About ASML
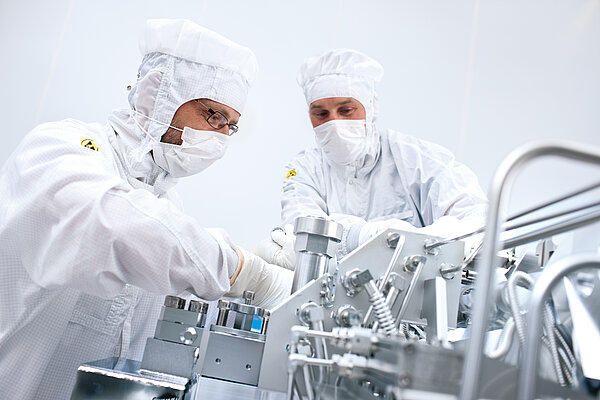
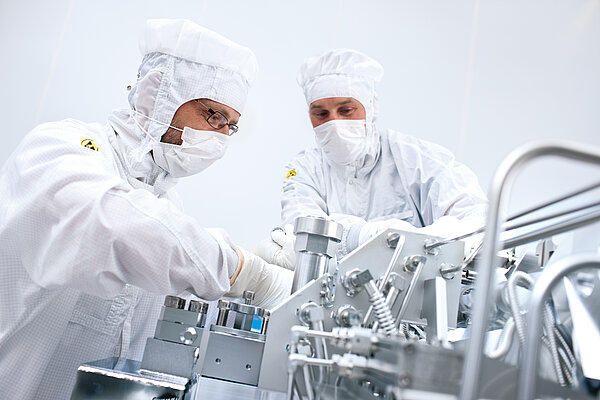
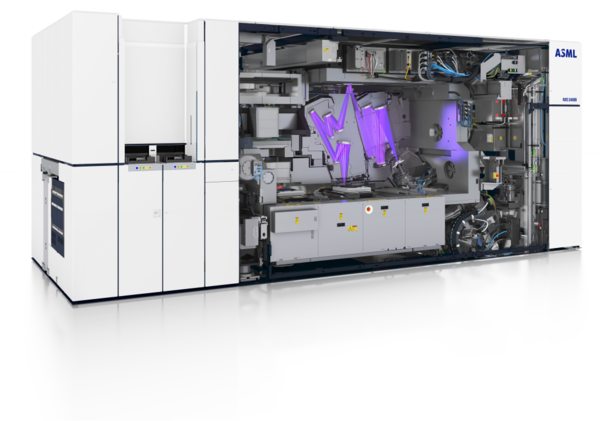
Extreme Ultraviolet (EUV) lithography – ever more powerful chips
Extreme Ultraviolet (EUV) lithography is on the cusp on being introduced in volume chip manufacturing. ASML’s lithography systems use ultraviolet light to create billions of tiny structures on thin slices of silicon. Together, these structures make up an integrated circuit, or chip. The more structures that chipmakers can cram on a chip, the faster and more powerful it is. That’s why ASML’s systems focus on making such structures smaller and smaller. With Extreme Ultraviolet (EUV) lithography, ASML does just that by harnessing light of a much shorter wavelength (13.5 nanometer light) than with previous lithography machines (193 nanometer light). This cutting-edge EUV lithography system enables ASML’s customers to create smaller, faster and more powerful chips.
EUV light essential for chip production
A lithography system essentially is a projection system. Light is projected through a blueprint of the pattern that will be printed (known as a ‘mask’). Optics focus the pattern onto the silicon wafer, which has earlier been coated with a light-sensitive chemical. When the unexposed parts are etched away, the pattern is revealed. The tricky thing with EUV light is that it’s absorbed by everything, even air. That’s why an EUV system has a large high-vacuum chamber in which the light can travel far enough to land on the wafer. The light is guided by a series of ultra-reflective mirrors, made by ASML’s German partner Carl Zeiss. But EUV light is also notoriously hard to generate. An EUV system uses a high-energy laser that fires on a microscopic droplet of molten tin and turns it into plasma, emitting EUV light, which then is focused into a beam.
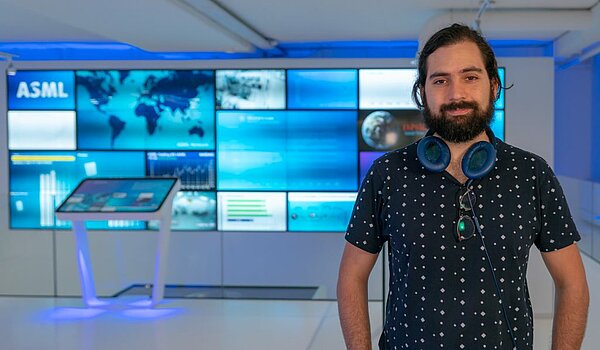
Talent
Discover completely new things every day
Diego Alvarez is a Mechanical Engineer at ASML. He works on tin droplets that help generate extreme ultraviolet light which is needed to print tiny features on chips. What Diego does is create solutions that prevent the tin from causing contamination in other parts of the lithography machine. Both the conditions as the machine are extreme. What Diego and his colleagues work on is not described in any book. They discover completely new things every day and literally are part of progress.
Generating EUV plasma
“In our EUV, or extreme ultraviolet lithography machine, we use extreme ultraviolet light to print tiny features on chips, Diego explains. “This light is generated with help of tin droplets. A laser shoots at these tin droplets, which essentially causes them to explode, generating EUV plasma. (This happens at an amazing speed of 50,000 times per second.)”
Preventing contamination
“My job is to create solutions that make sure that the tin isn’t getting into the scanner part of the machine because when the scanner mirrors are contaminated, the machine will not be able to print the features on the chip.”
Everything about this machine is extreme
“Everything about this machine is extreme, including the conditions inside the machine. Because of the high temperatures, we need to come up with solutions that can survive at 700 degrees Celsius for 7 years in a row. And another challenge for us: tin degrades other metals, so it means we need to make our designs with specific materials that are hardly applied in any other industry.
We discover new thing every time
“In my job, there is always a new technical question to solve. For example, nobody really knows how the light source behaves. It’s not in books; it’s not on the internet. So our research colleagues experiment in the labs and discover new things every time. In our group of engineers, we need to constantly adapt based on the new knowledge that we create.”
Very dynamic and thriving company
“I think the multicultural environment at ASML is very enriching. It opens your mind about how other people work, live and express themselves. When you walk around, you feel the vibe – it’s a very dynamic and thriving company.”
Welcome to challenge the ideas of others
“At ASML, we put quality first. We always deliver the best we can for our customers. So people here are open to all opinions. If you have a good idea, you can make yourself heard. You are also welcome to challenge others’ ideas. This really helps to avoid tunnel vision. It forces you to take a second look, to always improve. That’s what I love about working at ASML.”
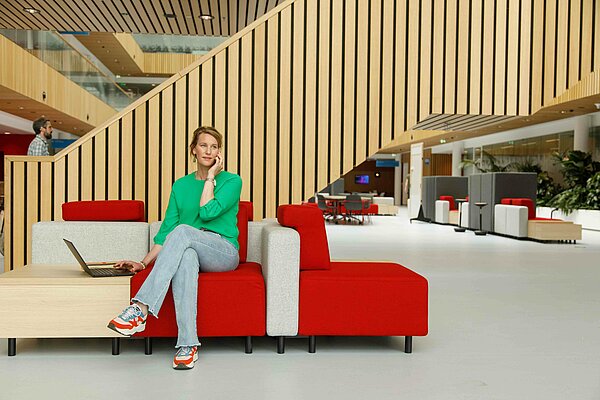
Societal impact
Hard to imagine a world without microchips
It is hard to imagine the world without microchips. They are at the heart of the devices that we use to work, travel, stay healthy and be entertained – from smartphones to cars, from MRI scanners to industrial robots. Delivering new functionalities, better performance and lower cost with each generation, advances in chips have spawned new products and transformed industries. New technologies and trends, such as artificial intelligence, augmented reality and the Internet of Things, result in additional demand for semiconductor chips to generate, transfer, store, analyze and apply vast amounts of data.
Semiconductors help solving society’s toughest
ASML is one of the world’s leading manufacturers of chip-making equipment. ASML’s vision is a world in which semiconductor technology is everywhere and helps to tackle society’s toughest challenges. ASML contributes to this goal by creating products and services that let chipmakers define the patterns that integrated circuits are made of. The company continuously raises the capabilities of its products, enabling its customers to increase the value and reduce the cost of chips. By helping to make chips cheaper and more powerful, ASML helps to make semiconductor technology more attractive for a larger range of products and services, which in turn enables progress in fields such as healthcare, energy, mobility and entertainment.
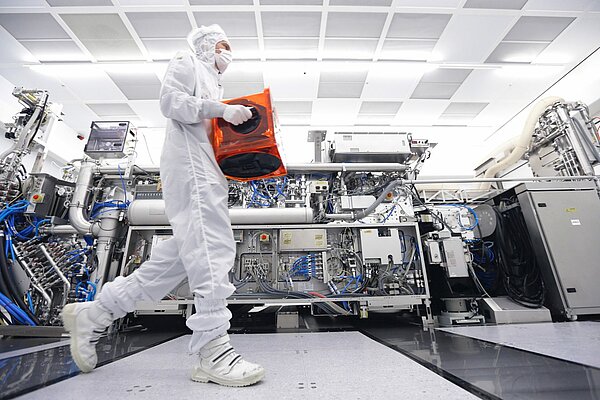
Brainport factor
Open innovation helps sustain ASML’s pace of invention
The concept of ‘open innovation’ that is characteristic of the Brainport Eindhoven region helps ASML sustain its pace of invention. This means that ASML develops its technology in close collaboration with partners inside and outside the company, sharing the rewards and the risks. This way of working ensures easy access to leading-edge knowledge and skills across a wide range of technologies, which partners on their turn can also use in other markets.
Sustainable relationships with suppliers
ASML relies heavily on its suppliers to develop, manufacture and deliver innovative parts for its systems, on time and with the right quality. It is ASML’s strategy to develop and manufacture those parts and modules that are unique for lithography in-house, both from a manufacturing and a development competence perspective. If this does not prove possible, supplier partnerships are established and well maintained. Contract manufacturers or original equipment manufacturing suppliers are mainly responsible for delivering modules that require non-unique manufacturing or development competencies. It is crucial that ASML builds a world-class supplier network. One of the company’s major priorities is to work with its suppliers to reduce the total cost of ownership of its systems while meeting its challenging quality standards.