World’s first iron fuel plant built by RIFT set to decarbonize industry
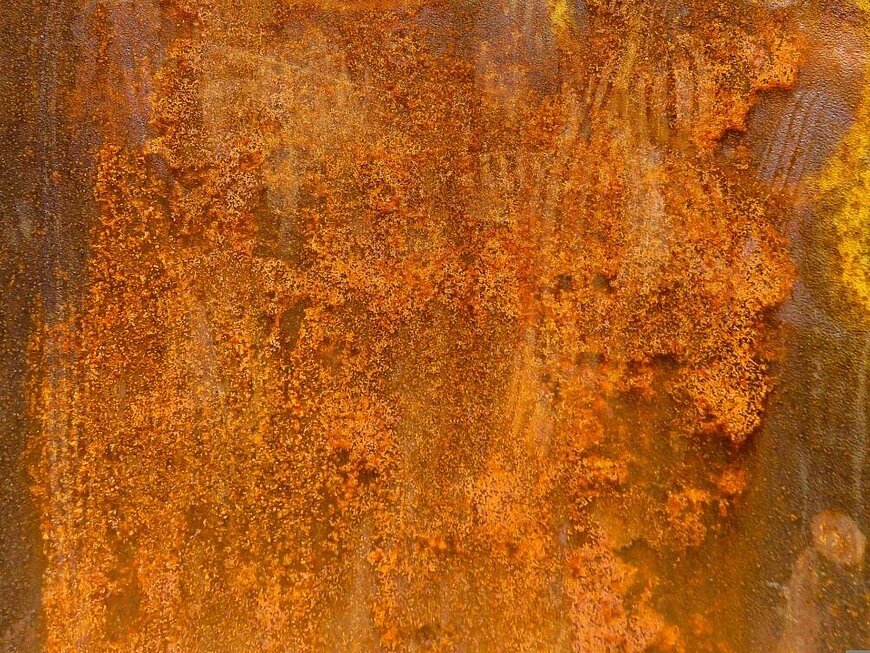
Anyone thinking about the energy transition soon associates that with electricity and hydrogen. But Renewable Iron Fuel Technology (RIFT), which sprang from the SOLID student team at Eindhoven University of Technology in the Netherlands, is convinced that iron fuel is also indispensable for a sustainable future. For industry, this circular fuel that the company produces is an ideal alternative to gas.
Recently, the start-up (which was founded in 2020) won the Gerard & Anton Awards: an award given to the most promising start-ups from the Brainport region. CEO Mark Verhagen talks about how the company is doing in this instalment of start-up of the day.
How does it work?
RIFT’s system works as follows: iron powder is burned in a boiler. This releases a lot of heat, e.g., for use in heat networks. What is left over is rust powder. You can use hydrogen to convert that back to iron powder, and in that way you “recharge” the powder and create a circular fuel.
Why does the world need iron fuel?
“Industry accounts for 52 percent of all CO2 emissions. It is still heavily reliant on fossil fuels, but the time has come for it to decarbonize. At present, there are two alternatives available to facilitate that: hydrogen combustion and electrification. However, the hydrogen network is not adequately in place as yet while electrification is not capable of meeting the needs of large companies all of the time. Which means that much of the puzzle basically remains unsolved. Iron fuel represents an ideal solution. That’s because you can easily adopt that technology in any location.”
How efficient is the use of iron powder compared to, for instance, hydrogen?
“One of the properties of iron powder is that you can easily store and transport it. Whereas hydrogen experiences efficiency losses during transport, this is scarcely the case with iron powder. That said, our technology does tend to lose slightly more of its efficiency during the production of the iron fuel. But ultimately, you do end up with a relatively high efficiency rate ranging from 65 to 81 percent.”
Which phase is RIFT currently in?
“We are in the ‘proof of concept’ phase. In the meantime, we have two plants up and running: Our production plant at the Energy Demo Field in Arnhem and our combustion plant in Helmond at Ennatuurlijk. At this point, we are collecting test results and if all goes according to plan, we will be able to share these with the general public in November.”
“Our goal is ultimately to save a gigatonne of CO2 per year by 2050. I hope that we will be making a major contribution to the global energy supply by then. Gas, oil and coal will then be a thing of the past and electricity, hydrogen as well as iron powder will be part of the energy supply of the future.”