TNO
Research and Development in Additive Manufacturing
TNO is an independent research institute with over 30 years of experience in additive manufacturing. The goal of TNO is to help the industry in their efforts to implement 3D printing through new technologies. The research institute focuses on three major areas of additive manufacturing: 3D printed food and pharma, polymer composite printing and printed electronics.
Next generation food & pharma printing
The TNO Food & Pharma Printing Expertise Group helps companies in developing innovative food and pharmaceutical products for their customers. The group compares the challenges in the market to existing commercial technologies and where gaps exists it uses equipment design, process control, system and software engineering to research and develop new innovative equipment concepts to fit the needs of the food and pharma industry. TNO has for instance developed a set-up for high-force and high-speed extrusion printing that exceeds commercially available limits. Their multi-nozzle printhead platform allows printing with multiple materials simultaneously. And their experimental printhead platform explores the potential of novel extrusion concepts for continuous and large-scale production. TNO can be a consortium partner or a private partner to advance your 3D-printing capabilities.
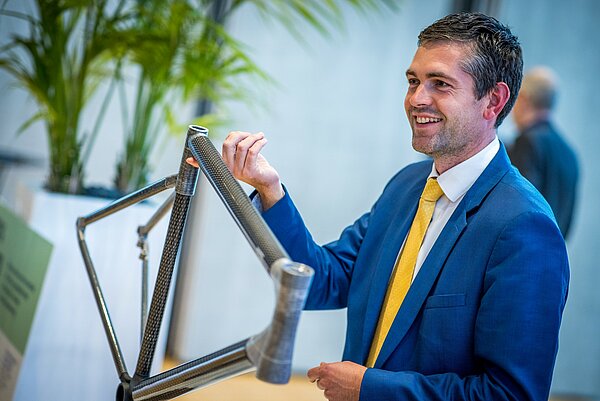
Challenging plastics in the Brightlands Materials Center
When you 3D print with polymers, the challenge is the mechanical strength of the resulting product. Traditional injection moulding technology typically produces a stronger end product. With the innovations of Brightlands Materials Center 3D printing with reinforcing continuous fibers inside of the polymer offers now a stronger, lightweight product. Through unique design optimalization and parts integration further weight savings can be reached. Compared to traditional manufacturing this provides aerospace and other mobility markets huge benefits, as weight reduction means cost reduction through fuel savings and CO2 reduction.
Additional to light weighting, circular business models can be further explored because resource recovery of thermoplastic composites manufactured by Continuous Fiber Additive Manufacturing is relatively easy compared to traditional thermoset composites.
Flexible and printed electronics by Holst Centre
Combining printed circuits and devices with traditional electronic components like LEDs and chips, printed electronics enables large-area, flexible and freeform applications that can be manufactured in high volumes using roll-to-roll printing and assembly processes. Holst Centre is a pioneer in flexible and printed electronics. The electronic circuits are created using printed electronics technologies as part of the 3D printing production process, embedding them directly into structural components. 3D printed electronics is currently in the early stages of development and promising markets are smart wearables for the medical industry, defence, and consumers. But also small-series semiconductor packaging or free-form antennas for automotive, communications and defence can benefit from this new technology.