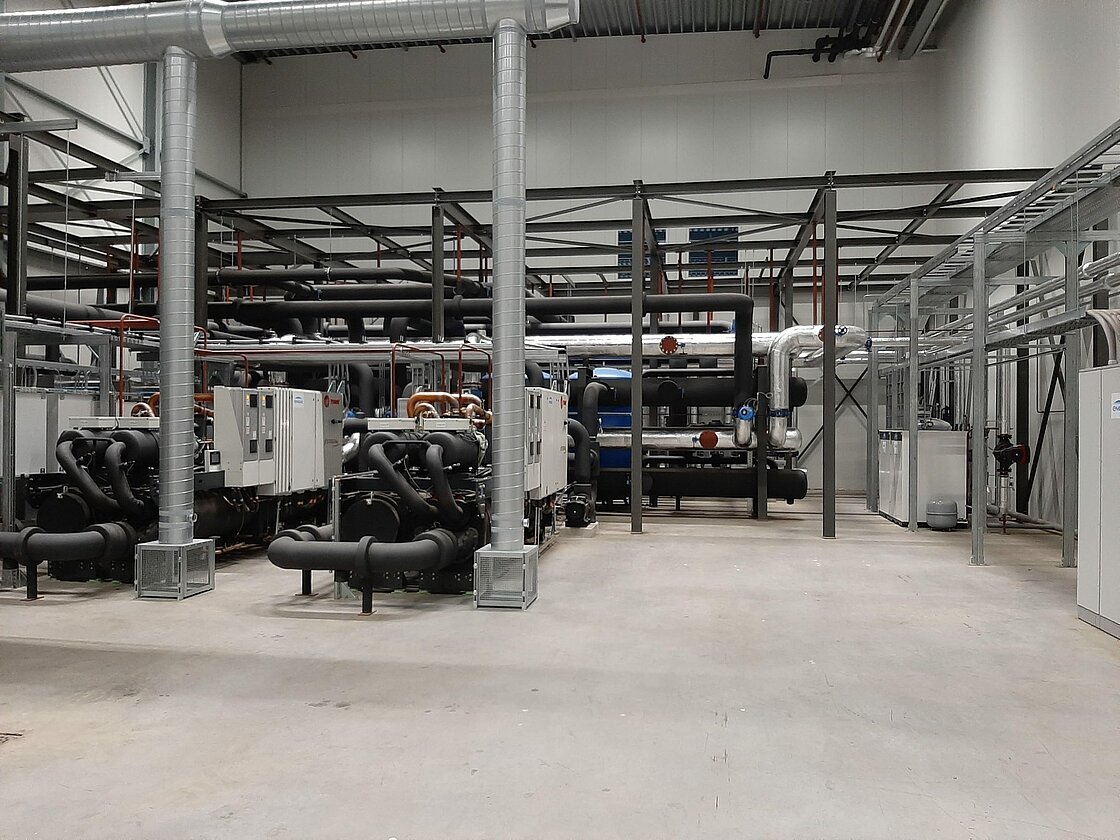
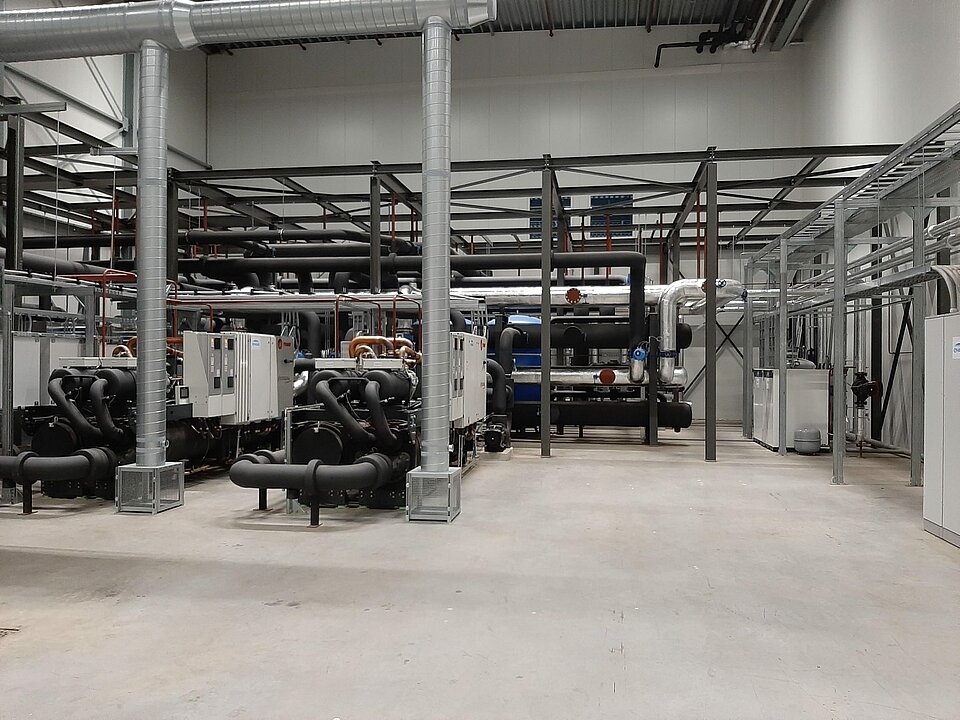
Automatische communicatie en verbonden systemen
Het doel van de Digitale Fabriek is een verbonden productieproces waar verschillende schakels in de waardeketen automatisch gegevens uitwisselen om het productieproces te verbeteren. Daarom werkt ENGIE aan een voorspellend algoritme dat rekening houdt met de toekomstige capaciteitsvraag door middel van de planning en productie van andere bedrijven. Leo van der Linden is namens ENGIE verantwoordelijk voor BIC. Hij legt uit waarom afstemming belangrijk is en hoe digitalisatie hierbij kan helpen. “In een drukke periode verbruikte een van de bedrijven meer demiwater dan was afgesproken, het ging zelfs zo ver dat het complete buffervat werd leeggetrokken. Er was niet tegenop te produceren voor ons. Toen zijn we in gesprek gegaan: vergroten we onze installatie? Of gaan jullie minder afnemen?”
Maar met communicerende systemen was zo’n gesprek niet nodig geweest, geeft Van der Linden aan. “Als we zicht hebben op de productieplanning van de verschillende bedrijven kunnen we hier automatisch rekening mee houden en actie ondernemen. Stel dat een bedrijf de komende tijd 4 extra machines aansluit, wat voor gevolgen heeft dit dan? Door onze eigen gegevens te koppelen met de gegevens van fabrieken, kunnen we hier voorspellingen op maken. Ook hier werken we nauw samen met TNO en de TU/e.”
Volgens Van der Linden en Van Schilt zijn dit soort voorspellende algoritmen onmisbaar op BIC. “Bedrijven die zich hier vestigen zijn in volle groei. Flexibiliteit en schaalbaarheid zijn hierbij belangrijke begrippen. Door alle verschillende datastromen bij elkaar te voegen, kun je rekening houden met deze groei. Binnen het Digitale Fabriek-project zoeken we uit welke gegevens we hier allemaal voor nodig hebben.”
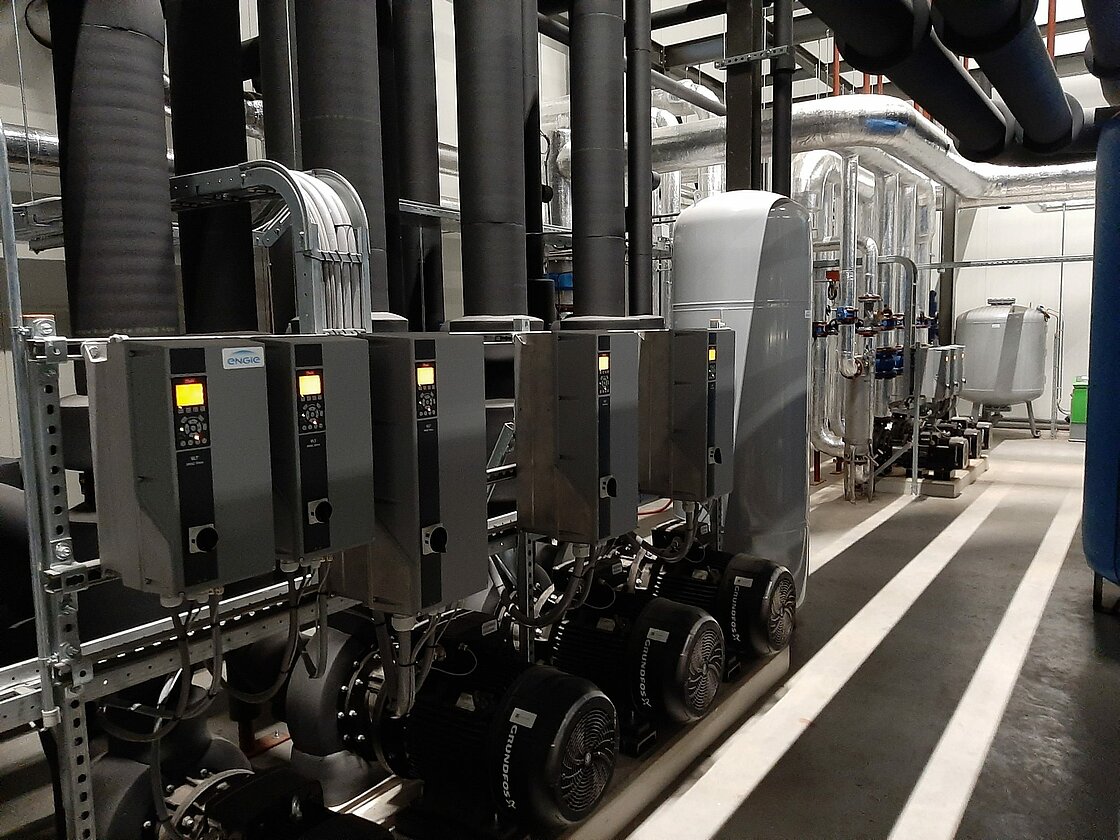
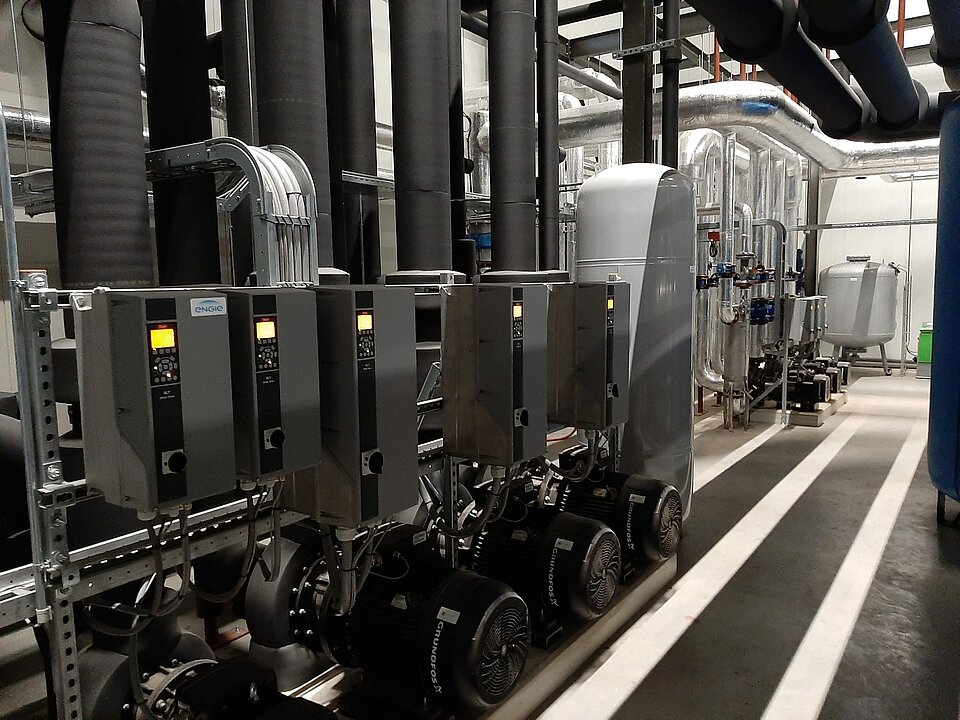